Total Quality Control and Six Sigma in Industrial Manufacturing: Reducing Production Variations
Maintaining consistent quality while minimizing production variations is an ongoing challenge in industrial manufacturing. For Plant Managers, achieving these goals is essential to meeting customer expectations, staying competitive, and controlling operational costs. Two approaches that have proven to be highly effective in this regard are Total Quality Management (TQM) and the Six Sigma methodology.
Integrating these approaches with advanced production planning systems like PlanetTogether and ERP solutions from SAP, Oracle, Microsoft, Kinaxis, or Aveva offers even greater opportunities to drive down production variations.
In this blog, we will explore how TQM and Six Sigma methods work and how their integration with advanced digital planning solutions can enhance quality control processes, eliminate variations, and lead to higher efficiency and profitability.
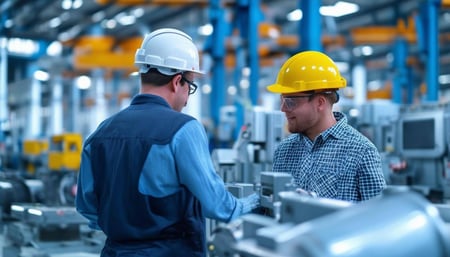
Understanding Total Quality Management (TQM)
Total Quality Management (TQM) is a comprehensive approach to long-term success that emphasizes customer satisfaction through continuous improvement across all levels of an organization. TQM involves all employees in the quest for quality, encouraging them to take ownership of processes and contribute to improvements.
The key principles of TQM include:
Customer Focus: Prioritizing the needs and expectations of both internal and external customers.
Total Employee Involvement: Engaging employees at all levels to foster a culture of quality.
Process-Centered Approach: Focusing on improving processes to reduce defects.
Integrated Systems: Utilizing all components of the organization to contribute to quality goals.
Strategic Approach: Developing a long-term vision and strategic plan for quality improvement.
Data-Driven Decision-Making: Using data and metrics to identify areas for improvement.
Continuous Improvement: Adopting a mindset of ongoing enhancement and refinement of processes.
With TQM as a foundation, plant managers can encourage a unified approach to quality that permeates every layer of the organization.
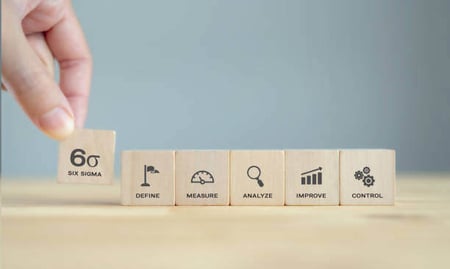
Six Sigma: A Structured Method to Reduce Variability
Six Sigma is a structured, data-driven approach to reducing variation in processes and improving quality. Originating in the manufacturing sector, Six Sigma has grown to be a global standard for quality management, aiming for a defect rate of less than 3.4 defects per million opportunities. The core focus of Six Sigma is the DMAIC methodology, which includes five phases:
Define: Identify the problem or improvement opportunity, along with customer requirements.
Measure: Gather data to understand the current state of the process and identify the baseline.
Analyze: Determine the root causes of variations or defects.
Improve: Implement solutions to address root causes and improve the process.
Control: Establish controls to maintain gains and ensure long-term success.
In practice, Six Sigma methods enable plant managers to identify process inefficiencies, reduce production variations, and achieve higher quality standards.

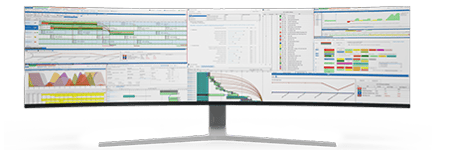
Why Integration Matters: Leveraging PlanetTogether and ERP Systems
While TQM and Six Sigma offer frameworks for quality control, integrating these methodologies with advanced production and planning systems like PlanetTogether alongside ERP systems (e.g., SAP, Oracle, Microsoft, Kinaxis, Aveva) can enhance the ability to minimize variations. Here’s how an integrated approach supports quality and efficiency:
Real-Time Data Collection and Analysis
Using PlanetTogether with an ERP system allows for real-time data collection from across the production floor, from material inputs to final quality checks. This capability is essential for Six Sigma’s Measure and Analyze phases, where accurate data is the foundation for identifying variations. By automatically feeding production data into the Six Sigma process, you can gain insights much faster than with manual methods.
Example: An integration between PlanetTogether and SAP allows automated data capture on production rates, material usage, and quality metrics, reducing the need for manual data entry and enhancing the speed of the Measure phase in Six Sigma.
Centralized Quality Control
Integrated systems centralize quality control data, allowing Plant Managers to monitor performance across the production line. This centralization is crucial in TQM’s Process-Centered Approach, where monitoring process performance in real-time can highlight areas for improvement.
