Behavioral Economics Principles in Scheduling Decisions
Every decision made within the supply chain has a direct impact on the quality of patient care and the success of the business. As a Supply Chain Manager in a medical manufacturing facility, you understand the complexities involved in scheduling production tasks, managing resources, and optimizing workflows.
In recent years, there has been a growing recognition of the importance of incorporating principles from behavioral economics into scheduling decisions. By understanding how human behavior influences decision-making, supply chain managers can design schedules that not only maximize efficiency but also improve employee morale and satisfaction.
In this blog, we will explore the application of behavioral economics principles in scheduling decisions, with a focus on integration between scheduling software like PlanetTogether and ERP, SCM, and MES systems such as SAP, Oracle, Microsoft, Kinaxis, and Aveva.
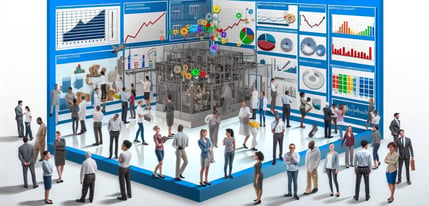
Behavioral Economics in Scheduling
Behavioral economics is a field of study that combines insights from psychology and economics to understand how individuals make decisions. Traditional economic theory assumes that individuals are rational actors who make decisions based on maximizing their utility. However, behavioral economics recognizes that human behavior is often influenced by cognitive biases, emotions, and social factors.
When it comes to scheduling decisions in a medical manufacturing facility, several behavioral economics principles come into play:
Loss Aversion: People tend to strongly prefer avoiding losses over acquiring gains of equal value. In scheduling decisions, this means that workers may be more motivated to meet deadlines to avoid the negative consequences of delays, rather than focusing solely on the potential benefits of completing tasks ahead of schedule.
The Endowment Effect: People tend to value items more highly simply because they own them. In the context of scheduling, this principle suggests that workers may be more invested in tasks that they have been assigned, leading to increased productivity and commitment.
Social Norms: People are strongly influenced by the behavior of others and the norms of their social group. In scheduling decisions, this means that workers may be more likely to adhere to schedules and deadlines if they perceive that their colleagues are doing the same.
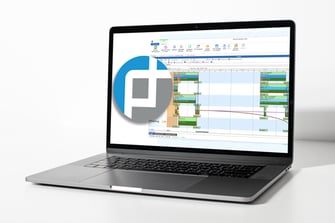
Integrating Behavioral Economics Principles with Scheduling Software
To effectively incorporate behavioral economics principles into scheduling decisions, supply chain managers can leverage advanced scheduling software like PlanetTogether, integrated with ERP, SCM, and MES systems such as SAP, Oracle, Microsoft, Kinaxis, and Aveva. Here's how:
Loss Aversion and Deadline Management
- Utilize scheduling software to set clear deadlines for production tasks, taking into account lead times, resource availability, and customer demand.
- Implement alerts and notifications within the software to remind workers of impending deadlines and the potential consequences of delays.
- Integrate data from ERP systems to provide real-time updates on inventory levels and customer orders, enabling proactive scheduling adjustments to avoid stockouts and backorders.
The Endowment Effect and Task Ownership
- Empower workers by allowing them to have input into the scheduling process through collaborative planning features in scheduling software.
- Provide visibility into the entire production schedule, allowing workers to see how their tasks fit into the broader workflow and understand the importance of timely completion.
- Integrate MES systems to track individual worker performance and provide feedback on productivity, fostering a sense of ownership and accountability for assigned tasks.
Social Norms and Peer Influence
- Foster a culture of accountability and collaboration by highlighting successful scheduling practices and recognizing teams that consistently meet or exceed targets.
- Utilize social features within scheduling software to facilitate communication and knowledge sharing among workers, enabling peer support and mentorship.
- Integrate feedback mechanisms to solicit input from workers on schedule effectiveness and areas for improvement, fostering a sense of collective responsibility for optimizing workflows.
Incorporating behavioral economics principles into scheduling decisions can have a profound impact on the efficiency and effectiveness of a medical manufacturing facility's supply chain. By leveraging advanced scheduling software like PlanetTogether integrated with ERP, SCM, and MES systems, supply chain managers can design schedules that not only maximize productivity and resource utilization but also promote employee engagement and satisfaction.
By understanding the behavioral motivations behind scheduling decisions, supply chain managers can unlock new opportunities for innovation and improvement in medical manufacturing operations.
As a Supply Chain Manager, embracing the principles of behavioral economics in scheduling decisions can be the key to unlocking the full potential of your supply chain and driving sustainable growth in your organization. With the right combination of advanced scheduling software and integrated systems, you can create a dynamic and responsive supply chain that delivers superior outcomes for both your business and your customers.
Are you ready to take your manufacturing operations to the next level? Contact us today to learn more about how PlanetTogether can help you achieve your goals and drive success in your industry.
LEAVE A COMMENT