AI-Driven Scheduling Assistants for Demand-Driven Planning
With consumers demanding more personalized products, faster delivery times, and sustainable practices, the pressure on Operations Directors is higher than ever. In this dynamic environment, embracing cutting-edge technologies like Artificial Intelligence (AI) is crucial for achieving efficiency, agility, and competitiveness.
One area where AI is making a significant impact is in demand-driven planning, particularly through AI-driven scheduling assistants. These assistants, powered by advanced algorithms and machine learning, are revolutionizing how production schedules are created, optimized, and executed.
In this blog, we look into the transformative potential of AI-driven scheduling assistants, exploring their integration with leading Enterprise Resource Planning (ERP), Supply Chain Management (SCM), and Manufacturing Execution Systems (MES) like SAP, Oracle, Microsoft, Kinaxis, Aveva, and more.
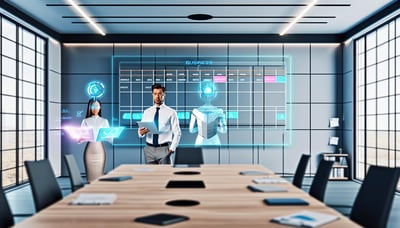
Understanding Demand-Driven Planning
Before we look into the specifics of AI-driven scheduling assistants, let's establish a foundational understanding of demand-driven planning. Traditionally, manufacturing schedules were based on forecasts or fixed time intervals, often resulting in inefficiencies, overproduction, or stockouts. Demand-driven planning, on the other hand, revolves around real-time demand signals, allowing for more agile, responsive, and customer-centric operations.
At the heart of demand-driven planning is the ability to synchronize production activities with fluctuating demand, minimizing waste and maximizing resource utilization. This requires not only accurate demand forecasting but also dynamic scheduling that can adapt to changing priorities, constraints, and market conditions in real-time.
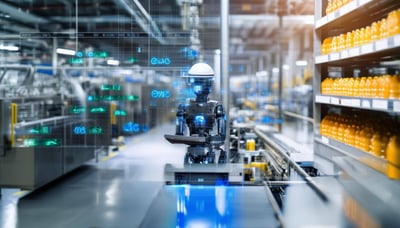
The Role of AI in Scheduling
AI-driven scheduling assistants leverage the power of artificial intelligence to optimize production schedules based on a multitude of factors, including demand forecasts, inventory levels, capacity constraints, lead times, and resource availability. These assistants analyze vast amounts of data, identify patterns, and generate schedules that are not only feasible but also highly efficient.
The key capabilities of AI-driven scheduling assistants include:
Real-Time Optimization: Unlike traditional scheduling methods that rely on static plans, AI-driven assistants continuously analyze incoming data and adjust schedules accordingly. This real-time optimization ensures that production remains aligned with demand, minimizing the risk of overproduction or stockouts.
Scenario Analysis: AI-driven assistants can simulate various scenarios to assess the impact of different factors on production schedules. This capability allows Operations Directors to make informed decisions, such as prioritizing certain orders, adjusting production capacities, or accommodating unexpected disruptions.
Constraint Management: Scheduling in manufacturing is often constrained by factors such as machine availability, labor constraints, and regulatory requirements. AI-driven assistants can intelligently manage these constraints, finding the optimal balance between conflicting priorities while ensuring compliance with regulations and standards.
Integration with ERP, SCM, and MES Systems: One of the most significant advantages of AI-driven scheduling assistants is their seamless integration with existing systems such as SAP, Oracle, Microsoft, Kinaxis, Aveva, and others. By leveraging data from these systems, AI assistants can provide a holistic view of the manufacturing operations, enabling end-to-end optimization.
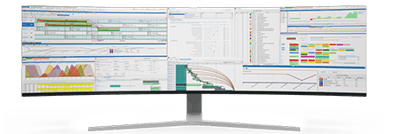
Integration of PlanetTogether with ERP, SCM, and MES systems
Among the leading solutions in AI-driven scheduling assistants is PlanetTogether. PlanetTogether offers a comprehensive suite of tools for production planning and scheduling, powered by advanced algorithms and optimization techniques. What sets PlanetTogether apart is its ability to integrate seamlessly with a wide range of ERP, SCM, and MES systems, including the ones mentioned earlier.
The integration between PlanetTogether and these systems enables:
Data Synchronization: Real-time exchange of data between PlanetTogether and ERP, SCM, and MES systems ensures that scheduling decisions are based on the latest information, such as inventory levels, production orders, and resource availability.
Unified Visibility: By consolidating data from multiple sources, the integration provides Operations Directors with a unified view of the entire manufacturing process, from raw materials procurement to finished goods delivery.
Streamlined Workflows: Integration eliminates manual data entry and reconciliation, streamlining workflows and reducing the risk of errors. This allows teams to focus on value-added activities rather than administrative tasks.
Enhanced Decision-Making: With access to accurate, up-to-date information, Operations Directors can make data-driven decisions that drive operational excellence, improve efficiency, and increase customer satisfaction.
AI-driven scheduling assistants are transforming demand-driven planning in Food and Beverage manufacturing, enabling Operations Directors to achieve unprecedented levels of efficiency, agility, and customer satisfaction. Through seamless integration of PlanetTogether with leading ERP, SCM, and MES systems like SAP, Oracle, Microsoft, Kinaxis, Aveva, and others, these assistants are streamlining workflows, optimizing production schedules, and driving operational excellence.
As we look to the future, the role of AI in manufacturing will only continue to grow, offering new opportunities for innovation and competitive advantage. By embracing AI-driven scheduling assistants and harnessing the power of integration, Operations Directors can position their organizations for success in the digital age of manufacturing.
Are you ready to take your manufacturing operations to the next level? Contact us today to learn more about how PlanetTogether can help you achieve your goals and drive success in your industry.
LEAVE A COMMENT