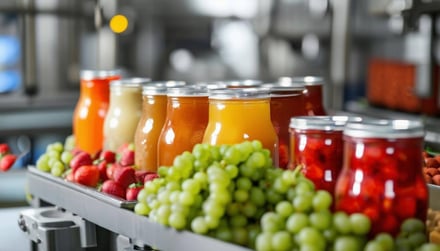
Understanding the Value Chain in Food and Beverage Manufacturing
Operational excellence hinges on a comprehensive understanding of the value chain. For Operations Directors, this means not only optimizing internal processes but also ensuring that every link in the chain—from procurement to delivery—functions seamlessly.
With growing consumer demands, tightening regulations, and the push for sustainability, leveraging advanced technologies like PlanetTogether and integrating them with enterprise systems such as SAP, Oracle, Microsoft, Kinaxis, or Aveva is critical to staying competitive.
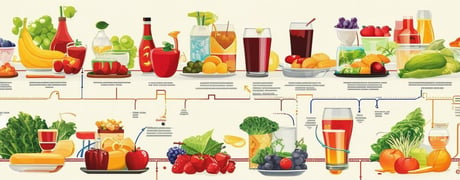
The Modern Food and Beverage Value Chain
The value chain in food and beverage manufacturing is multifaceted, encompassing procurement, production, logistics, and customer engagement. Operations Directors must manage several variables, including:
Raw Material Sourcing: Ensuring high-quality, cost-effective, and sustainable procurement.
Production Efficiency: Balancing capacity, minimizing waste, and meeting compliance standards.
Distribution and Logistics: Ensuring timely delivery and maintaining product integrity.
Customer Feedback Loops: Leveraging data to adapt to changing consumer preferences.
To address these challenges, the integration of advanced planning and scheduling (APS) systems like PlanetTogether with robust ERP platforms can drive transparency and efficiency across the value chain.

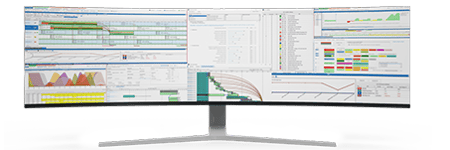
The Role of Technology in Value Chain Optimization
Breaking Down Silos with Integrated Solutions
One of the most significant barriers to value chain optimization is siloed operations. Disconnected systems for production, procurement, and logistics create bottlenecks, limiting visibility and coordination. Integrating PlanetTogether with systems like SAP or Oracle breaks down these silos, enabling a unified view of operations.
For example:
SAP Integration: PlanetTogether syncs with SAP's ERP modules to align production schedules with inventory levels and procurement plans. This ensures raw materials are available when needed, reducing downtime and excess inventory costs.
Oracle Integration: By combining Oracle’s cloud capabilities with PlanetTogether’s scheduling tools, Operations Directors can dynamically adjust production schedules based on real-time market demands or supply chain disruptions.
Enhancing Decision-Making with Data Analytics
Incorporating advanced analytics into the value chain transforms data into actionable insights. Integrating PlanetTogether with platforms like Microsoft Dynamics or Kinaxis enables real-time monitoring and predictive analytics, allowing for better forecasting and risk mitigation.
For instance:
Microsoft Dynamics integration can provide a seamless flow of data between the shop floor and the executive level, enabling faster decision-making when disruptions occur.
Kinaxis integration offers supply chain modeling and scenario planning, ensuring resilience in a volatile market.
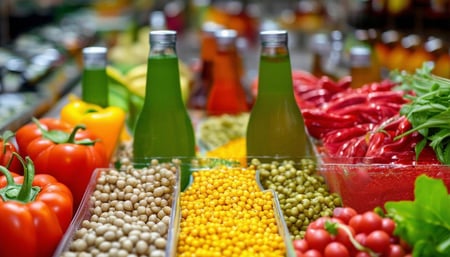
Addressing Key Challenges in Food and Beverage Value Chains
Demand Volatility
Consumer preferences can shift overnight due to trends, seasonal changes, or unexpected events. Advanced integrations between PlanetTogether and SAP or Kinaxis can help forecast demand with greater accuracy, enabling manufacturers to adjust production schedules proactively.
Scenario: A spike in demand for plant-based beverages requires immediate capacity adjustments. Integration ensures visibility across supply chain nodes, facilitating rapid responses.
Sustainability Goals
Consumers and regulators are increasingly prioritizing sustainability. Operations Directors must align production with eco-friendly practices, reduce waste, and source ethically. PlanetTogether’s optimization algorithms, combined with Aveva’s sustainability analytics, can pinpoint inefficiencies and suggest greener alternatives.
Scenario: By analyzing energy consumption patterns, Aveva integration identifies opportunities to reduce carbon emissions while maintaining throughput.
Compliance and Traceability
Regulatory compliance is a critical concern in food and beverage manufacturing. Traceability across the value chain is essential for ensuring food safety and meeting regulatory standards. Integrating PlanetTogether with ERP systems like Oracle enhances traceability by maintaining accurate, real-time records of raw material sourcing, production, and distribution.
Scenario: In the event of a product recall, integration ensures rapid identification and removal of affected batches, minimizing reputational and financial damage.
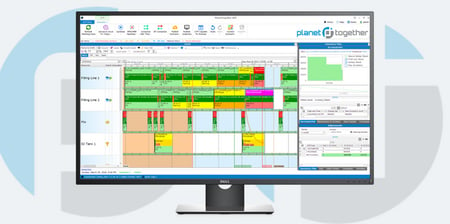
Benefits of Integrating PlanetTogether with ERP Systems
End-to-End Visibility
By integrating PlanetTogether with platforms like SAP or Microsoft Dynamics, Operations Directors gain a holistic view of the entire value chain. This transparency allows for better coordination between departments and faster resolution of issues.
Improved Resource Utilization
PlanetTogether’s scheduling capabilities optimize resource allocation, minimizing downtime and waste. For example, by syncing with SAP’s inventory management tools, manufacturers can ensure that raw materials are utilized efficiently.
Agility and Scalability
Integrations with systems like Kinaxis enable dynamic adjustments to production schedules in response to market fluctuations. This agility ensures that manufacturers can scale operations up or down without sacrificing efficiency.
Cost Savings
By reducing waste, improving production efficiency, and minimizing downtime, integrated solutions drive significant cost savings. For instance, Oracle’s financial planning tools, combined with PlanetTogether’s scheduling algorithms, can identify cost-saving opportunities in procurement and production.
As the food and beverage industry continues to evolve, Operations Directors must adopt a forward-thinking approach to the value chain. Technologies like PlanetTogether, coupled with powerful ERP systems, offer a scalable, adaptable framework for addressing emerging challenges. Whether it’s responding to consumer demands, achieving sustainability targets, or navigating regulatory landscapes, integrated solutions provide the tools to thrive.
By understanding and optimizing the value chain, you can transform operations from reactive to proactive—creating a resilient, efficient, and sustainable future for your manufacturing facility.
Are you ready to take your manufacturing operations to the next level? Contact us today to learn more about how PlanetTogether can help you achieve your goals and drive success in your industry.
LEAVE A COMMENT