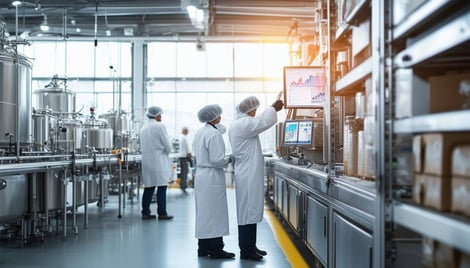
Synchronizing Production with Demand: A Guide for Food and Beverage Production Schedulers
Production schedulers play a pivotal role in aligning production schedules with market demand in the food and beverage sector. The task requires precision, agility, and insight into both operational capabilities and market fluctuations. Misalignment can result in costly overproduction, underutilized resources, or failure to meet customer expectations.
In this blog, we’ll explore strategies to synchronize production with demand, emphasizing how advanced planning tools like PlanetTogether, when integrated with systems such as SAP, Oracle, Microsoft Dynamics, Kinaxis, or Aveva, can revolutionize the scheduling process.
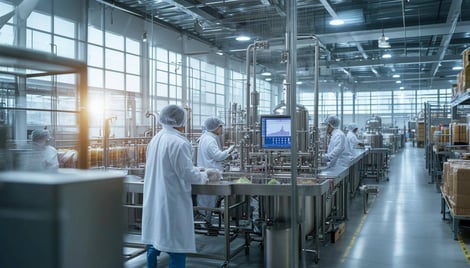
The Challenges of Demand-Synchronized Production
Production schedulers face a unique set of challenges in the food and beverage sector:
- Perishable Inventory: Unlike other manufacturing sectors, food and beverage products often have limited shelf lives, increasing the stakes for precise production planning.
- Demand Variability: Seasonal trends, promotions, and unpredictable consumer preferences require adaptive scheduling strategies.
- Regulatory Compliance: Ensuring production aligns with food safety and labeling standards adds another layer of complexity.
- Resource Constraints: Limited production capacity, raw material availability, and workforce scheduling are constant concerns.
These factors make achieving a demand-driven production model difficult without leveraging advanced technologies.

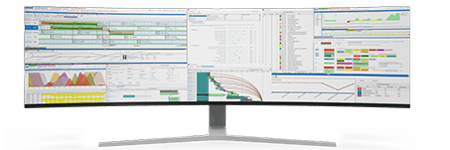
PlanetTogether: The Key to Synchronization
PlanetTogether, an Advanced Planning and Scheduling (APS) system, offers powerful tools to tackle these challenges. By integrating with leading ERP systems like SAP, Oracle, Microsoft Dynamics, Kinaxis, or Aveva, PlanetTogether provides production schedulers with real-time insights, enhanced decision-making capabilities, and a streamlined process to synchronize production with demand.
Here’s how PlanetTogether drives alignment:
- Real-Time Visibility: PlanetTogether’s integration with ERP systems ensures that production schedulers have access to real-time data on raw material inventory, production capacity, and demand forecasts.
- Automated Scheduling: The APS system automates the generation of optimal production schedules, taking into account constraints like equipment availability, workforce schedules, and customer delivery timelines.
- Scenario Analysis: What-if scenarios empower schedulers to evaluate the impact of demand fluctuations or resource changes before making decisions.
- Collaboration: Integration facilitates better communication between supply chain teams, production planners, and other stakeholders, ensuring a unified approach to demand-driven production.
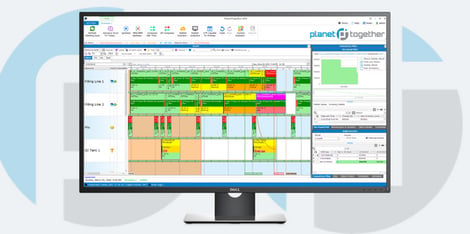
Benefits of Integration with ERP Systems
When integrated with robust ERP systems like SAP, Oracle, Microsoft Dynamics, Kinaxis, or Aveva, PlanetTogether amplifies its capabilities, creating a seamless flow of information across the enterprise.
