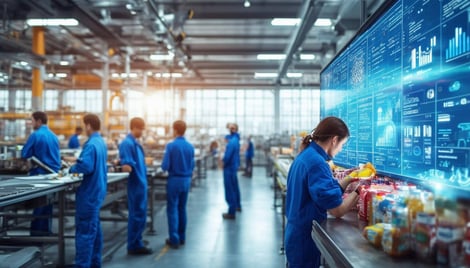
Transitioning from Reactive to Proactive Scheduling in Food and Beverage Manufacturing
Consumer demand is ever-changing, regulatory requirements are strict, and production environments are rife with complexities. Amidst these challenges, scheduling plays a pivotal role in ensuring smooth operations, meeting deadlines, and controlling costs. However, many facilities are stuck in a reactive scheduling paradigm, where problems are addressed only as they arise, leading to inefficiencies and unnecessary stress.
Transitioning to a proactive scheduling approach, supported by cutting-edge tools like PlanetTogether integrated with systems such as SAP, Oracle, Microsoft, Kinaxis, or Aveva, can be transformative.
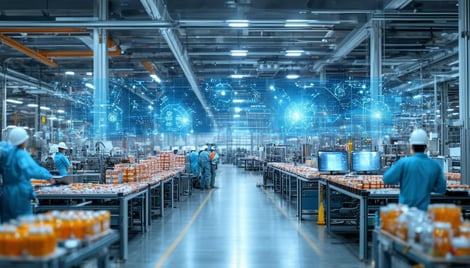
Understanding the Pitfalls of Reactive Scheduling
Reactive scheduling operates in a constant state of "firefighting." Unexpected equipment failures, last-minute order changes, and raw material shortages often result in:
Production Delays: When unforeseen disruptions occur, reactive strategies lead to bottlenecks that delay overall production.
Increased Costs: Overtime labor, expedited shipping, and resource waste are frequent consequences of reactive adjustments.
Poor Resource Utilization: Resources like machinery, materials, and manpower are not optimally aligned, reducing efficiency.
Employee Stress: Constantly adjusting to unanticipated changes creates a stressful work environment and impacts team morale.
The need for a shift toward proactive scheduling is clear. But what does this transition look like, and how can technology facilitate it?

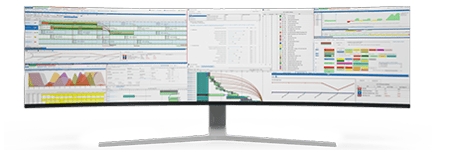
Proactive Scheduling: A Paradigm Shift
Proactive scheduling focuses on anticipating issues before they occur and implementing strategies to prevent them. This involves advanced planning, scenario analysis, and real-time visibility into operations. The core benefits of proactive scheduling include:
Enhanced Predictability: Anticipating potential issues reduces uncertainty and helps stabilize production schedules.
Optimized Resource Allocation: Better planning ensures efficient utilization of machinery, labor, and materials.
Improved Responsiveness: When disruptions occur, a proactive system allows for swift, informed decision-making to minimize impact.
Cost Savings: Avoiding unplanned downtime and reducing overtime lead to significant cost reductions.
Transitioning to proactive scheduling requires the right mindset and the right tools. This is where the integration of advanced scheduling systems like PlanetTogether with ERP solutions such as SAP, Oracle, Microsoft, Kinaxis, or Aveva becomes essential.
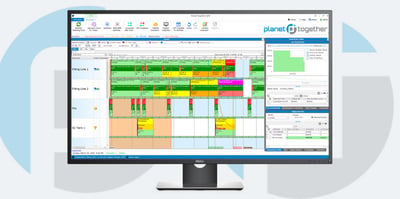
Leveraging Technology for Proactive Scheduling
Real-Time Data Integration: Proactive scheduling relies on real-time data. Integration between PlanetTogether and ERP systems like SAP or Oracle provides a seamless flow of information. For example, inventory levels, production statuses, and order requirements can be updated in real time, enabling accurate planning and rapid adjustments.
Predictive Analytics: PlanetTogether's advanced algorithms, when paired with data from ERP systems, can predict potential bottlenecks or resource constraints. By analyzing historical data and current trends, these tools help Operations Directors anticipate issues before they escalate.
Scenario Planning: One of the standout features of proactive scheduling tools is the ability to simulate "what-if" scenarios. For instance, if a critical piece of equipment is scheduled for maintenance, the system can model how this will impact production and suggest adjustments. Integration with platforms like Microsoft Dynamics or Kinaxis enhances these capabilities by incorporating supply chain data into the simulations.
Enhanced Collaboration: Collaboration across departments is crucial for proactive scheduling. Integrated systems ensure that production, procurement, and logistics teams are aligned. Tools like Aveva’s connected systems facilitate this by offering a unified platform for communication and decision-making.
Automated Adjustments: Proactive scheduling doesn’t mean disruptions won’t occur; it means the system is prepared to handle them. Integrated solutions can automatically adjust schedules in response to changes, such as a delay in raw material delivery. This reduces downtime and keeps production on track.
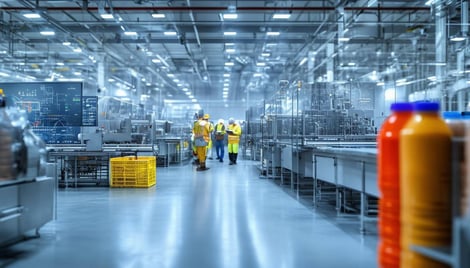
Implementation: Best Practices for a Smooth Transition
Transitioning from reactive to proactive scheduling is a journey that requires careful planning and execution. Here are some best practices:
Assess Current Processes: Conduct a thorough audit of your current scheduling practices. Identify pain points, inefficiencies, and areas where technology can make a difference.
Invest in Training: Your team needs to understand the capabilities of tools like PlanetTogether and how they integrate with existing systems. Offer comprehensive training to ensure smooth adoption.
Start Small: Begin with a pilot project to test the new scheduling approach. Choose a specific production line or process to implement proactive scheduling and measure the results.
Leverage Integration: Maximize the benefits of integration by ensuring that PlanetTogether communicates seamlessly with your ERP system. This may require collaboration with IT teams or external consultants.
Monitor and Iterate: Proactive scheduling is not a one-and-done implementation. Continuously monitor performance, gather feedback, and refine your processes to achieve optimal results.
In food and beverage industry, staying competitive requires more than just reacting to challenges—it demands anticipating and preventing them. Proactive scheduling, supported by robust tools like PlanetTogether integrated with leading ERP systems, is not just a strategy; it’s a necessity.
For Operations Directors, the benefits are clear: improved efficiency, cost savings, and a more resilient production process. By embracing proactive scheduling, you can ensure your facility is not just keeping up with the competition but setting the standard for operational excellence.
Are you ready to take your manufacturing operations to the next level? Contact us today to learn more about how PlanetTogether can help you achieve your goals and drive success in your industry.