Design Algorithms in Optimized Product Design and Material Usage
As an Operations Director in this industry, you understand the critical role optimization plays in ensuring the quality, cost-effectiveness, and timely delivery of medical products. Today, we're looking into a groundbreaking technology that holds the potential to transform your operations: generative design algorithms.
In this blog, we'll explore how generative design algorithms are revolutionizing product design and material usage in medical manufacturing. Furthermore, we'll discuss the integration between PlanetTogether—a leading production planning and scheduling software—and key Enterprise Resource Planning (ERP), Supply Chain Management (SCM), and Manufacturing Execution Systems (MES) such as SAP, Oracle, Microsoft, Kinaxis, Aveva, and others, to maximize the benefits of generative design.
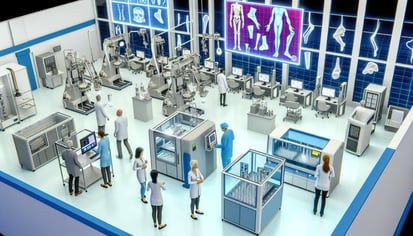
Generative Design
Generative design is not a new concept, but recent advancements in computational power and artificial intelligence have propelled it into the spotlight. At its core, generative design involves using algorithms to explore a vast range of design options, considering various parameters and constraints, to arrive at optimal solutions.
Unlike traditional design approaches, where human designers iterate through limited options, generative design algorithms generate numerous possibilities based on defined parameters such as material properties, manufacturing constraints, performance criteria, and cost considerations. This iterative process leads to designs that are often innovative, efficient, and highly optimized for their intended purpose.
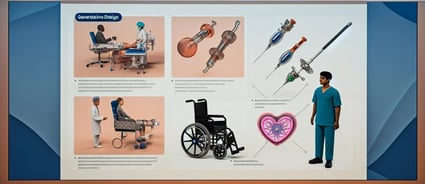
Benefits of Generative Design in Medical Manufacturing
Enhanced Product Performance: Generative design algorithms excel at exploring unconventional design solutions that maximize product performance. In medical manufacturing, this translates to devices and equipment that are lighter, stronger, and more ergonomic, leading to improved patient outcomes and user satisfaction.
Material Efficiency: By analyzing material properties and structural requirements, generative design algorithms can minimize material usage while maintaining structural integrity. This not only reduces material costs but also contributes to sustainability efforts by minimizing waste.
Accelerated Innovation: Traditional design processes can be time-consuming, often limiting the exploration of innovative concepts. Generative design algorithms rapidly generate and evaluate numerous design iterations, accelerating the innovation cycle and enabling manufacturers to stay ahead of market demands.
Cost Reduction: Optimized designs result in reduced material usage, lower manufacturing costs, and improved operational efficiency. Additionally, by streamlining the design process and minimizing the need for physical prototypes, generative design helps to lower development costs and speed up time-to-market.
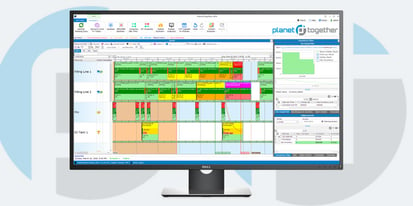
Integration with PlanetTogether and ERP/SCM/MES Systems
To fully harness the potential of generative design algorithms, seamless integration with production planning, scheduling, and enterprise systems is essential. PlanetTogether, a leading production planning and scheduling software, offers robust integration capabilities with various ERP, SCM, and MES systems including SAP, Oracle, Microsoft, Kinaxis, Aveva, and others.
By integrating generative design outputs with these systems, manufacturers can achieve a synchronized workflow that optimizes both design and production processes.
Here's how integration between PlanetTogether and ERP/SCM/MES systems enhances the application of generative design in medical manufacturing:
Unified Data Management: Integration ensures that design data, production schedules, inventory levels, and resource availability are synchronized across the organization. This unified data environment provides designers and planners with real-time insights to make informed decisions.
Seamless Workflow Automation: Generative design outputs seamlessly flow into production planning and scheduling processes within PlanetTogether. This automation eliminates manual data transfer, reduces errors, and accelerates the transition from design to manufacturing.
Dynamic Resource Allocation: With integrated ERP/SCM/MES systems, PlanetTogether can dynamically allocate resources based on design specifications, production requirements, and supply chain constraints. This agility optimizes resource utilization and minimizes bottlenecks throughout the manufacturing process.
Continuous Optimization: By leveraging real-time data exchange between systems, manufacturers can continuously optimize production schedules and adapt to changing demand patterns, market conditions, and design iterations. This agility enables agile manufacturing practices that enhance competitiveness and customer responsiveness.
Generative design algorithms represent a paradigm shift in the way medical products are designed and manufactured. By leveraging advanced computational techniques, manufacturers can achieve unparalleled levels of efficiency, innovation, and sustainability.
As an Operations Director in a medical manufacturing facility, integrating generative design with leading production planning and ERP/SCM/MES systems such as PlanetTogether, SAP, Oracle, Microsoft, Kinaxis, Aveva, and others is key to unlocking the full potential of this transformative technology.
By embracing generative design and fostering seamless integration across the entire product lifecycle, you can drive operational excellence, accelerate innovation, and deliver superior medical products that positively impact patient lives.
Are you ready to take your manufacturing operations to the next level? Contact us today to learn more about how PlanetTogether can help you achieve your goals and drive success in your industry.
LEAVE A COMMENT