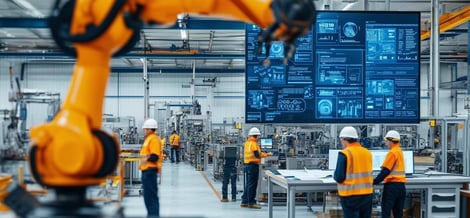
Using Buffer Stock Strategically in Production Plans: A Guide for Industrial Manufacturing Operations Directors
In today’s volatile manufacturing landscape, operations directors must juggle the complex demands of meeting production goals, maintaining quality, and minimizing costs. Buffer stock — the safety net between supply and demand — often plays a critical role in achieving these goals. However, when not managed strategically, it can lead to inefficiencies, increased holding costs, and waste.
This blog explores how to use buffer stock strategically in industrial manufacturing and how integrating advanced planning tools like PlanetTogether with enterprise systems such as SAP, Oracle, Microsoft, Kinaxis, or Aveva can streamline this process.
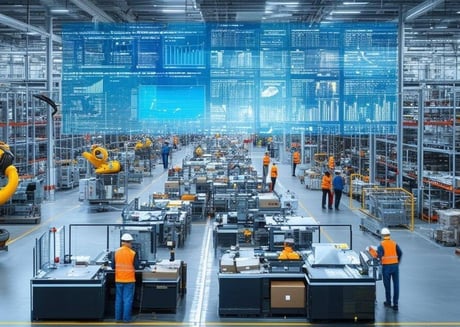
What Is Buffer Stock, and Why Does It Matter?
Buffer stock, also known as safety stock, serves as a safeguard against uncertainties in supply chains, production schedules, and market demands. While its primary purpose is to ensure smooth operations and avoid stockouts, poorly managed buffer stock can:
Inflate inventory carrying costs.
Tie up working capital.
Create overproduction risks in lean environments.
Strategically managing buffer stock requires striking a balance between maintaining enough inventory to meet unforeseen demand and minimizing excess inventory that leads to inefficiencies.
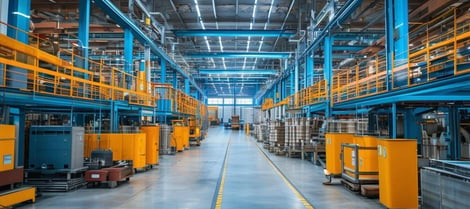
Challenges in Managing Buffer Stock in Industrial Manufacturing
Industrial manufacturing, with its intricate supply chains and diverse product lines, faces unique challenges in buffer stock management:
Demand Volatility: Forecasting inaccuracies and sudden changes in customer orders can lead to either stockouts or excessive buffer inventory.
Complex Supply Chains: With multiple suppliers, varying lead times, and global sourcing, aligning inventory levels with production schedules becomes a daunting task.
Production Bottlenecks: Unplanned downtimes, equipment failures, or labor shortages can disrupt production, increasing reliance on buffer stock.
Regulatory Compliance: In industries with strict regulations, maintaining buffer stock to ensure quality and compliance adds an extra layer of complexity.
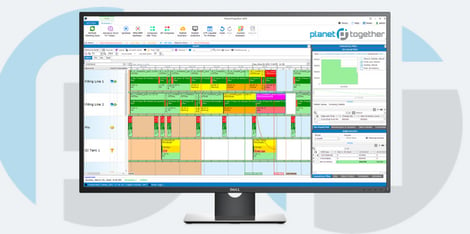
Technology in Strategic Buffer Stock Management
Effective buffer stock management in industrial manufacturing requires accurate data, advanced analytics, and seamless coordination between supply chain planning and production scheduling. This is where tools like PlanetTogether, integrated with ERP systems like SAP, Oracle, Microsoft, Kinaxis, or Aveva, come into play.
Key Benefits of Integration:
Enhanced Demand Forecasting: Integration with ERP systems allows PlanetTogether to access historical sales data, market trends, and customer behavior. This enables more accurate demand forecasting, reducing reliance on excessive buffer stock.
