Edge Computing for Real-Time Decision-Making in Scheduling
As an Operations Director, you understand the critical role scheduling plays in optimizing production processes in the food and beverage manufacturing business. However, traditional scheduling methods often fall short in providing real-time insights and adaptability needed to meet the demands of modern consumers. This is where edge computing steps in to revolutionize scheduling, enabling agile decision-making and driving operational excellence.
In this blog, we will look into the significance of edge computing in scheduling for F&B manufacturing facilities. Specifically, we'll explore how the integration between PlanetTogether, a leading scheduling software, and prominent ERP, SCM, and MES systems such as SAP, Oracle, Microsoft, Kinaxis, and Aveva, empowers Operations Directors like you to make informed decisions in real-time, ultimately enhancing productivity and profitability.
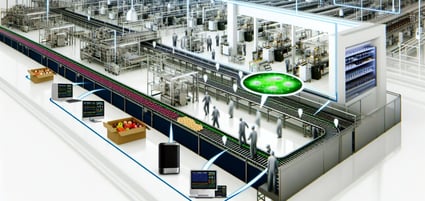
Understanding Edge Computing in Manufacturing
Before we look into the specifics, let's first grasp the concept of edge computing and its relevance in the manufacturing sector. Edge computing involves processing data closer to the source of generation, i.e., at the "edge" of the network, rather than relying solely on centralized data centers. This approach minimizes latency, enhances scalability, and enables faster decision-making by analyzing data in real-time.
In the context of F&B manufacturing, where every minute counts, leveraging edge computing for scheduling offers numerous advantages. By harnessing the power of edge devices deployed across the production floor, manufacturers can access real-time data on machine performance, inventory levels, and production metrics, facilitating proactive decision-making and optimization of production schedules.
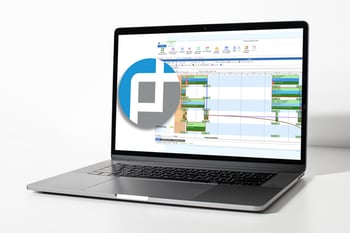
Integration of PlanetTogether with ERP, SCM, and MES Systems
Now, let's discuss the integration between PlanetTogether and leading ERP, SCM, and MES systems, such as SAP, Oracle, Microsoft, Kinaxis, and Aveva. This integration is instrumental in streamlining operations, as it enables seamless data exchange between scheduling software and other critical systems within the manufacturing ecosystem.
SAP Integration: SAP is widely used in the F&B industry for its robust ERP solutions. By integrating PlanetTogether with SAP, Operations Directors gain access to a comprehensive view of production data, inventory levels, and customer orders. This integration facilitates synchronized planning and execution, ensuring optimal resource utilization and on-time delivery.
Oracle Integration: Oracle's SCM solutions play a pivotal role in managing supply chain operations in F&B manufacturing. Integrating PlanetTogether with Oracle enables real-time synchronization of production schedules with procurement, inventory, and logistics functions. This synergy enhances supply chain visibility and agility, enabling prompt response to changing market demands.
Microsoft Integration: Microsoft's suite of business applications, including Dynamics 365, offers powerful tools for managing manufacturing operations. Integration between PlanetTogether and Microsoft ERP systems provides Operations Directors with a unified platform for scheduling, resource allocation, and production tracking. The seamless flow of data between these systems enhances operational efficiency and facilitates continuous improvement initiatives.
Kinaxis Integration: Kinaxis is renowned for its cloud-based SCM and S&OP solutions, which are highly adaptable to dynamic business environments. By integrating PlanetTogether with Kinaxis, Operations Directors can leverage advanced analytics and scenario planning capabilities to optimize production schedules in response to demand fluctuations, supply chain disruptions, or capacity constraints.
Aveva Integration: Aveva's MES solutions are designed to improve manufacturing performance and quality by digitizing production processes. Integration between PlanetTogether and Aveva MES enables real-time monitoring of equipment status, production rates, and quality metrics. This integration empowers Operations Directors to make data-driven decisions to maximize throughput and minimize downtime.
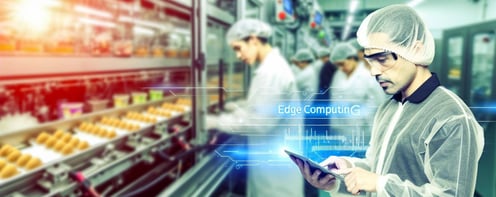
Benefits of Edge Computing for Real-Time Decision-Making
Now that we've discussed the integration between scheduling software and ERP, SCM, and MES systems, let's explore the tangible benefits of edge computing for real-time decision-making in F&B manufacturing:
Enhanced Agility: Edge computing enables Operations Directors to respond swiftly to changing market dynamics, production disruptions, or customer preferences. By accessing real-time data insights, decision-makers can adjust production schedules on-the-fly, ensuring optimal resource utilization and minimizing production downtime.
Improved Efficiency: With edge computing, manufacturers can leverage predictive analytics and machine learning algorithms to anticipate potential bottlenecks or quality issues before they arise. By proactively addressing these challenges, Operations Directors can optimize production processes, reduce waste, and improve overall operational efficiency.
Increased Visibility: Edge devices deployed throughout the production facility provide granular visibility into key performance indicators (KPIs), such as machine uptime, cycle times, and throughput. This real-time visibility enables Operations Directors to identify opportunities for process optimization and continuous improvement, driving long-term competitiveness and profitability.
Empowered Decision-Making: By integrating scheduling software with ERP, SCM, and MES systems, Operations Directors have access to a unified data platform for making informed decisions. Whether it's prioritizing production orders, allocating resources, or adjusting schedules, decision-makers can rely on real-time insights to optimize operations and meet customer expectations.
Edge computing holds immense potential for revolutionizing scheduling in F&B manufacturing facilities. By integrating scheduling software such as PlanetTogether with ERP, SCM, and MES systems, Operations Directors can harness the power of real-time data to drive agility, efficiency, and visibility across the production floor. As consumer demands continue to evolve, embracing edge computing for scheduling is not just a competitive advantage—it's a strategic imperative for staying ahead in the fast-paced world of F&B manufacturing.
As an Operations Director, embracing edge computing for real-time decision-making in scheduling is the key to unlocking operational excellence and driving business success in the dynamic F&B industry.
Are you ready to take your manufacturing operations to the next level? Contact us today to learn more about how PlanetTogether can help you achieve your goals and drive success in your industry.