Sustainable Logistics: Scalable, Reliable, and Effective Solutions
The role of a Production Scheduler is pivotal in food and beverage manufacturing. Not only are they tasked with ensuring efficient production processes, but they are also increasingly responsible for integrating sustainable logistics practices into their operations. Sustainability is no longer just a buzzword; it's a necessity. Consumers are demanding it, regulations are enforcing it, and businesses are recognizing its importance for long-term viability.
This blog aims to look into the realm of sustainable logistics, exploring scalable, reliable, and effective solutions tailored to the needs of production schedulers in food and beverage manufacturing facilities.
We'll also touch upon the integration between PlanetTogether, a leading production planning software, and various ERP (Enterprise Resource Planning), SCM (Supply Chain Management), and MES (Manufacturing Execution Systems) solutions like SAP, Oracle, Microsoft, Kinaxis, and Aveva, to streamline operations and enhance sustainability efforts.
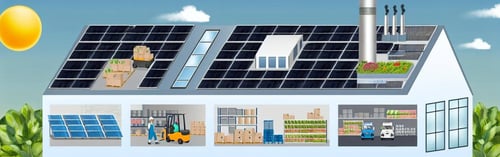
What are Sustainable Logistics?
Sustainable logistics encompasses a range of practices aimed at reducing environmental impact, optimizing resource utilization, and promoting social responsibility throughout the supply chain. From sourcing raw materials to delivering finished products, every step in the logistics process offers opportunities for sustainability improvements.
Key elements of sustainable logistics include:
Green Transportation: Utilizing eco-friendly modes of transportation, such as electric vehicles, hybrid trucks, or even alternative fuels, to reduce carbon emissions and minimize environmental footprint.
Efficient Route Planning: Optimizing delivery routes to minimize fuel consumption, reduce congestion, and decrease overall transportation costs while maintaining timely deliveries.
Waste Reduction: Implementing strategies to minimize packaging waste, food spoilage, and other forms of waste generation throughout the supply chain.
Responsible Sourcing: Partnering with suppliers who adhere to sustainable practices, such as fair trade principles, organic farming, and ethical labor standards.
Now, let's explore how production schedulers can implement scalable, reliable, and effective solutions to embed sustainability into their logistics operations.
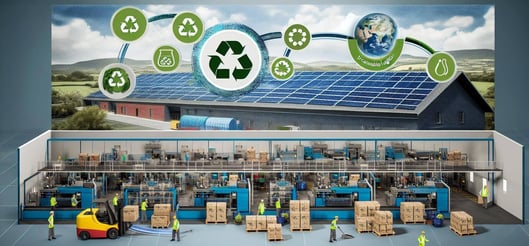
Scalable Solutions for Sustainable Logistics
Dynamic Production Scheduling: Leverage advanced production scheduling software like PlanetTogether to dynamically adjust production schedules based on real-time data. By synchronizing production with demand fluctuations, you can minimize overproduction, reduce inventory levels, and decrease the need for expedited shipping, thus cutting down on carbon emissions and waste.
Demand Forecasting Integration: Integrate your production scheduling software with ERP systems like SAP, Oracle, or Microsoft Dynamics to enhance demand forecasting accuracy. By having a clear understanding of demand patterns, you can optimize production schedules, minimize stockouts, and prevent excess inventory buildup, leading to more sustainable inventory management practices.
Collaborative Supply Chain Planning: Foster collaboration with suppliers, distributors, and other stakeholders through SCM platforms like Kinaxis or Aveva. By sharing demand forecasts, production schedules, and inventory levels in real-time, you can streamline procurement processes, reduce lead times, and minimize transportation inefficiencies, ultimately contributing to a more sustainable supply chain.
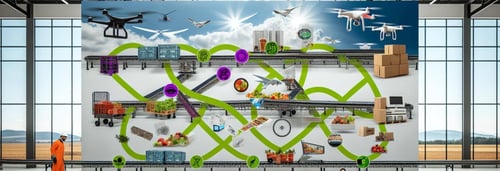
Reliable Solutions for Sustainable Logistics
Real-Time Visibility: Invest in MES solutions that provide real-time visibility into production processes, inventory levels, and logistics operations. By having access to accurate and up-to-date information, production schedulers can make informed decisions, identify bottlenecks, and proactively address issues before they escalate, ensuring reliable and efficient supply chain operations.
