Integrating Circular Economy Practices in Manufacturing
As the world becomes increasingly aware of the urgent need for sustainability, the pressure on industries to adopt environmentally friendly practices is mounting. In the realm of manufacturing, the concept of a circular economy has emerged as a beacon of hope, promising not just reduced environmental impact, but also enhanced efficiency and profitability. For plant managers like you, navigating this shift towards circularity can be daunting. However, with the right strategies and tools in place, it's not only achievable but also highly beneficial.
In this blog, we'll look into the development and implementation of circular economy practices in manufacturing, focusing on how advanced planning systems, particularly the integration between PlanetTogether and leading ERP, SCM, and MES systems like SAP, Oracle, Microsoft, Kinaxis, and Aveva, can catalyze this transformation.
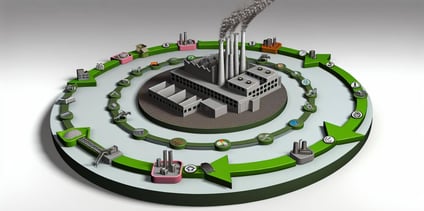
Circular Economy
Unlike the traditional linear economy, where resources are extracted, used, and disposed of, a circular economy aims to keep resources in use for as long as possible, extracting the maximum value from them and then recovering and regenerating products and materials at the end of their lifecycle.
Key principles of the circular economy include:
- Designing out waste and pollution
- Keeping products and materials in use
- Regenerating natural systems
These principles align closely with the goals of sustainability, offering a holistic approach to resource management and environmental stewardship.
Challenges in Implementing Circular Economy Practices in Manufacturing
While the benefits of transitioning to a circular economy are clear, the path to implementation is not without its challenges. Manufacturing plants often face the following hurdles:
- Legacy Systems: Outdated technology and siloed systems hinder the seamless flow of information and collaboration necessary for circularity.
- Supply Chain Complexity: Managing diverse and global supply chains adds layers of complexity, making it difficult to track and optimize resource flows.
- Resistance to Change: Embracing circular economy practices may require significant changes to established processes and mindsets, which can meet with resistance from stakeholders.
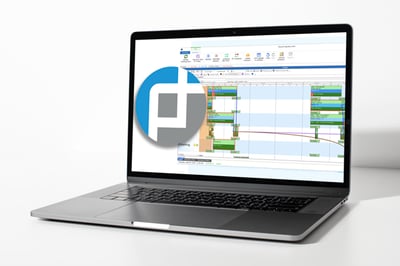
Integrating Advanced Planning Systems for Circular Economy
This is where advanced planning systems like PlanetTogether come into play. By integrating with ERP, SCM, and MES systems such as SAP, Oracle, Microsoft, Kinaxis, and Aveva, these planning tools offer a comprehensive solution to the challenges of implementing circular economy practices in manufacturing.
Data Visibility and Transparency: Integration allows for real-time access to data across the entire value chain, providing visibility into resource flows, inventory levels, and production processes. This transparency is essential for identifying areas of waste and inefficiency.
Demand Forecasting and Optimization: Advanced planning systems leverage sophisticated algorithms to forecast demand accurately, enabling manufacturers to produce only what is needed, thereby minimizing overproduction and reducing waste.
Resource Optimization: By optimizing production schedules and resource allocation, these systems help maximize the utilization of raw materials, energy, and other resources, ensuring they are kept in circulation for as long as possible.
Closed-Loop Supply Chains: Integration facilitates the creation of closed-loop supply chains, where materials are recycled and reused within the production process. This not only reduces the reliance on virgin resources but also minimizes waste generation.
Collaboration and Communication: Seamless integration fosters collaboration and communication among various departments and stakeholders, breaking down silos and promoting a shared vision of sustainability.
The development and implementation of circular economy practices in manufacturing present both challenges and opportunities for plant managers. By leveraging advanced planning systems like PlanetTogether and integrating them with leading ERP, SCM, and MES systems, manufacturers can overcome obstacles and accelerate their journey towards sustainability.
Through enhanced visibility, optimization, and collaboration, these integrated solutions empower plant managers to design out waste, keep resources in circulation, and regenerate natural systems, thereby creating value not just for their organizations, but also for the planet and future generations.
Embracing the circular economy is not just a moral imperative but also a strategic necessity in today's rapidly changing business landscape. With the right tools and mindset, plant managers can lead the charge towards a more sustainable and prosperous future for the manufacturing industry.
Are you ready to take your manufacturing operations to the next level? Contact us today to learn more about how PlanetTogether can help you achieve your goals and drive success in your industry.