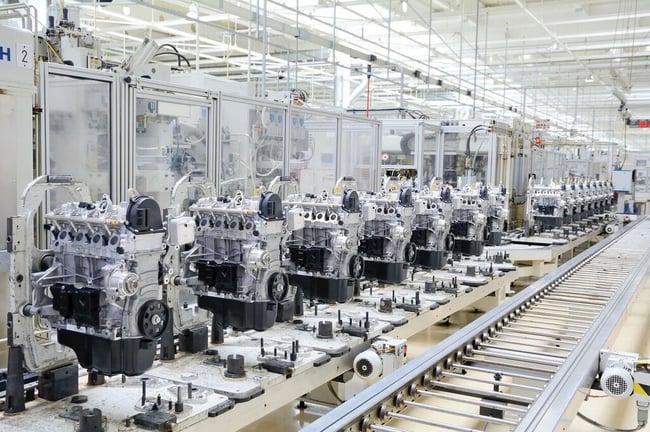
In recent years, much attention has been placed on lean manufacturing: the active elimination of waste from any manufacturing process with the objective to maximize value to the customer. Traditionally, this has meant getting rid of excess inventory, creating a continuous flow in production, organizing work groups logically, simplifying the manufacturing process, just-in-time raw materials delivery, and minimizing defects and waste.
However, major shifts in manufacturing are occurring, which requires shifts in manufacturing strategies. Now more than ever, customers have higher standards in terms of fast delivery, customization of products and low costs. The next step in bringing a competitive advantage to your company is building upon lean manufacturing methods by applying an agile manufacturing methodology.
What is Agile Manufacturing?
Agile Manufacturing involves putting even more emphasis on providing a rapid response to changing customer demands. In order to maintain a competitive advantage within the market, manufacturing organizations must find a way to satisfy their customer demands within a short time frame. When using an agile framework, local manufacturing becomes advantageous in satisfying customers quickly with personalized products and services.
While agile manufacturing can employ similar techniques as lean manufacturing, they are not the same. Lean manufacturing puts a strong focus on eliminating waste to reduce costs and shorten the lead time of items. Agile manufacturing can certainly use lean techniques, but the strategy is focused on processes that are flexible to adapt to changes quickly.
Existing organizational structures, however, can be an obstacle to becoming truly agile and should be analyzed holistically.
Key Factors of Agile Manufacturing Explained
There are 5 key factors to consider when thinking of agile manufacturing: customer focused product design, technology, supply chain cooperation, employee training, and full company involvement.
1. Customer Focused Product Design
Consumers expect more personalized attention than ever before. This extends not only to rapid service but also to the products they order. An agile organization will stay on top of market demand and design the production process so that desired product variations are accounted for in the production planning.
2. Technologies
Quick response to market demand is difficult without an integrated technology environment. Information flow needs to be accurate, in real-time, and shared across all departments. This enables all areas of an agile manufacturing organization to fulfill orders correctly and efficiently. Everyone involved, from sales teams and customer service agents to line workers, needs to be on top of reliable production and market information. This information, of course, must be supported with the ability to act upon it quickly.
3. Supply Chain Cooperation
Agile methodologies involve both internal teams and external alliances. Suppliers can only respond quickly when armed with adequate production flow information, and shippers need to know what to expect for rapid delivery to end-users. It is helpful to involve new alliances and supply chain partners with some part of the product build-out or design to ensure adequate collaboration at each step. In sum, your entire supply chain must be viewed as a single entity and be aligned with your customer demand.
4. Employee Training
Employee training for agile manufacturing involves learning basic information on new production practices in addition to education in a new, agile, and customer-driven format. Expecting employees to understand the rapid changes and adaptations they will be involved in requires intensive training and an acknowledgement that a cultural change is occurring. Your team will then have the sills required to quickly solve problems in the events of unexpected disruptions.
5. Full Company Involvement
An agile transition will not work if it is relegated to the team level. Company structure needs to be part of the transformation to becoming agile. The changeover usually works better if an operation is introducing a new plant or expanding an older one. That way, the focus can be on bringing the entire new area up to agile standards. Requesting workers handle operations as they did previously while expecting them to concentrate on setting up an agile manufacturing module is doomed to fail.
Implementing Agility with Advanced Planning and Scheduling Systems
Moving an organization to become an agile manufacturing company with swift response to customers, offering them what they want when they want it, requires planning.
It will be a path involving everyone in the company and it will change the old order dramatically, but it is rewarding, supports growth, and provides a huge competitive advantage to the brave managers that decide to walk down that path.
In recent years, technological advances have enabled companies to increase their agility. An Advanced Planning and Scheduling (APS) software allows organizations to quickly adapt their production schedules to respond to unexpected changes. PlanetTogether's APS system will allow you organization to quickly generate and re-generate production schedules that will allow you to rapidly adjust to changes in demand.
PlanetTogether enables us to provide a quality product to our customers in a timely manner.
GREGORY VAN LEIRSBURG, PRODUCTION SCHEDULER, STANDARD PROCESS SUPPLEMENTS
Advanced Planning and Scheduling (APS) Software
Advanced Planning and Scheduling Softwares have become a must for modern-day manufacturing operations as customer demand for increased product assortment, fast delivery, and downward cost pressures become prevalent. These systems help planners save time while providing greater agility in updating ever-changing priorities, production schedules, and inventory plans. APS Systems can be quickly integrated with an ERP/MRP software to fill the gaps where these systems lack planning and scheduling flexibility, accuracy, and efficiency.
With PlanetTogether APS you can:
- Create optimized schedules that balance production efficiency and delivery performance
- Maximize throughput on bottleneck resources to increase revenue
- Synchronize supply with demand to reduce inventories
- Provide company-wide visibility to resource capacity
- Enable scenario data-driven decision making
The implementation of an Advanced Planning and Scheduling (APS) Software will take your manufacturing operations to the next level of production efficiency by taking advantage of the operational data you already possess in your ERP system. APS is a step in the right direction of efficiency and lean manufacturing production enhancement. Try out a free trial or demo!
Related What-If Scheduling Video
APS Resources