There are many questions that supply chain and project managers must ask themselves when it comes to optimizing flow, minimizing shortages, reducing transportation costs, reducing orders, and timing delivery.
The outputs of DRP can help supply chain managers answer questions such as:
- Which products will we need?
- What quantity of each product will we need?
- Where are those finished goods needed?
- What quantity do we have on-hand and how much do we need to produce?
The goal of DRP is to ensure that the right quantity of goods are produced in the manufacturing facilities and sent to various warehouses to fulfill customer orders.
Distribution Requirements Planning (DRP) in Supply Chain
The Distribution Requirements Planning process ensures that goods are delivered in the most efficient manner. This includes considering the quantity of the various materials required in production and the direct location that it is needed to arrive at in a given time.
Distribution requirements planning will benefit operations as a whole by increasing efficiency in the following areas:
- Faster Decision Making
- Utilization of Demand Forecasting
- Planning Initiation Accuracy
- Cost Awareness
- Customer Service Enhancement
- Push or Pull Method
The DRP process can either use a push or pull method. First, the pull method involves demands for finished goods shifting upward throughout the system to fulfil customer orders. Although management controls the amount of goods available, the distribution inventory management is challenging because all orders are considered new to the supplying location as the demand is flowing upward, which is otherwise known as the “Bullwhip Effect”. This effect reflects the increasing demand forecast inaccuracies as orders move up the supply chain
The push method is the opposite of the pull method - instead, goods are sent downward through the system. The advantage of this method is that it allows lower costs, but can be disadvantageous when the central planning and demand are not on the same page at all times.
As distribution requirements planning is gradually being implemented into the production facilities and manufacturing operations, there is a drastic increase in production efficiency, accuracy, and order fulfillment.
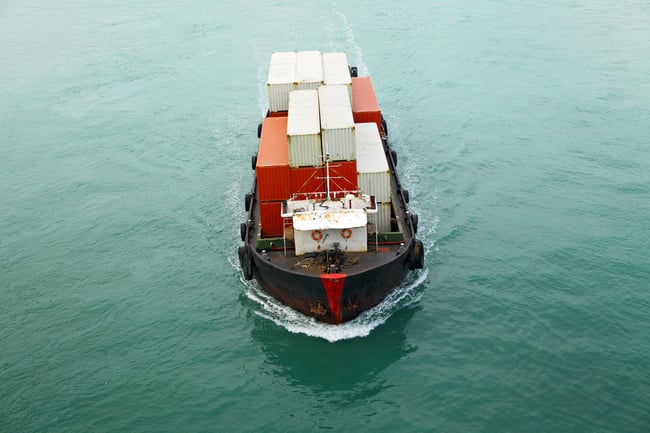
APS & DRP in the Supply Chain
Distribution Requirements Planning (DRP) is a vital aspect of manufacturing operations. Tools such as advanced planning and scheduling systems (APS) allow for increased insight into the distribution process to optimize it. An APS system such as PlanetTogether offers the following capabilities:
- Supply Scenarios - What-If Scenarios allow supply chain managers to create and compare various sourcing options to meet changing demands. This software allows users to create realistic and efficient supply plans.
- KPI Optimization - PlanetTogether APS allows managers to analyze the impact of changing distribution plans on their key performance indicators (KPIs) of interest. The software also provides a way to optimize the weighted business key performance indicators to evaluate the best distribution plan.
- Smart Sourcing - An advanced planning and scheduling system allows you to consider availability, transfer times, and costs when creating the most efficient supply network.
These capabilities are extremely beneficial to distribution and production and will gradually increase production and distribution efficiency for production facilities around the globe.
I can just say that every process, from order entry to warehouse, scheduling, materials planning, and so on have ALL become more responsive and able to plan better than ever.
CHUCK DIPIETRO, DIRECTOR OF PROCUREMENT & PLANNING, BEMA INCORPORATED
Advanced Planning and Scheduling (APS) Software
Advanced Planning and Scheduling Softwares have become a must for modern-day manufacturing operations as customer demand for increased product assortment, fast delivery, and downward cost pressures become prevalent. These systems help planners save time while providing greater agility in updating ever-changing priorities, production schedules, and inventory plans. APS systems can be quickly integrated with an ERP/MRP software to fill the gaps where these systems lack in terms of planning and scheduling flexibility, accuracy, and efficiency.
With PlanetTogether APS you can:
- Synchronize supply with demand to reduce inventories
- Enable scenario data-driven decision-making
- Create optimized schedules that balance production efficiency and delivery performance
- Maximize throughput on bottleneck resources to increase revenue
- Provide company-wide visibility of resource capacity
The implementation of an Advanced Planning and Scheduling (APS) Software will take your manufacturing operations to the next level of production efficiency by taking advantage of the operational data you already possess in your ERP system. APS is a step in the right direction of efficiency and lean manufacturing production enhancement. Try out a free trial or demo!
Related Constraints Video
APS Resources