Have you ever wanted to predict what would happen if you changed part of your production schedule? PlanetTogether's What-If Scenarios feature allows you to see the effects of any changes made to the production schedule before they are implemented to allow you to make better business decisions.
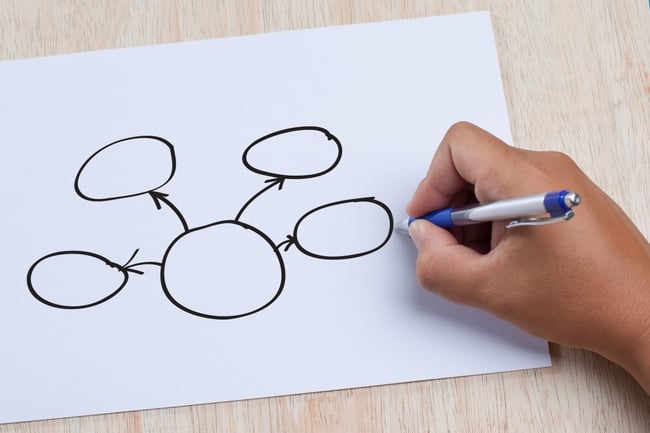
What-If Scenarios contain all of the data for the factory model including plants, departments, resources, items, inventories, operations, and financial information. This data can be manually entered or imported from an ERP system.
What-If Scenarios can be used in conjunction with the Key Performance Indicators (KPIs) pane to allow better decision making. This allows planners and schedulers to see the impact of various changes made to the production schedule on a number of specific KPIs.
Use What-If Scenarios to Simulate:
- Adding resources
- Adding overtime capacity
- Changing optimization rules
- Changing release rules
- Scheduling maintenance
For example, you can see the impact of scheduling maintenance for a machine that is running slower than usual and compare it to adding overtime capacity intervals to meet your production goals.
We work with the what-if scenarios until we find the one that works best for us and then take the new schedule live.
BRUCE HAYS, DIRECTOR OF MANUFACTURING, J&J SYNTHES
Finally, once the best What-If Scenario is found, it can easily be converted to the Live Scenario with the click of a button. This feature will save you time and energy when making changes to the production schedule to maximize profits and cut costs.
Why You Should Use What-If Scenarios
- Plan for the future - You can make changes to the production schedule in a What-If environment without disrupting your current schedule. This will allow you to make better decisions based on the effects of those potential changes.
- Evaluate the best schedule - With this feature, you can look at the different KPIs for each potential production schedule to decide which will have the best outcome for your company. Any number of What-If Scenarios can be created and compared.
- Quickly implement changes - Once the best schedule is chosen, it can easily be converted to the Live Scenario with the click of a button.
What-If Scenarios are a feature within PlanetTogether’s Advanced Planning and Scheduling (APS) software that allows you to generate hypothetical schedules and locate the most advantageous one that pertains to efficiency, waste elimination, and potential bottlenecks within the operation.
Advanced Planning and Scheduling (APS) Software
Advanced Planning and Scheduling Softwares have become a must for modern-day manufacturing operations as customer demand for increased product assortment, fast delivery, and downward cost pressures become prevalent. These systems help planners save time while providing greater agility in updating ever-changing priorities, production schedules, and inventory plans. APS Systems can be quickly integrated with an ERP/MRP software to fill the gaps where these systems lack planning and scheduling flexibility, accuracy, and efficiency.
With PlanetTogether APS you can:
- Create optimized schedules that balance production efficiency and delivery performance
- Maximize throughput on bottleneck resources to increase revenue
- Synchronize supply with demand to reduce inventories
- Provide company-wide visibility to resource capacity
- Enable scenario data-driven decision making
The implementation of an Advanced Planning and Scheduling (APS) Software will take your manufacturing operations to the next level of production efficiency by taking advantage of the operational data you already possess in your ERP system. APS is a step in the right direction of efficiency and lean manufacturing production enhancement. Try out a free trial or demo!
Related What-If Video
APS Resources