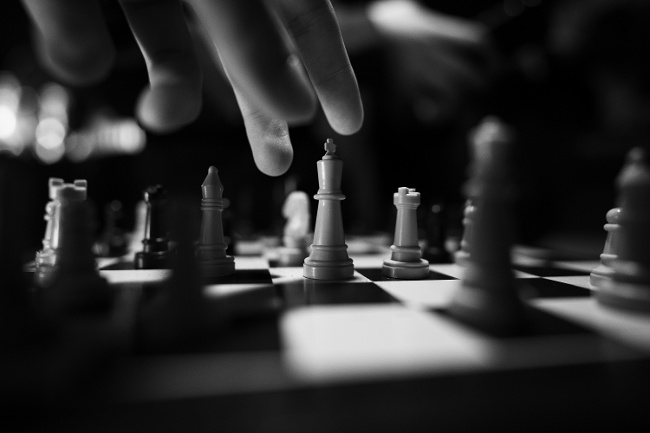
What is Operations Management?
Operations management pertains to the management of business practices that create goods and provide services. In manufacturing, this refers to all processes that transform raw materials into finished goods.
Operations management processes such as planning, organizing, and supervising ensure for a much higher profitability and improvement of efficiency within a manufacturing operation. The overall goal of operations management is to utilize resources, labor, material, and equipment effectively in order to match supply and demand.
When operations management is implemented, key adjustments that are made to help support the company reach its strategic goals. These goals are met through understanding the most important principles of operations management.
The 10 principles of operations management were presented by Randall Schaeffer at an APICS conference. It was said that the violation of these principles were the reason why many manufacturing organizations in the U.S. were struggling.
10 Principles of Operations Management
The 10 principles of Operations Management include the following:
- Reality - Operations management should focus on the overall problem, instead of just the tools and techniques. This is because no tool in itself will be able to present a universal solution to all problems that can be encountered.
- Organization - Within a production facility, everything within the operation is interconnected. All of these elements have to be consistent and predictable, or else the operation will not be able to achieve an outcome for profit.
- Humility - Trial and error processes are extremely costly, which is why it is important for managers to understand that they have limitations. Knowing what your limitations are will allow you to save money and time and help production in the long run.
- Success - While there are various definitions of what success is within your production facility, the interest of your customer should always be taken into account. If you wish to be successful, you have to keep your customers happy and coming back.
- Accountability - Being accountable is key within running a manufacturing operation. Managers are expected to be able to set rules and metrics while also checking on a frequent basis that these goals are being met. This keeps workers accountable and allows them to put in the necessary efforts to meet those goals.
- Causality - Problems are very similar to symptoms, in which these two things usually have underlying causes. In order to rid yourself of the problem forever, you have to remove the underlying cause as well.
- Fundamentals - In operations management, the Pareto Rule of Efficiency (aka the 80/20 rule) is applicable as 80% of success will come from maintaining current processes while 20% comes from applying new techniques to the processes.
- Variance - The variance of demand signals can be problematic for manufacturing facilities. However, variance in terms of the techniques and processes put in place should be encouraged to foster creativity and allow for a better response to other sources of variation.
- Managed passion - Passionate employees are your most valuable asset. They are the key to long-term performance and success of the company. It is crucial to have motivated managers as that can instill a sense of passion in their employees.
- Change - Sometimes, change is good. With new theories and solutions available to manufacturing operations, being open to change will ensure that you maintain stable operations in the long run.
The Importance of Operations Management
Operations Management is an essential aspect of any business as it affects and is affected by every business aspect. PlanetTogether's Advanced Planning and Scheduling (APS) Software can help operations managers navigate the challenges of implementing processes related to operations management.
This software allows manufacturing facilities to have a visual representation of their production schedule and can help with reducing waste, increase profits, and boost production efficiency. PlanetTogether APS can be implemented in production facilities around the globe to help them take their operation to the next level.
With PlanetTogether, we now have a consistent tool for our planning and scheduling. PlanetTogether APS is used by most of our departments, from supervisors, production planners, purchasing, IT staff, and management.
BRUCE HAYS, DIRECTOR OF MANUFACTURING, J&J SYNTHES
Advanced Planning and Scheduling (APS) Software
Advanced Planning and Scheduling Softwares have become a must for modern-day manufacturing operations as customer demand for increased product assortment, fast delivery, and downward cost pressures become prevalent. These systems help planners save time while providing greater agility in updating ever-changing priorities, production schedules, and inventory plans. APS Systems can be quickly integrated with an ERP/MRP software to fill the gaps where these systems lack planning and scheduling flexibility, accuracy, and efficiency.
With PlanetTogether APS you can:
- Create optimized schedules that balance production efficiency and delivery performance
- Maximize throughput on bottleneck resources to increase revenue
- Synchronize supply with demand to reduce inventories
- Provide company-wide visibility to resource capacity
- Enable scenario data-driven decision making
The implementation of an Advanced Planning and Scheduling (APS) Software will take your manufacturing operations to the next level of production efficiency by taking advantage of the operational data you already possess in your ERP system. PlanetTogether is a step in the right direction of efficiency and lean manufacturing production enhancement. Try out a free trial or demo!
Related What If Video
APS Resources