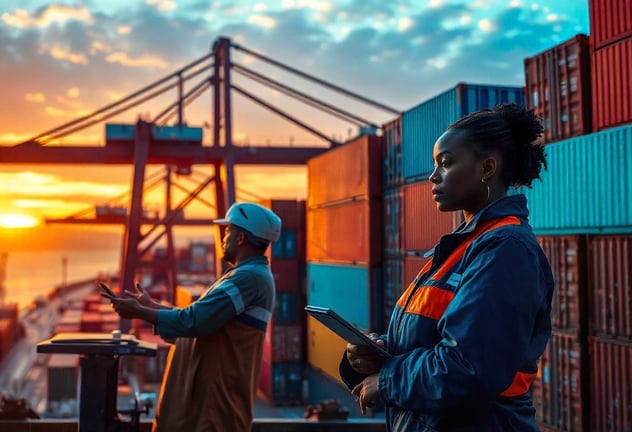
What is Supply Chain Management?
Supply chain management (SCM) refers to the management of operations that are involved in the procurement of raw materials, their transformation into finished goods, and their distribution to the end consumer.
The simplest supply chain includes your suppliers, you, and your customers. However, most manufacturing organizations have a more complex supply chain that includes multiple suppliers and even outsourcing operations.
Any company will benefit from proper supply chain management as it strives to streamline the processes found at each step of the supply chain to ensure that consumers are receiving the right amount of the right item at the right time. When you are able to deliver on your promises, you are more likely to secure future business with your customers and maintain a competitive advantage in the market.
Good supply chain management ensures that you maintain a balance between demand and supply. In order to reduce waste, increase profits, reduce costs, and ensure the timely delivery of products, supply chain management must be efficient. This is why understanding the five functions of supply chain management is essential for manufacturing organizations as it will provide insight into how to improve the efficiency of your operations. Therefore, here are the five functions of supply chain management.
.png?width=632&height=234&name=Supply%20Chain%20Management%20(1).png)
Five Functions of Supply Chain Management
The five functions of supply chain management include the following:
1. Purchasing
The first function of supply chain management is purchasing. In the manufacturing process, raw materials are required to produce goods and products. It is important that these materials are procured and delivered on time so that production can begin. For this to occur, coordination with suppliers and delivery companies will be required to avoid any potential delays.
2. Operations
Demand planning and forecasting are usually required before materials can be procured, as the demand market will dictate how many units to be produced and how much material is required for production. This function is important in supply chain management as organizations must accurately forecast demand to avoid having too much or too little inventory that will lead to losses in revenue. Therefore, demand planning and forecasting must be tied in with inventory management, production, and shipping to avoid such mistakes.
3. Logistics
Logistics is the part of supply chain management that coordinates all aspects of planning, purchasing, production, warehousing, and transportation so that the products will reach the end-consumer without any hindrances. It is helpful to have adequate communication between multiple departments so that products can be shipped to customers quickly and at the lowest cost.
4. Resource Management
Production consumes raw materials, technology, time, and labor. Resource management ensures that the right resources are allocated to the right activities in an optimized manner. This will ensure that an optimized production schedule is created to maximize the efficiency of the operations. When calculating the available capacity, you should consider the capabilities of each resource and determine whether they can perform the work that is scheduled on it. This will ensure that you are not over-promising orders and that your production schedule is feasible and accurate.
5. Information Workflow
Information sharing and distribution is what keeps all of the other functions of supply chain management on track. If the information workflow and communication are poor, it could break apart the entire chain. Many disruptions that arise in supply chains can be prevented by increased visibility and communication. Having a consistent system that is used by all departments will ensure that everyone is working with the same set of data and will prevent miscommunications and time spent updating everyone on new developments.
.png?width=632&height=421&name=Supply%20Chain%20Management%20(2).png)
It is important for any manufacturing organization to understand the five functions of supply chain management. However, many manufacturers around the globe have trouble keeping up with the rapidly changing demands and challenges involved in supply chain management.
An Advanced Planning and Scheduling (APS) Software can help coordinate these five functions by providing thorough insights into your manufacturing operations.
With PlanetTogether APS, you are able to concurrently plan and schedule your production based on actual customer demands. You will be able to ensure that you have all of the required materials and resource capacity available to start production. This will ensure that your supply and demand are aligned so that you can deliver goods to your customers on time.
With PlanetTogether, we're delivering what we said we would, when we said we would. It is an amazingly powerful tool.
Director of Material Systems and IT for the Medical Devices industry
Visual production scheduling will automatically alert you of any material shortages or capacity bottlenecks so that you can fix problems before they occur. The inventory plan will help you keep track of when materials and parts are coming in as well as track increases and decreases in supply for every item.
Manufacturing operations looking to take their company to the next level, improve their production efficiency, and take a hold of their supply chain management should consider implementing an Advanced Planning and Scheduling software.
Advanced Planning and Scheduling (APS) Software
Advanced Planning and Scheduling Softwares have become a must for modern-day manufacturing operations as customer demand for increased product assortment, fast delivery, and downward cost pressures become prevalent. These systems help planners save time while providing greater agility in updating ever-changing priorities, production schedules, and inventory plans. APS Systems can be quickly integrated with an ERP/MRP software to fill the gaps where these systems lack planning and scheduling flexibility, accuracy, and efficiency.
With APS you can:
- Create optimized schedules that balance production efficiency and delivery performance
- Maximize throughput on bottleneck resources to increase revenue
- Synchronize supply with demand to reduce inventories
- Provide company-wide visibility to resource capacity
- Enable scenario data-driven decision making
The implementation of an Advanced Planning and Scheduling (APS) Software will take your manufacturing operations to the next level of production efficiency by taking advantage of the operational data you already possess in your ERP system. APS is a step in the right direction of efficiency and lean manufacturing production enhancement. Try out a free trial or demo!
Take control of your production process with PlanetTogether, a powerful production scheduling software. Reduce costs, eliminate bottlenecks, and achieve peak efficiency.
Related Multi Plant Video
APS Resources