Timely Decision-Making in Food and Beverage Manufacturing
timely decision-making is critical to maintaining efficient production schedules, minimizing waste, and meeting consumer demand. Production planners often juggle complex scheduling requirements, raw material procurement, compliance demands, and inventory control, all within short timeframes. The need for agility in decision-making is paramount, and technology plays a pivotal role in achieving this. This blog explores how integrating advanced scheduling tools like PlanetTogether with enterprise resource planning (ERP) systems—such as SAP, Oracle, Microsoft, Kinaxis, or Aveva—can streamline processes, enable more responsive planning, and empower production planners to make timely, data-driven decisions.
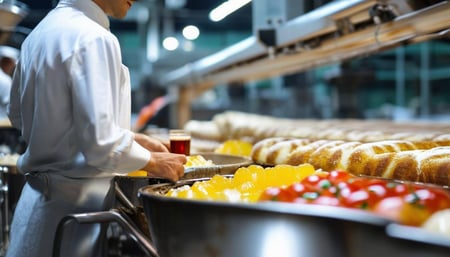
The Challenge of Timely Decision-Making in Food and Beverage Production
Food and beverage manufacturing is uniquely challenging due to perishability, fluctuating demand, regulatory requirements, and an increasing emphasis on sustainability. Production planners face numerous critical decisions, including:
Managing Inventory Levels: Avoiding overstock or stockouts of perishable goods.
Scheduling Production Runs: Aligning production schedules with demand forecasts.
Optimizing Resource Utilization: Ensuring machines, labor, and raw materials are used efficiently.
Reducing Waste and Downtime: Minimizing production stops and optimizing resource allocation.
Responding to Market Changes: Quickly adjusting to seasonal demand fluctuations and shifts in consumer preferences.
Without timely, accurate data, even a small delay in decision-making can disrupt production schedules, result in waste, or impact delivery timelines. Here, the integration of advanced scheduling tools like PlanetTogether with an ERP system offers the agility needed to navigate these challenges.

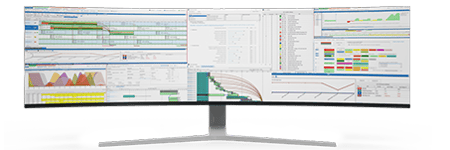
Leveraging PlanetTogether for Advanced Production Scheduling
PlanetTogether is a powerful tool designed to optimize production scheduling and capacity planning. By centralizing data and providing a clear view of available resources, constraints, and demand, it enables production planners to make faster, more informed decisions. Key features of PlanetTogether that support timely decision-making include:
Real-Time Scheduling: Provides instant visibility into production schedules and capacity, allowing planners to make adjustments on the fly.
What-If Scenarios: Allows planners to simulate different scheduling options, helping them to evaluate outcomes and select the best course of action.
Resource Optimization: Automates the scheduling process to maximize the use of equipment, labor, and materials.
Multi-Plant Visibility: Offers visibility across multiple facilities, ideal for larger food and beverage manufacturers with multiple production sites.
However, while PlanetTogether is highly effective on its own, its full potential is realized when integrated with an ERP system.
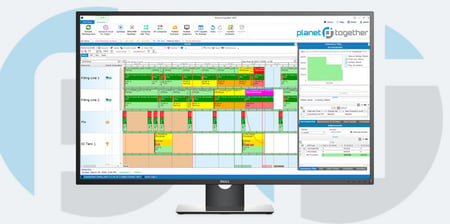
The Power of Integrating PlanetTogether with an ERP System
An ERP system, such as SAP, Oracle, Microsoft, Kinaxis, or Aveva, acts as the backbone of many manufacturing operations by managing data on inventory, procurement, finance, and production. Integrating PlanetTogether with an ERP system provides a holistic view of operations and enables production planners to access real-time data and insights needed for swift, accurate decision-making.
Here's how this integration benefits production planning:
Real-Time Data Synchronization
The integration of PlanetTogether with an ERP system enables real-time data flow between production schedules and other key operational areas, such as inventory, procurement, and sales. When inventory levels change due to a sudden increase in demand, this information is immediately available in PlanetTogether, allowing the production planner to adjust schedules in response. This synchronized data flow eliminates the delays and discrepancies that often arise from using siloed systems, ensuring that decisions are made based on the most current information.
Enhanced Forecast Accuracy
With ERP integration, PlanetTogether can pull demand forecasts and sales orders directly from the ERP, allowing planners to align production schedules more accurately with anticipated demand. In the food and beverage industry, where demand can be influenced by seasonal trends or marketing campaigns, access to accurate forecasting data is essential. Integration with systems like Kinaxis or SAP, which offer advanced forecasting capabilities, further enhances PlanetTogether’s ability to deliver reliable scheduling recommendations.
