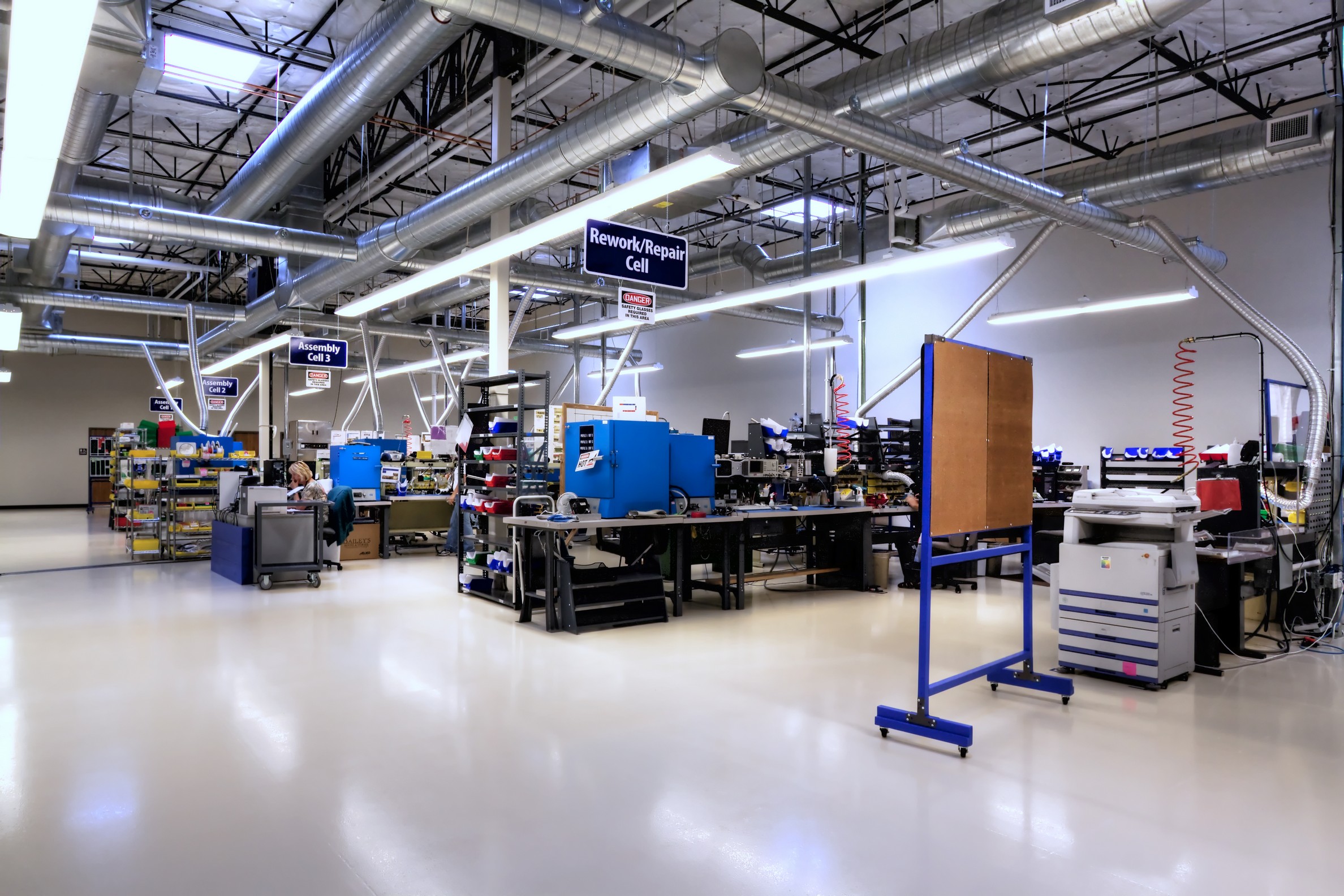
Though countless factories have adopted lean manufacturing over the years, the truth is that removing waste from manufacturing is no new concept. Since the height of the Industrial Age, profit-seeking manufacturers have looked for ways to generate higher quantities of product with less out-of-pocket expense. From Eli Whitney in the 1850s to the Toyota Company a century later, lean manufacturing has taken many bounds towards becoming the formulaic process it is today.
Perhaps one of the largest bounds was the Toyota Company’s identification of the “Seven Wastes” of lean manufacturing. In Toyota’s eyes, the Seven Wastes are categories of unproductive manufacturing practices that take away from a company’s ability to produce at its highest efficiency. Today we will be offering a short overview of each of these Seven Wastes along with a summary of the ways that advanced planning software can help reduce those wastes.
Overproduction
Quite simply, overproduction is manufacturing product too far in advance or too far in excess of customer demand. This leads to waste of time, space, material, labor, and ultimately, money.
How can advanced planning software help?
Advanced planning software, such as PlanetTogether, takes detailed record of your company’s processes—including but not limited to the amount of time, labor, and material needed to successfully complete a product—and converts it into raw data. This raw data is then used to compute production schedules based on actual orders and forecasts. Production is started when needed and at the exact quantities needed to avoid overproduction. Only producing and buying enough for what is needed, when needed, will lead to reduced inventory, meaning more money in your pocket at the end of the day.
Waiting
The second waste in Toyota’s list is waiting. This refers to time, labor, and money being wasted due to insufficient amounts of material. Lean manufacturing states that, ideally, all factory processes should be fluid and continuous.
How can advanced planning software help?
Advanced scheduling software assists users with quick decision making through predictive analytics. If a floor manager can foresee a stall in raw material delivery, he or she can make a proper decision to accommodate that delay or a buyer can expedite the material. In addition, visual operations charts allow facility managers to take note of the full scope of their orders at the click of a mouse. This means more accurate completion time predictions, and less time waiting for a product to make its way through the funnel.
Transportation
From a lean manufacturing perspective, transportation is waste-inducing practice. Moving a product between manufacturing processes adds no value, can be expensive, and can cause damage or product deterioration. It is most efficient to complete all processes within one facility with as little movement as possible.
How can advanced planning software help?
A planning system can help avoid material movement both between facilities and between locations within one facility. In situations where product can be produced at multiple locations, the APS system can choose the location that is closest whenever possible. Also, by producing closer to the delivery date, the movement of WIP in and out of storage can be minimized to save on material movement.
Excess Processing
People and equipment are a factory’s ultimate asset—use them efficiently, and your profits and customer service are maximized. If the wrong equipment, tools, or people are selected to do the work then scrap, delays, or poor quality will be the result.
How can advanced planning software help?
Advanced scheduling software catches and tracks all company routing data, allowing users to make intelligent processing decisions based on past processes (machine or employee) that were most successful—the best people and equipment are chosen to do the job.
That concludes the first half of our lean manufacturing wastes recap. If you would like to continue learning about the Seven Wastes, tune into our blog next Tuesday, June 30th for the second half of this series.
Thank you for reading. We look forward to seeing you soon.
Related Lean Manufacturing Video
APS Resources
Topics: Factory Scheduling, Advanced Planning and Scheduling, Lean Manufacturing
LEAVE A COMMENT