Digital Supply Chain Platforms for End-to-End Visibility and Collaboration
In today's rapidly evolving market landscape, effective supply chain management is crucial, particularly for supply chain managers working in the food and beverage industry. The challenge lies in ensuring the timely delivery of products while managing fluctuating consumer demands, regulatory requirements, and production complexities.
The integration of digital supply chain platforms, such as PlanetTogether and various ERP, SCM, and MES systems like SAP, Oracle, Microsoft, Kinaxis, and Aveva, provides the key to achieving seamless end-to-end visibility and collaboration.
In this blog, we'll explore the importance of digital supply chain platforms, their benefits, and how integrating them can empower supply chain managers in food and beverage manufacturing facilities to optimize their operations.
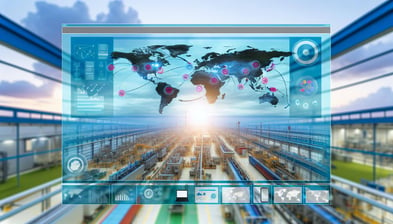
Understanding the Importance of Digital Supply Chain Platforms
Digital supply chain platforms are systems designed to unify and streamline supply chain activities. These platforms incorporate data analytics, artificial intelligence (AI), and other emerging technologies to deliver real-time visibility into the supply chain. They enhance the ability to forecast demand, optimize production schedules, and efficiently manage inventory levels.
Key benefits of adopting digital platforms include:
End-to-End Visibility: Access real-time data across all stages of the supply chain, enabling proactive decision-making and better handling of disruptions.
Improved Collaboration: Foster stronger relationships with suppliers, distributors, and internal teams by providing a unified platform for communication and data sharing.
Increased Agility: Swiftly adapt to market changes and customer demands through data-driven insights and predictive analytics.
Cost Reduction: Minimize production, transportation, and inventory costs by optimizing workflows and reducing wastage.
Compliance and Quality Control: Ensure regulatory compliance and maintain high-quality standards with transparent data across the supply chain.
Integration of PlanetTogether with ERP, SCM, and MES Systems
Integrating planning and scheduling software like PlanetTogether with enterprise resource planning (ERP), supply chain management (SCM), and manufacturing execution systems (MES) provides significant advantages for supply chain managers. Here’s how different system integrations can benefit food and beverage manufacturers:
PlanetTogether and ERP Systems
ERP systems such as SAP, Oracle, and Microsoft Dynamics are designed to centralize business processes like accounting, procurement, and inventory management. However, integrating an advanced planning and scheduling (APS) system like PlanetTogether provides additional features to enhance production efficiency:
Demand Forecasting: By leveraging ERP data and PlanetTogether’s APS capabilities, companies can build accurate demand forecasts, aligning production schedules with market needs.
Production Optimization: PlanetTogether allows dynamic production scheduling based on data from ERP systems, optimizing resources and reducing changeover times.
Real-Time Monitoring: Combining ERP data with PlanetTogether’s scheduling tool offers real-time visibility into work-in-progress and inventory levels, helping adjust production plans promptly.
PlanetTogether and SCM Systems
Supply chain management systems like Kinaxis focus on broader supply chain planning and optimization. Integrating PlanetTogether with SCM systems enables tighter control over the production stage:
Seamless Coordination: Coordinate production schedules with upstream and downstream supply chain partners, ensuring timely supply and delivery of materials.
Inventory Control: Maintain optimal inventory levels across multiple sites by synchronizing production schedules with demand forecasts.
Scenario Planning: Run simulations to assess the impact of potential supply chain disruptions and develop contingency plans.
PlanetTogether and MES Systems
Manufacturing execution systems like Aveva focus on managing and monitoring production on the shop floor. Integrating PlanetTogether with MES systems provides:
Shop Floor Visibility: Gain real-time visibility into production lines, enabling dynamic rescheduling to minimize delays.
Quality Assurance: Monitor production quality and ensure adherence to food safety regulations.
Performance Analysis: Analyze production performance to identify bottlenecks and inefficiencies, enabling continuous improvement.
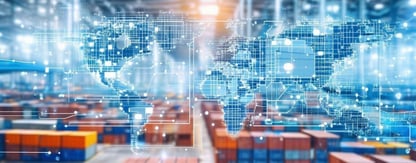
Best Practices for Integrating Digital Supply Chain Platforms
To successfully implement and integrate digital supply chain platforms, consider the following best practices:
Define Clear Objectives: Understand the specific business objectives to achieve with the platform. Whether it's reducing lead times or enhancing collaboration, setting clear goals helps prioritize efforts.
Cross-Functional Collaboration: Involve stakeholders from IT, production, procurement, sales, and finance departments to understand their needs and ensure seamless data flow across functions.
Data Standardization: Ensure data consistency across systems to avoid inaccuracies and miscommunication.
Change Management: Develop a robust change management strategy, including staff training and continuous support, to ease the transition.
Phased Implementation: Start with a pilot project before expanding the integration across the entire organization.
Continuous Improvement: Regularly assess the platform's performance and make adjustments based on evolving business needs.
Supply chain managers in the food and beverage industry face increasing challenges, from fluctuating consumer demands to regulatory pressures. However, the integration of digital supply chain platforms like PlanetTogether with ERP, SCM, and MES systems can transform these challenges into opportunities. By fostering end-to-end visibility and collaboration, supply chain managers can enhance agility, optimize production processes, and ultimately deliver superior products to consumers.
Adopting such platforms isn't just about keeping up with technology trends but strategically positioning your organization for success in a dynamic market. Are you ready to take your manufacturing operations to the next level? Contact us today to learn more about how PlanetTogether can help you achieve your goals and drive success in your industry.
LEAVE A COMMENT