Integration Strategies for Manufacturing IT
In food and beverage manufacturing, where consumer preferences, regulations, and market demands constantly evolve, maintaining a competitive edge requires a relentless pursuit of productivity. As manufacturing IT professionals in this sector, you understand the pivotal role technology plays in driving efficiency, reducing costs, and enhancing quality.
In this blog, we look into the realm of productivity improvement strategies, exploring how integration between advanced planning and scheduling (APS) solutions like PlanetTogether and Enterprise Resource Planning (ERP), Supply Chain Management (SCM), and Manufacturing Execution Systems (MES) can revolutionize operations in food and beverage manufacturing facilities.

The Challenges
Before we look into solutions, let’s address the challenges plaguing productivity in food and beverage manufacturing:
Complex Supply Chain Dynamics: The intricate network of suppliers, distributors, and retailers demands streamlined coordination to minimize disruptions and optimize resources.
Demand Volatility: Fluctuating consumer preferences and seasonal variations create demand uncertainties, making accurate forecasting and resource allocation a daunting task.
Regulatory Compliance: Stringent regulations governing food safety, labeling, and traceability necessitate meticulous record-keeping and adherence to standards.
Operational Inefficiencies: Inefficient production scheduling, equipment downtime, and wastage contribute to reduced productivity and increased costs.
Data Silos: Disjointed systems and disparate data sources hinder visibility across the supply chain, impeding informed decision-making.

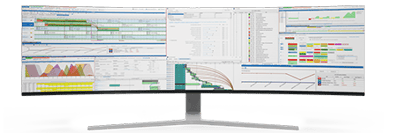
Integration Solutions
To address these challenges head-on, integration between PlanetTogether APS and leading ERP, SCM, and MES systems emerges as a game-changer. Let’s explore how this integration unlocks productivity improvement strategies:
Real-time Data Exchange
Integration enables seamless data flow between APS and ERP systems, providing real-time visibility into inventory levels, production schedules, and customer orders. This empowers planners to make informed decisions, anticipate demand fluctuations, and adjust production schedules accordingly.
Optimized Production Planning
By synchronizing PlanetTogether with ERP and MES systems, manufacturers can achieve optimized production planning. This involves aligning production schedules with resource availability, minimizing changeovers, and balancing workloads across production lines to maximize efficiency.
Enhanced Inventory Management
Integration with SCM systems facilitates accurate demand forecasting and inventory optimization. Manufacturers can maintain optimal inventory levels, reduce stockouts, and mitigate excess inventory costs by aligning production schedules with demand forecasts and supplier lead times.
Improved Traceability and Compliance
Integration between PlanetTogether and ERP/MES systems enables end-to-end traceability, from raw material procurement to finished product distribution. This ensures compliance with regulatory requirements and enhances product quality and safety through batch tracking and recall management.
Efficient Resource Utilization
Leveraging integration, manufacturers can optimize resource utilization by synchronizing production schedules with equipment availability and maintenance schedules. This minimizes downtime, enhances equipment efficiency, and prolongs asset lifespan, resulting in significant cost savings.
Streamlined Order Fulfillment
Integration between APS and ERP systems streamlines order processing and fulfillment by automating order creation, allocation, and scheduling. This reduces order cycle times, improves on-time delivery performance, and enhances customer satisfaction.
Data-driven Decision-making
By consolidating data from disparate systems into a unified dashboard, integration empowers stakeholders with actionable insights. Advanced analytics and reporting capabilities enable data-driven decision-making, facilitating continuous improvement initiatives and driving operational excellence.
In the fiercely competitive landscape of food and beverage manufacturing, productivity improvement strategies are paramount to success. Integration between advanced planning and scheduling solutions like PlanetTogether and ERP, SCM, and MES systems offers a transformative approach to driving efficiency, reducing costs, and enhancing quality.
By harnessing the power of integration, manufacturers can optimize production planning, enhance inventory management, ensure regulatory compliance, and streamline order fulfillment, paving the way for sustained growth and competitive advantage in the global marketplace. Embrace integration, unleash productivity, and propel your food and beverage manufacturing facility towards excellence.
Are you ready to take your manufacturing operations to the next level? Contact us today to learn more about how PlanetTogether can help you achieve your goals and drive success in your industry.
LEAVE A COMMENT