Transforming Operational Procurement in Packaging and Containers Manufacturing
In packaging and containers manufacturing, operational procurement plays a critical role in ensuring seamless production, cost efficiency, and supply chain resilience. However, traditional procurement methods often struggle to keep up with the increasing complexity of global supply chains, fluctuating raw material prices, and evolving regulatory requirements. To stay competitive, Purchasing Managers must leverage advanced technologies to optimize procurement strategies, streamline workflows, and enhance supplier collaboration.
One of the most impactful ways to transform operational procurement is through the integration of PlanetTogether Advanced Planning and Scheduling (APS) with enterprise resource planning (ERP) systems like SAP, Oracle, Microsoft, Kinaxis, or Aveva. By bridging the gap between procurement, production planning, and inventory management, this integration enables real-time decision-making, minimizes material shortages, and enhances overall efficiency.
The Challenges of Operational Procurement in Packaging Manufacturing
Purchasing Managers in packaging and containers manufacturing face several challenges that hinder operational efficiency and cost-effectiveness, including:
Supply Chain Volatility
The packaging industry relies on a wide range of materials, such as plastics, paperboard, metals, and adhesives. Market fluctuations, geopolitical instability, and disruptions in transportation can lead to delays, cost spikes, and material shortages.
Production Uncertainty
Without real-time visibility into production schedules, purchasing teams struggle to align procurement with actual production needs. Overordering can lead to excess inventory and increased holding costs, while underordering can halt production lines, leading to missed deadlines.
Complex Supplier Networks
Many packaging manufacturers work with multiple suppliers across different regions. Managing supplier performance, lead times, and compliance requirements manually is time-consuming and prone to errors.
Siloed Data Systems
In many manufacturing environments, procurement operates separately from production planning and inventory management. Disconnected systems make it difficult to coordinate purchasing decisions with real-time shop floor requirements.
The Role of PlanetTogether APS in Procurement Transformation
PlanetTogether APS is an advanced production scheduling tool that optimizes manufacturing operations by balancing demand, capacity, and resource constraints. When integrated with ERP systems like SAP, Oracle, Microsoft, Kinaxis, or Aveva, PlanetTogether APS provides a data-driven approach to procurement, enabling Purchasing Managers to:
Gain Real-Time Visibility into Material Requirements
Through real-time production scheduling, PlanetTogether APS provides precise material requirements based on actual and forecasted demand. This eliminates the guesswork in procurement and ensures that materials are ordered only when needed, reducing waste and excess inventory.
Enhance Supplier Collaboration
By leveraging automated data sharing between PlanetTogether APS and ERP systems, suppliers receive accurate demand forecasts and lead time expectations. This helps streamline procurement negotiations, improve supplier performance, and minimize supply disruptions.
Optimize Just-in-Time (JIT) Procurement
With real-time data integration, Purchasing Managers can implement a Just-in-Time (JIT) strategy to minimize storage costs and prevent material obsolescence. PlanetTogether APS aligns purchasing schedules with production timelines, ensuring materials arrive exactly when needed.
Improve Cost Efficiency and Budget Control
By integrating PlanetTogether APS with SAP, Oracle, Microsoft, Kinaxis, or Aveva, procurement teams gain better control over material costs. Automated alerts notify managers of price fluctuations, alternative suppliers, and bulk purchase opportunities, enabling smarter cost-saving decisions.
Automate Procurement Workflows
The integration eliminates manual purchase order processing by generating automated procurement requests based on real-time demand signals. This reduces administrative burdens, minimizes human errors, and speeds up the approval process.
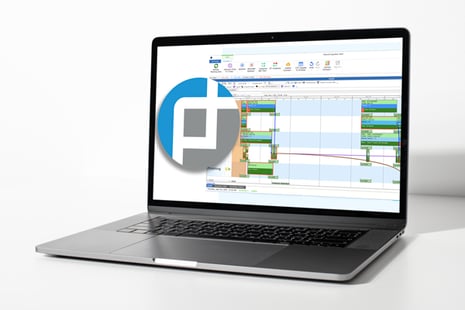
Key Benefits of PlanetTogether APS and ERP Integration
When PlanetTogether APS is fully integrated with ERP systems, Purchasing Managers in packaging and containers manufacturing can expect:
Reduced Procurement Lead Times
Real-time synchronization between scheduling and procurement ensures faster material availability, reducing production downtime and enhancing delivery reliability.
Higher Supplier Reliability
With better demand forecasts and automated communication, suppliers can plan their deliveries more accurately, reducing stockouts and backorders.
Lower Inventory Costs
JIT procurement and optimized order planning prevent overstocking and understocking, leading to reduced inventory carrying costs and improved cash flow.
Enhanced Data-Driven Decision Making
Integration provides Purchasing Managers with real-time analytics, KPI dashboards, and predictive insights that help optimize procurement strategies and mitigate risks.
Increased Operational Efficiency
With automated workflows and synchronized data, procurement teams spend less time on administrative tasks and more time on strategic initiatives such as supplier relationship management and cost negotiations.
Transforming operational procurement in packaging and containers manufacturing requires a strategic approach to data integration, supplier collaboration, and process automation. By integrating PlanetTogether APS with ERP systems like SAP, Oracle, Microsoft, Kinaxis, or Aveva, Purchasing Managers gain real-time insights, optimize material planning, and enhance overall efficiency.
With a proactive, technology-driven approach, procurement teams can overcome supply chain disruptions, reduce costs, and ensure seamless production flow. Investing in advanced planning and scheduling tools is no longer optional—it is a must for packaging manufacturers striving to achieve operational excellence in an increasingly competitive market.
Are you ready to take your manufacturing operations to the next level? Contact us today to learn more about how PlanetTogether can help you achieve your goals and drive success in your industry.
Topics: PlanetTogether Software, Integrating PlanetTogether, Packaging and Containers Manufacturing
LEAVE A COMMENT