Automated Material Handling Systems (AMHS)
Precision, efficiency, and reliability are essential in medical manufacturing. As the industry continues to evolve, manufacturers are constantly seeking innovative solutions to streamline operations and enhance productivity. One such solution that has gained significant traction in recent years is Automated Material Handling Systems (AMHS).
In this blog, we will look into the transformative potential of AMHS in medical manufacturing facilities, exploring its benefits, challenges, and the crucial role of integration with leading ERP, SCM, and MES systems like PlanetTogether, SAP, Oracle, Microsoft, Kinaxis, and Aveva.
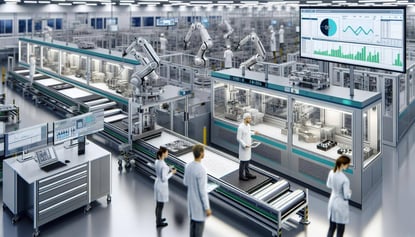
Automated Material Handling Systems
Automated Material Handling Systems (AMHS) encompass a wide range of technologies and processes designed to automate the movement, storage, and retrieval of materials within a manufacturing facility. From raw materials to finished products, AMHS efficiently manage the flow of materials throughout the production process, minimizing manual intervention and optimizing throughput.
Key Components of AMHS
Conveyor Systems: Conveyor belts, roller conveyors, and automated guided vehicles (AGVs) are commonly used to transport materials between various manufacturing stages, eliminating the need for manual handling.
Automated Storage and Retrieval Systems (AS/RS): AS/RS utilize robotic arms and automated storage units to store and retrieve materials from designated storage locations, maximizing storage density and retrieval speed.
Robotics and Automation: Robotic arms and automation technologies play a crucial role in material handling tasks such as palletizing, sorting, and packaging, enhancing efficiency and precision.
Warehouse Management Systems (WMS): WMS software integrates with AMHS to optimize inventory management, order picking, and replenishment processes, ensuring accurate and timely material handling operations.
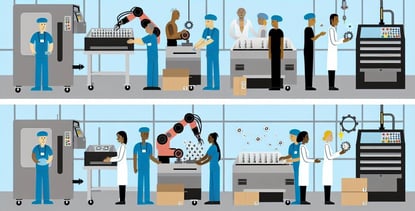
Benefits of Automated Material Handling Systems in Medical Manufacturing
Improved Efficiency: AMHS streamline material flow and reduce lead times, allowing manufacturers to meet tight production schedules and customer demands more effectively.
Enhanced Accuracy: Automation minimizes the risk of human error in material handling tasks, ensuring precise inventory management and order fulfillment.
Increased Safety: By reducing manual handling tasks and minimizing the risk of accidents and injuries, AMHS create a safer working environment for employees.
Scalability and Flexibility: Modular design and scalable solutions enable manufacturers to adapt AMHS to evolving production needs and scale operations as required.
Cost Savings: Automation reduces labor costs, minimizes material waste, and optimizes resource utilization, resulting in significant cost savings over time.
Challenges and Considerations
While the benefits of AMHS are undeniable, implementing and integrating these systems into existing manufacturing environments pose several challenges:
Initial Investment: The upfront cost of deploying AMHS can be substantial, requiring careful budgeting and ROI analysis to justify the investment.
Integration Complexity: Integrating AMHS with existing ERP, SCM, and MES systems is essential for seamless data exchange and process optimization. However, achieving integration can be complex, requiring collaboration between IT and manufacturing teams.
Maintenance and Support: AMHS require regular maintenance and support to ensure optimal performance and reliability. Manufacturers must have robust maintenance protocols in place to address potential issues promptly.
Employee Training and Adoption: Transitioning to an automated manufacturing environment requires comprehensive training and change management initiatives to upskill employees and ensure smooth adoption of new technologies.

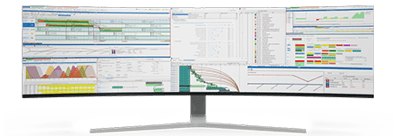
Integration with Leading ERP, SCM, and MES Systems
Integration between AMHS and leading ERP, SCM, and MES systems such as PlanetTogether, SAP, Oracle, Microsoft, Kinaxis, and Aveva is critical for realizing the full potential of automation in medical manufacturing facilities.
Real-Time Data Visibility: Integration enables seamless data exchange between AMHS and ERP systems, providing real-time visibility into inventory levels, production schedules, and order status.
Demand Forecasting and Planning: By integrating with SCM and MES systems, AMHS can leverage demand forecasting data to optimize material flow, production scheduling, and inventory management processes.
Process Optimization: Integration allows for continuous process improvement by analyzing performance data from AMHS and ERP systems, identifying bottlenecks, and implementing corrective actions to enhance efficiency and productivity.
Compliance and Traceability: Integrated systems facilitate compliance with regulatory requirements by providing accurate documentation and traceability throughout the manufacturing process, ensuring product quality and safety.
Automated Material Handling Systems (AMHS) represent a game-changer for medical manufacturing facilities, offering a myriad of benefits ranging from improved efficiency and accuracy to enhanced safety and cost savings. However, successful implementation and integration require careful planning, investment, and collaboration between manufacturing and IT teams.
By integrating AMHS with leading ERP, SCM, and MES systems like PlanetTogether, SAP, Oracle, Microsoft, Kinaxis, and Aveva, manufacturers can unlock the full potential of automation, driving innovation, and competitiveness in the dynamic landscape of medical manufacturing.
Are you ready to take your manufacturing operations to the next level? Contact us today to learn more about how PlanetTogether can help you achieve your goals and drive success in your industry.
LEAVE A COMMENT