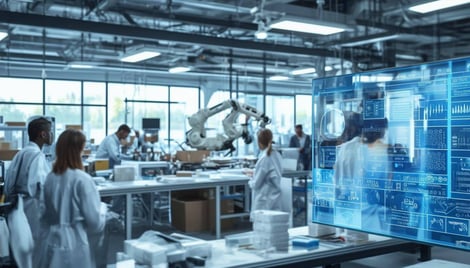
Unlocking Operational Excellence: Data Management Strategies for Medical Manufacturing
As Operations Directors, you are tasked with ensuring operational efficiency, compliance, and scalability while navigating a labyrinth of complex regulations and market demands. The integration of advanced planning and scheduling software like PlanetTogether with enterprise resource planning (ERP) systems such as SAP, Oracle, Microsoft, Kinaxis, or Aveva offers a transformative approach to mastering data management.
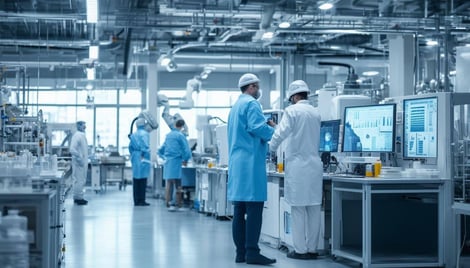
The Data Management Challenge in Medical Manufacturing
Medical manufacturing facilities generate vast amounts of data daily—from production schedules and inventory levels to quality control metrics and compliance documentation. This data is critical for:
Regulatory Compliance: Adhering to stringent standards like FDA, ISO 13485, and EU MDR.
Operational Efficiency: Streamlining workflows to reduce waste and improve productivity.
Quality Assurance: Ensuring every product meets the highest safety and performance standards.
Scalability: Supporting growth without compromising on quality or compliance.
However, the challenge lies in effectively managing and leveraging this data. Siloed systems, manual processes, and fragmented workflows often hinder visibility and decision-making.
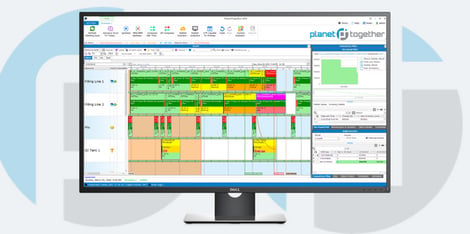
The Case for Integrated Solutions
Integrating PlanetTogether with ERP systems like SAP, Oracle, Microsoft, Kinaxis, or Aveva can bridge these gaps, creating a unified platform for data management and operational excellence. Here’s how:
Enhanced Visibility: Real-time data synchronization across systems provides a single source of truth.
Improved Decision-Making: Advanced analytics and reporting enable data-driven strategies.
Operational Agility: Seamless workflows and automated processes reduce lead times and increase flexibility.
Regulatory Confidence: Centralized documentation and traceability simplify compliance audits.
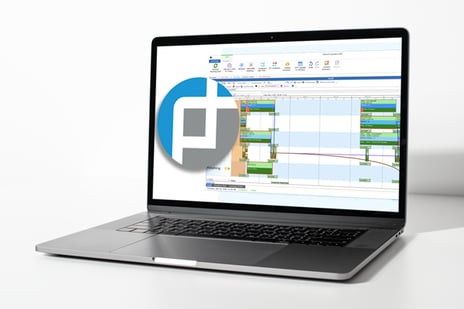
Key Benefits of Integration
1. Streamlined Scheduling and Production Planning
Medical manufacturing is characterized by high-mix, low-volume production, often with tight deadlines. Integrating PlanetTogether with an ERP system allows for dynamic scheduling that adapts to changing priorities and constraints. For example, if a batch of critical components is delayed, the system can automatically reschedule tasks to minimize disruption.
2. Inventory Optimization
Inventory management in medical manufacturing is critical, given the high costs and strict expiration requirements of materials. By connecting PlanetTogether with ERP systems like Microsoft Dynamics or Kinaxis, you can:
Monitor inventory levels in real-time.
Optimize reorder points and safety stock levels.
Minimize excess inventory and associated costs.
3. Enhanced Quality Control
Quality is paramount in medical manufacturing. Integration ensures that quality data from production lines is automatically captured, analyzed, and stored. This facilitates real-time quality checks and trend analysis, reducing the risk of defects and recalls.
For instance, integrating Aveva’s data management tools with PlanetTogether can provide predictive insights, helping you address potential quality issues before they escalate.
4. Regulatory Compliance Made Easy
Meeting regulatory requirements demands meticulous documentation and traceability. Integrated systems can:
Automate data collection and reporting.
Ensure consistent record-keeping.
Simplify audits with centralized data access.
SAP’s compliance modules, when combined with PlanetTogether, can streamline the creation of audit-ready reports, saving time and reducing errors.
5. Scalability and Future-Readiness
As your facility grows, so does the complexity of managing data. Integrated solutions provide a scalable foundation that can support new products, processes, and market expansions without compromising efficiency or compliance.
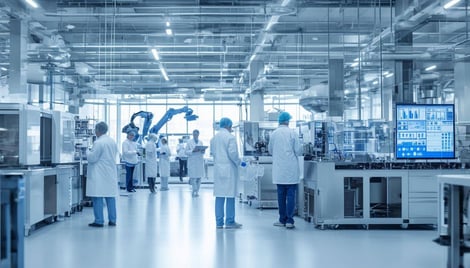
Overcoming Implementation Challenges
While the benefits of integration are clear, the path to implementation can be challenging. Common obstacles include:
Data Silos: Legacy systems often operate in isolation, making integration difficult.
Change Management: Employees may resist new workflows and technologies.
Cost and Time: Integration projects require significant upfront investment and resources.
To address these challenges:
Conduct a thorough needs assessment to identify pain points and integration priorities.
Partner with experienced vendors who understand the nuances of medical manufacturing.
Invest in employee training to ensure smooth adoption of new systems.
The Role of Operations Directors
As an Operations Director, your leadership is critical in driving the adoption and success of integrated data management solutions. Key responsibilities include:
Strategic Vision: Align integration projects with organizational goals and market trends.
Cross-Functional Collaboration: Work closely with IT, production, and quality teams to ensure seamless implementation.
Continuous Improvement: Monitor system performance and identify opportunities for further optimization.
Mastering data management is essential for staying competitive in the medical manufacturing industry. By integrating PlanetTogether with ERP systems like SAP, Oracle, Microsoft, Kinaxis, or Aveva, you can unlock new levels of efficiency, quality, and compliance. While the journey may involve challenges, the rewards—from streamlined operations to enhanced customer satisfaction—are well worth the effort.
As you navigate this transformation, remember that the key to success lies in strategic planning, cross-functional collaboration, and a commitment to continuous improvement. By embracing integrated solutions, you can not only meet today’s demands but also position your facility for future growth and innovation.
Are you ready to take your manufacturing operations to the next level? Contact us today to learn more about how PlanetTogether can help you achieve your goals and drive success in your industry.
LEAVE A COMMENT