SAP Integration
With SAP, PlanetTogether taps into precise demand forecasts and historical sales data, enabling schedulers to predict demand spikes and adjust production plans accordingly. This reduces overproduction and waste, which are particularly crucial in the food and beverage industry.
Oracle Integration
Integration with Oracle allows PlanetTogether to leverage advanced analytics for demand sensing and real-time inventory updates. This ensures production schedules are always aligned with the latest market conditions.
Microsoft Dynamics Integration
When paired with Microsoft Dynamics, PlanetTogether enhances supply chain visibility and operational efficiency. The integration simplifies workflows by centralizing data, improving responsiveness to demand changes.
Kinaxis Integration
Kinaxis’ focus on supply chain planning and risk mitigation complements PlanetTogether’s scheduling capabilities. The integration allows production schedulers to address disruptions quickly, ensuring uninterrupted production.
Aveva Integration
Aveva’s expertise in operational efficiency aligns well with PlanetTogether’s scheduling tools. Together, they enable production facilities to optimize energy usage and equipment performance, contributing to cost savings while meeting demand.
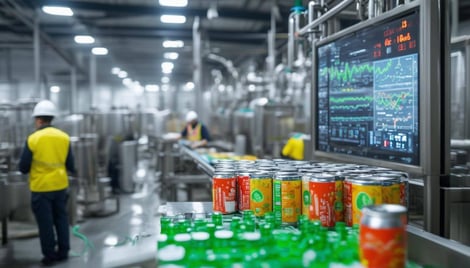
Best Practices for Synchronizing Production with Demand
To maximize the potential of PlanetTogether and ERP integrations, production schedulers should adopt the following best practices:
Demand Forecasting with Data Analytics
Leverage advanced demand forecasting tools integrated with ERP systems. These forecasts should account for historical sales data, seasonal trends, and external factors like market trends or supply chain disruptions.
Collaborative Planning
Ensure seamless communication between supply chain teams, production planners, and sales departments. PlanetTogether’s collaborative features and ERP integration can bridge these gaps effectively.
Dynamic Scheduling
Adopt a flexible approach to scheduling. Use what-if scenario analysis to prepare for demand changes, and ensure the ability to pivot production schedules quickly.
Inventory Optimization
Track and control inventory levels rigorously. Real-time visibility into raw materials and finished goods ensures production schedules align with demand without leading to overstock or shortages.
Monitor Key Metrics
Regularly evaluate metrics like On-Time Delivery (OTD), inventory turnover, and production efficiency. Tools like PlanetTogether provide detailed reports to help production schedulers measure success and identify areas for improvement.
As food and beverage manufacturers face increasing demand variability and supply chain disruptions, the role of production schedulers will continue to evolve. Advanced tools like PlanetTogether, integrated with ERP systems, are no longer optional—they’re essential for staying competitive.
Future developments, such as the integration of artificial intelligence (AI) and machine learning (ML) into these systems, promise even greater precision in demand forecasting and production scheduling. Production schedulers who adopt these technologies will be better equipped to anticipate market changes, reduce waste, and deliver consistent value to their organizations.
Synchronizing production with demand is a complex but critical task in food and beverage manufacturing. Tools like PlanetTogether, when integrated with ERP systems such as SAP, Oracle, Microsoft Dynamics, Kinaxis, or Aveva, empower production schedulers to make informed decisions, optimize resources, and meet customer expectations with precision.
By embracing technology, adopting best practices, and fostering collaboration across teams, production schedulers can transform challenges into opportunities, ensuring their facilities are poised for long-term success in a dynamic market.
Are you ready to take your manufacturing operations to the next level? Contact us today to learn more about how PlanetTogether can help you achieve your goals and drive success in your industry.