Example: With PlanetTogether integrated into Oracle ERP, quality data from multiple stages of production can be accessed in a single dashboard. This allows immediate corrective action if an increase in defects or variations is detected at any stage.
Automated Alerts and Notifications
PlanetTogether and ERP integrations can include automated alerts for deviations, allowing plant managers to quickly respond to anomalies. These systems can be configured to notify relevant team members when quality falls outside acceptable limits, supporting Six Sigma’s Control phase.
Example: A setup with Microsoft Dynamics and PlanetTogether could trigger alerts if specific process variables exceed predefined Six Sigma control limits, enabling quicker intervention and minimizing the impact of production variations.
Data-Driven Continuous Improvement
Integrating data from PlanetTogether and ERP solutions supports TQM’s Continuous Improvement principle. The data generated across integrated systems helps plant managers continuously refine processes, address root causes of variations, and implement more efficient production methods.
Example: Kinaxis integration with PlanetTogether allows for automated reporting that highlights bottlenecks or variation trends. By identifying recurring quality issues, a plant manager can implement targeted improvements in line with Six Sigma and TQM goals.
Enhanced Predictive Maintenance
Predictive maintenance, powered by data insights from integrated systems, is another benefit for quality control. Equipment malfunctions are a significant source of production variations, and a predictive maintenance approach ensures machines operate within optimal parameters.
Example: Integration between Aveva and PlanetTogether could use machine learning models to forecast equipment failures based on historical data. This proactive approach supports TQM’s commitment to reducing production waste and aligns with Six Sigma’s goal to eliminate process variation caused by equipment inconsistencies.
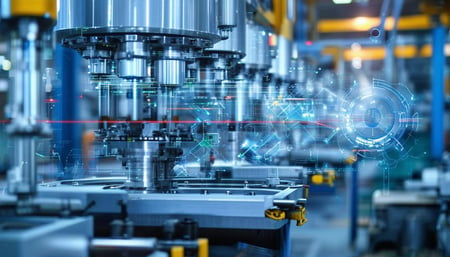
Implementing Integrated Quality Control: A Practical Roadmap
To successfully implement TQM and Six Sigma with an integrated system, plant managers can follow a practical roadmap:
Set Clear Objectives: Define what you want to achieve through TQM and Six Sigma (e.g., reduce defect rates by 10% in the next six months).
Choose Metrics: Identify key metrics that will be monitored, such as yield rates, cycle times, and defect counts.
Integrate Systems: Work with IT to integrate PlanetTogether with your ERP solution (SAP, Oracle, Microsoft, Kinaxis, or Aveva).
Train Employees: Provide training on TQM and Six Sigma principles and show how integrated systems will support their efforts.
Monitor Performance: Use dashboards to track progress in real time, and encourage employees to report issues as they arise.
Drive Continuous Improvement: Regularly review data, adjust processes as needed, and celebrate quality improvements to sustain momentum.
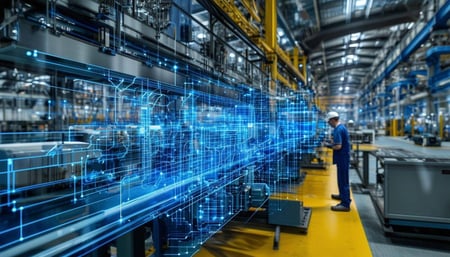
Benefits of Integration for Industrial Manufacturing Facilities
The integration of PlanetTogether and ERP systems amplifies the effectiveness of TQM and Six Sigma in multiple ways:
Enhanced Consistency: Automated data collection and monitoring provide a consistent approach to quality.
Increased Responsiveness: Real-time alerts allow plant managers to address issues immediately, minimizing defects.
Reduced Waste: Predictive maintenance minimizes downtime and ensures machinery operates at optimal levels, reducing waste from defective products.
Improved Employee Engagement: With automated systems handling data tracking, employees can focus on problem-solving and process improvement.
Better Decision-Making: With integrated systems, data-driven insights help managers make informed, proactive decisions, ultimately leading to fewer variations.
For Plant Managers in industrial manufacturing, TQM and Six Sigma offer powerful frameworks for reducing production variations, but integrating these methodologies with advanced systems like PlanetTogether and leading ERP platforms (SAP, Oracle, Microsoft, Kinaxis, or Aveva) can take quality control to the next level. This integration supports real-time monitoring, automated alerts, predictive maintenance, and data-driven decision-making, allowing plant managers to stay agile, proactive, and aligned with quality objectives.
By embracing this integrated approach, your facility can achieve lower defect rates, more consistent product quality, and ultimately, a stronger competitive advantage in today’s demanding industrial landscape. Total Quality Control and Six Sigma, bolstered by modern technology, create a foundation for long-term success in industrial manufacturing.
Are you ready to take your manufacturing operations to the next level? Contact us today to learn more about how PlanetTogether can help you achieve your goals and drive success in your industry.