RL Revolution in Synchronized Production
Operations Directors are constantly seeking ways to optimize production processes, reduce costs, and improve overall efficiency. In this digital era, the integration of advanced technologies like Reinforcement Learning (RL) with Enterprise Resource Planning (ERP), Supply Chain Management (SCM), and Manufacturing Execution Systems (MES) can revolutionize synchronized production, providing a competitive edge to manufacturers.
This blog explores the potential of RL and its integration with systems like PlanetTogether, SAP, Oracle, Microsoft, Kinaxis, Aveva, and others to transform the Food and Beverage manufacturing sector.
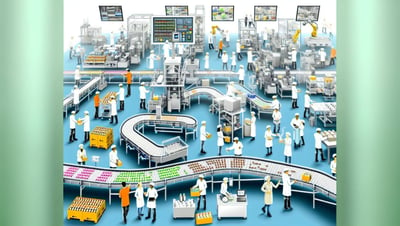
Synchronized Production
Synchronized production, in the context of the Food and Beverage industry, refers to the ability to efficiently coordinate all aspects of production, from raw material procurement to final product delivery, in real-time. Achieving synchronization in an environment with fluctuating demand, perishable ingredients, and complex production processes can be incredibly challenging.
Traditionally, manufacturers have relied on rule-based algorithms and manual decision-making processes to maintain synchronization. However, these approaches often fall short in adapting to dynamic changes in the production environment. This is where Reinforcement Learning enters the picture.
Reinforcement Learning
Reinforcement Learning is a subset of artificial intelligence that focuses on training algorithms to make sequential decisions through trial and error. It closely mimics human learning by rewarding actions that lead to desired outcomes and penalizing those that don't. In the context of synchronized production, RL can optimize production processes by continuously learning and adapting to changing conditions.
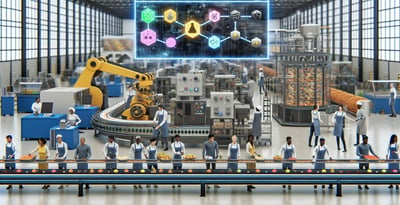
The Integration of RL with ERP, SCM, and MES Systems
To harness the full potential of RL in synchronized production, it's crucial to integrate it seamlessly with existing systems like ERP, SCM, and MES. Let's explore how this integration can create a powerful synergy:
Data Integration: RL algorithms require access to real-time data to make informed decisions. Integrating systems like PlanetTogether, SAP, Oracle, Microsoft, Kinaxis, Aveva, and others allows RL algorithms to access data related to demand forecasting, inventory levels, production schedules, and more. This data forms the basis for RL-driven decision-making.
Optimized Production Scheduling: One of the most significant benefits of integrating RL with production systems is the ability to optimize production schedules dynamically. RL algorithms can continually adjust production plans based on real-time data, ensuring that production resources are allocated efficiently.
Demand Forecasting and Inventory Management: Integrating RL with ERP and SCM systems enables more accurate demand forecasting and inventory management. RL algorithms can adapt to sudden changes in demand and recommend inventory levels that minimize waste while meeting customer demands.
Quality Control: In the Food and Beverage industry, maintaining product quality is paramount. RL algorithms can be trained to monitor production processes and make real-time adjustments to ensure consistent product quality.
Resource Allocation: RL can optimize the allocation of resources such as labor, equipment, and raw materials. This leads to reduced downtime, lower operating costs, and improved overall efficiency.
Energy Efficiency: For sustainable manufacturing practices, RL can optimize energy consumption by adjusting production schedules to take advantage of lower energy costs during off-peak hours.
The Path to Implementation
Implementing RL for synchronized production is a significant undertaking, but the rewards can be game-changing. Here are the key steps to consider:
Assessment: Begin by assessing your current production processes, data availability, and technology infrastructure. Identify areas where RL integration can yield the most significant benefits.
Data Preparation: Ensure that your data is clean, structured, and readily accessible by RL algorithms. Data integration across ERP, SCM, and MES systems is crucial for success.
Algorithm Development: Partner with experts in RL or work with vendors specializing in RL solutions. Develop and train RL algorithms tailored to your specific production environment.
Integration: Collaborate with your IT team to integrate RL seamlessly with existing systems. Ensure data flows in real-time to support dynamic decision-making.
Testing and Validation: Rigorously test the RL-driven solutions in a controlled environment to fine-tune algorithms and verify their effectiveness.
Deployment: Gradually roll out RL integration into your production processes, starting with pilot programs and scaling up as you gain confidence in the system's performance.
Continuous Improvement: Monitor the performance of RL algorithms and gather feedback from production teams. Continuously adapt and refine the algorithms to maximize their impact.
Challenges and Considerations
While RL integration holds immense promise, there are several challenges and considerations to keep in mind:
Data Security: Integrating systems opens potential security vulnerabilities. Ensure robust data encryption and access controls to protect sensitive information.
Change Management: Introducing RL-driven decision-making may require a cultural shift within your organization. Invest in change management strategies to gain buy-in from employees.
Maintenance and Support: RL algorithms require ongoing maintenance and updates. Establish a support framework to address issues promptly and keep algorithms up to date.
Initial Investment: The initial cost of RL integration can be substantial. Conduct a cost-benefit analysis to justify the investment and determine the expected return on investment.
Regulatory Compliance: Ensure that RL-driven decisions comply with industry regulations and standards, especially in the Food and Beverage sector, which has strict quality and safety requirements.
Reinforcement Learning represents a powerful opportunity for Food and Beverage manufacturers to achieve synchronized production and gain a competitive edge in a dynamic market. By integrating RL with systems like PlanetTogether, SAP, Oracle, Microsoft, Kinaxis, Aveva, and others, Operations Directors can unlock new levels of efficiency, reduce costs, and enhance product quality.
While challenges exist, the potential benefits make RL integration a compelling strategy for the future of Food and Beverage manufacturing. Embracing RL-driven decision-making can pave the way for a more agile, sustainable, and profitable industry.
LEAVE A COMMENT