Data-Driven Maintenance in Industrial Manufacturing
Plant managers face the constant challenge of optimizing operations to enhance margins in industrial manufacturing. The key to achieving operational excellence lies in leveraging cutting-edge technologies and fostering seamless integration between various systems.
This blog explores the transformative potential of data-driven maintenance, specifically focusing on its integration with leading ERP (Enterprise Resource Planning), SCM (Supply Chain Management), and MES (Manufacturing Execution System) platforms like PlanetTogether, SAP, Oracle, Microsoft, Kinaxis, and Aveva.
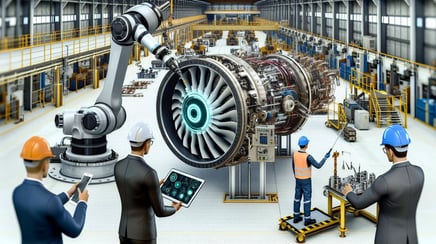
Data-Driven Maintenance
Data-driven maintenance represents a paradigm shift in the approach to equipment upkeep. Traditionally, maintenance activities followed a fixed schedule, often leading to unnecessary downtime and increased costs. In contrast, data-driven maintenance utilizes real-time data from sensors, IoT devices, and other sources to predict equipment failures, schedule maintenance proactively, and optimize asset performance.

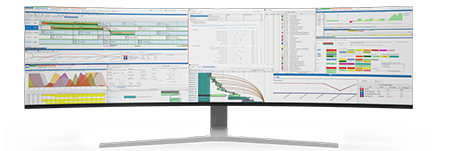
Integration with PlanetTogether
PlanetTogether, renowned for its advanced production planning and scheduling capabilities, becomes a linchpin in this transformative journey. By seamlessly integrating PlanetTogether with ERP, SCM, and MES systems, plant managers can unlock a new era of efficiency and cost-effectiveness.
SAP Integration
Harnessing the Power of SAP for Streamlined Operations: Integrating PlanetTogether with SAP ERP ensures a synchronized flow of data, facilitating accurate demand forecasting and inventory management.
Real-time Insights for Informed Decision-Making: The integration empowers plant managers with real-time insights into production schedules, enabling proactive maintenance strategies and minimizing disruptions.
Oracle Fusion Connection
Achieving Operational Synergy: Linking PlanetTogether with Oracle Fusion SCM fosters a seamless exchange of information, optimizing production schedules based on real-time demand and supply chain dynamics.
Enhanced Asset Reliability: Data-driven maintenance, supported by Oracle's robust infrastructure, ensures the reliability of critical assets, minimizing downtime and maximizing productivity.
Microsoft Dynamics 365 Collaboration
Unifying Processes for Holistic Management: Integration with Microsoft Dynamics 365 streamlines business processes, ensuring a holistic approach to data-driven maintenance.
AI-Driven Insights for Predictive Maintenance: Leveraging Microsoft's AI capabilities enhances predictive maintenance, allowing plant managers to address potential issues before they escalate.
Kinaxis RapidResponse Integration
Orchestrating Supply Chain Resilience: The integration of PlanetTogether and Kinaxis RapidResponse creates a responsive and resilient supply chain, adapting to dynamic market conditions.
Proactive Maintenance in an Agile Environment: Agile production schedules are complemented by proactive maintenance strategies, ensuring equipment reliability in a rapidly changing manufacturing landscape.
Aveva's Insightful Integration
Maximizing MES Efficiency: The integration of PlanetTogether and Aveva MES optimizes manufacturing execution, ensuring seamless coordination between production schedules and shop floor activities.
Continuous Improvement through Data Analytics: Aveva's analytics capabilities enhance data-driven decision-making, driving continuous improvement in maintenance processes.
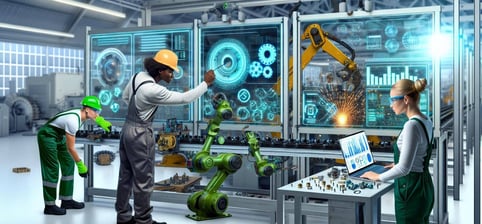
Benefits of Integrated Data-Driven Maintenance
Cost Reduction
Minimizing Downtime: Proactive maintenance strategies based on real-time data significantly reduce unplanned downtime, leading to cost savings.
Efficient Resource Allocation: Integrated systems enable optimal allocation of resources, minimizing idle time and operational costs.
Enhanced Productivity
Streamlined Operations: The integration of advanced planning tools with ERP, SCM, and MES results in streamlined operations, improving overall productivity.
Predictive Insights: Predictive maintenance ensures that equipment operates at peak efficiency, contributing to increased production output.
Improved Decision-Making
Real-Time Visibility: Integration provides plant managers with real-time visibility into all facets of operations, empowering them to make informed decisions.
Data-Driven Strategy: Leveraging data analytics facilitates strategic decision-making, aligning maintenance efforts with overarching business objectives.
Compliance and Quality Assurance
Regulatory Compliance: Integrated systems aid in ensuring compliance with industry regulations through accurate record-keeping and adherence to maintenance protocols.
Consistent Quality: Proactive maintenance contributes to consistent product quality, enhancing customer satisfaction and brand reputation.
In the pursuit of operational excellence, plant managers must embrace the transformative potential of data-driven maintenance. By integrating PlanetTogether with leading ERP, SCM, and MES systems, industrial manufacturing facilities can achieve a harmonized ecosystem where real-time data empowers decision-making, reduces costs, and enhances overall efficiency.
Embracing this synergy is not just a choice but a strategic imperative for those seeking to thrive in the competitive landscape of modern manufacturing.
Are you ready to take your manufacturing operations to the next level? Contact us today to learn more about how PlanetTogether and integrated scheduling solutions can help you achieve your sustainability goals and drive success in the industrial industry.
LEAVE A COMMENT