Quality Control Measures: Implement robust quality control measures throughout the production process to minimize defects, rework, and waste. By ensuring product quality and consistency, you can reduce the likelihood of product recalls, minimize food waste, and enhance customer satisfaction, thereby improving the reliability of your supply chain.
Contingency Planning: Develop contingency plans and risk mitigation strategies to address potential disruptions, such as natural disasters, transportation delays, or supplier issues. By having backup suppliers, alternative transportation routes, and contingency production schedules in place, you can minimize the impact of disruptions on your supply chain and maintain reliable operations, even in challenging circumstances.
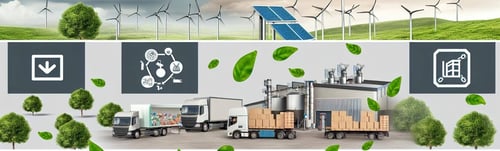
Effective Solutions for Sustainable Logistics
Continuous Improvement Culture: Foster a culture of continuous improvement within your organization, where employees are empowered to identify inefficiencies, propose innovative solutions, and implement sustainable practices. By encouraging collaboration, creativity, and accountability, you can drive ongoing improvements in your logistics operations and achieve long-term sustainability goals.
Employee Training and Development: Invest in training and development programs to equip employees with the knowledge, skills, and tools they need to excel in their roles. By providing ongoing education on sustainability best practices, technology utilization, and industry trends, you can empower production schedulers to drive positive change and make meaningful contributions to sustainable logistics efforts.
Performance Metrics and KPIs: Establish key performance indicators (KPIs) and metrics to measure the effectiveness of your sustainable logistics initiatives. By tracking metrics such as carbon emissions, waste reduction, on-time delivery performance, and cost savings, you can evaluate the impact of your efforts, identify areas for improvement, and drive continuous progress towards sustainability goals.
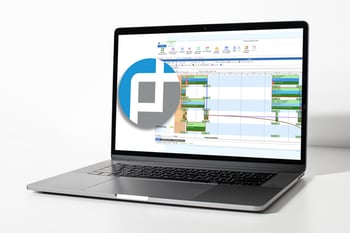
Integration with PlanetTogether and ERP, SCM, MES Systems
Integration between production scheduling software like PlanetTogether and ERP, SCM, and MES systems is essential for seamless data exchange, streamlined operations, and enhanced decision-making capabilities. By integrating with leading ERP systems such as SAP, Oracle, Microsoft Dynamics, Kinaxis, and Aveva, production schedulers can achieve greater visibility, agility, and efficiency across the entire supply chain.
Data Synchronization: Integration enables real-time synchronization of data between production scheduling software and ERP systems, ensuring that production plans align with demand forecasts, inventory levels, and resource availability. This allows production schedulers to make informed decisions based on accurate and up-to-date information, leading to more effective production scheduling and inventory management.
Streamlined Workflows: Integration streamlines workflows by automating data exchange and eliminating manual data entry tasks. This reduces the risk of errors, improves data accuracy, and enhances overall operational efficiency, enabling production schedulers to focus on strategic decision-making rather than administrative tasks.
Enhanced Visibility: Integration provides enhanced visibility into production processes, inventory levels, and supply chain performance by consolidating data from multiple systems into a single, centralized platform. This allows production schedulers to identify trends, analyze performance metrics, and proactively address issues, leading to more agile and responsive supply chain operations.
Optimized Resource Utilization: Integration enables optimization of resource utilization by providing visibility into capacity constraints, production bottlenecks, and resource availability. This allows production schedulers to allocate resources more efficiently, minimize idle time, and maximize throughput, resulting in improved productivity and cost savings.
Sustainable logistics is not just a lofty ideal; it's a strategic imperative for food and beverage manufacturing facilities looking to thrive in today's competitive landscape. By implementing scalable, reliable, and effective solutions tailored to the needs of production schedulers, companies can reduce their environmental footprint, enhance operational efficiency, and drive long-term value creation.
Integration between production scheduling software like PlanetTogether and ERP, SCM, and MES systems is instrumental in achieving these objectives, enabling seamless data exchange, streamlined operations, and enhanced decision-making capabilities. By harnessing the power of technology and collaboration, production schedulers can lead the charge towards a more sustainable future for the food and beverage industry.
Remember, sustainability is not a destination; it's a journey. Embrace the challenge, seize the opportunities, and together, we can build a more sustainable and resilient supply chain for generations to come. Are you ready to take your manufacturing operations to the next level? Contact us today to learn more about how PlanetTogether can help you achieve your goals and drive success in your industry.