Improved Inventory Management
Managing inventory is one of the most challenging aspects of food and beverage manufacturing. Overstocks lead to waste, while stockouts can halt production. By integrating PlanetTogether with an ERP system, production planners can get an accurate picture of inventory levels, lead times, and supply chain status. For example, Oracle ERP provides real-time updates on inventory status, which can be seamlessly reflected in PlanetTogether’s scheduling recommendations, helping planners adjust schedules based on material availability. This helps reduce waste, optimize inventory levels, and avoid disruptions.
Efficient Resource Allocation
Production planners in the food and beverage industry must ensure that resources—whether labor, machinery, or materials—are used efficiently to meet production goals. Through ERP integration, PlanetTogether can account for resource availability, scheduled maintenance, and even labor shifts. For example, if Microsoft Dynamics ERP signals that a machine is due for maintenance, PlanetTogether can automatically adjust the production schedule to minimize downtime. This streamlined communication prevents delays, minimizes idle time, and ensures that resources are allocated in the most effective way possible.
Enhanced Compliance and Traceability
Compliance is a critical concern in food and beverage manufacturing, where strict regulations govern production processes and ingredient sourcing. Integration between PlanetTogether and an ERP system provides planners with traceability throughout the supply chain. If a compliance issue arises, the production planner can quickly trace the affected batch and make necessary adjustments in real-time. For example, with Aveva ERP’s compliance tracking capabilities, PlanetTogether can assist in creating compliant schedules, ensuring that production processes meet regulatory standards while maintaining productivity.
Faster Response to Market Changes
The food and beverage industry is dynamic, with consumer preferences and market trends constantly evolving. Integrated systems enable production planners to react swiftly to these changes. If demand for a product surges, the ERP system can relay this information to PlanetTogether, which can then reschedule production runs to meet the increased demand. With systems like Kinaxis, known for its rapid planning and response capabilities, integration with PlanetTogether enables near-instantaneous adjustments to production schedules, providing a significant competitive advantage.
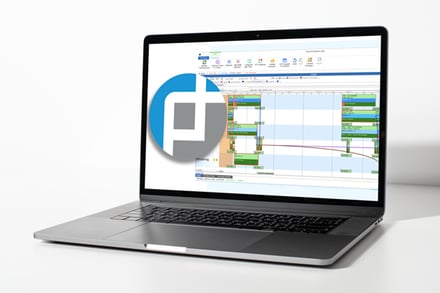
How PlanetTogether and ERP Integration Empowers Production Planners
For production planners, the integration of PlanetTogether with ERP systems means fewer bottlenecks, faster adjustments, and a more agile response to unforeseen challenges. Here’s a closer look at how this integration supports production planners in making timely decisions:
Data-Driven Insights: Planners no longer need to rely on manual data entry or outdated reports. Integrated data provides them with a live dashboard of key metrics, including inventory status, production rates, and demand forecasts.
Predictive Decision-Making: With what-if scenario analysis and predictive capabilities, planners can foresee potential issues and proactively adjust schedules. For instance, they can predict the impact of a machine breakdown on overall productivity and adjust accordingly.
Reduced Administrative Burden: Automation reduces the need for manual data entry, freeing up planners to focus on high-level strategic decisions. By minimizing administrative tasks, planners can spend more time analyzing data and optimizing production processes.
Improved Communication and Collaboration: ERP integration facilitates better communication across departments. Sales, inventory, procurement, and production teams all access the same real-time data, enabling coordinated decision-making. This is especially valuable in large organizations where different departments may work in silos.
For production planners in food and beverage manufacturing, timely decision-making is essential to maintaining efficiency, reducing waste, and meeting customer demands. The integration of PlanetTogether with ERP systems like SAP, Oracle, Microsoft, Kinaxis, or Aveva unlocks new levels of agility, empowering planners with real-time insights, predictive capabilities, and optimized workflows. By embracing this integrated approach, food and beverage manufacturers can overcome the challenges of a dynamic market, streamline production processes, and deliver products to consumers more effectively.
In an industry where every minute counts, the ability to make swift, informed decisions is invaluable. Integrating PlanetTogether with ERP systems provides the foundation for truly agile, responsive production planning, setting the stage for long-term success in the competitive world of food and beverage manufacturing.
Are you ready to take your manufacturing operations to the next level? Contact us today to learn more about how PlanetTogether can help you achieve your goals and drive success in your industry.