Real-Time Visibility: By connecting to systems like SAP or Aveva, manufacturers gain a real-time view of inventory levels, production schedules, and supply chain disruptions, enabling timely adjustments to buffer stock.
Optimized Production Scheduling: PlanetTogether’s advanced scheduling capabilities can synchronize production with inventory requirements, ensuring buffer stock is aligned with actual production needs.
Scenario Planning: With tools like Kinaxis or Microsoft Dynamics, operations directors can model "what-if" scenarios to assess the impact of demand spikes, supplier delays, or production disruptions, fine-tuning buffer stock strategies accordingly.
Regulatory Compliance: Integration ensures traceability and compliance by maintaining the right inventory levels of critical components, especially in regulated industries like automotive or aerospace.
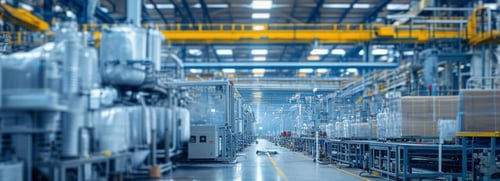
Strategies for Using Buffer Stock Effectively
To make buffer stock a strategic asset rather than a liability, consider the following approaches:
1. Segment Inventory by Criticality
Not all inventory items require the same buffer stock levels. Classify items based on their criticality to production and demand variability. High-priority items with unpredictable demand may warrant higher buffer stock, while low-priority items can be managed with minimal safety margins.
Technology Tip: Use PlanetTogether’s integration with SAP or Oracle to apply ABC or XYZ analysis for precise inventory segmentation.
2. Leverage Dynamic Safety Stock Models
Static safety stock levels can lead to inefficiencies. Instead, adopt dynamic models that adjust buffer stock based on real-time demand patterns, lead times, and production cycles.
Technology Tip: Tools like Kinaxis and Microsoft Dynamics allow for dynamic safety stock calculations, enabling manufacturers to adapt to changing market conditions seamlessly.
3. Align Buffer Stock with Production Bottlenecks
Identify stages in your production process prone to delays or bottlenecks and adjust buffer stock levels accordingly. This ensures that critical stages remain operational even during disruptions.
Technology Tip: PlanetTogether’s capacity planning features can pinpoint bottlenecks and help optimize buffer stock placement.
4. Integrate Supplier Performance Metrics
Suppliers play a key role in maintaining inventory levels. Track metrics like lead times, order accuracy, and reliability to determine how much buffer stock is needed for components sourced externally.
Technology Tip: Integrating Aveva with PlanetTogether provides a comprehensive view of supplier performance, enabling more informed buffer stock decisions.
5. Embrace Lean Manufacturing Principles
While lean principles advocate minimizing inventory, strategic buffer stock can coexist with lean practices. Use tools to strike a balance between efficiency and resilience.
Technology Tip: PlanetTogether’s integration with Oracle or SAP supports lean inventory practices while maintaining necessary safety stock levels.
The Strategic Edge: Combining Technology with Expertise
For operations directors in industrial manufacturing, strategic buffer stock management is no longer optional — it’s a necessity in today’s fast-paced market. By integrating tools like PlanetTogether with ERP systems such as SAP, Oracle, Microsoft, Kinaxis, or Aveva, manufacturers can achieve:
Greater visibility into supply chain and production processes.
Smarter, data-driven inventory decisions.
Enhanced agility to respond to disruptions.
Buffer stock, when managed strategically, can be a powerful tool to ensure operational resilience, meet customer demands, and drive cost efficiencies. However, this requires a data-driven approach and seamless integration between advanced planning tools and enterprise systems.
As an operations director, your ability to align technology with strategic goals can transform buffer stock from a reactive safety net into a proactive enabler of success. By leveraging the integration capabilities of tools like PlanetTogether with SAP, Oracle, Microsoft, Kinaxis, or Aveva, you can position your facility for sustained growth and competitive advantage.
Are you ready to take your manufacturing operations to the next level? Contact us today to learn more about how PlanetTogether can help you achieve your goals and drive success in your industry.