Sustainability and Operational Excellence Hand in Hand
Packaging manufacturing facilities face increasing pressure to balance operational efficiency with sustainability. Purchasing Managers play a crucial role in this dynamic by selecting suppliers, materials, and technologies that optimize production while reducing environmental impact. Achieving this balance is more than a trend—it's essential for long-term success in a marketplace where consumers, regulators, and stakeholders demand accountability and green practices.
One of the ways manufacturers can stay ahead is by embracing advanced software solutions that integrate operational excellence with sustainability. Integrating supply chain management tools like PlanetTogether with ERP systems such as SAP, Oracle, Microsoft Dynamics, Kinaxis, and Aveva can lead to transformative results.
This blog will look into strategies that Purchasing Managers can adopt to drive sustainability while maintaining or even enhancing operational efficiency in packaging manufacturing.
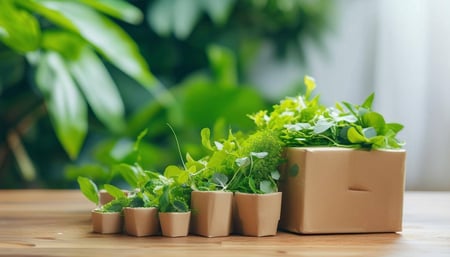
The Increasing Importance of Sustainability in Packaging Manufacturing
The global packaging industry is valued at over $900 billion, with continued growth driven by evolving consumer preferences, regulatory pressures, and the push for more sustainable practices. For Purchasing Managers, the mandate is clear: find ways to source environmentally friendly materials and improve production efficiencies, all while controlling costs.
In the packaging sector, the demand for sustainable materials like biodegradable plastics, paper-based alternatives, and recycled content has surged. But sustainability goes beyond the materials used; it encompasses energy-efficient production, reduced waste, and minimized carbon footprints.
According to the World Economic Forum, nearly 90% of business leaders agree that sustainability is critical to success. However, only a small percentage of companies are equipped with the necessary tools and strategies to embed sustainability into every aspect of their operations. For Purchasing Managers, this gap is an opportunity to lead change by leveraging technology and strategic partnerships.
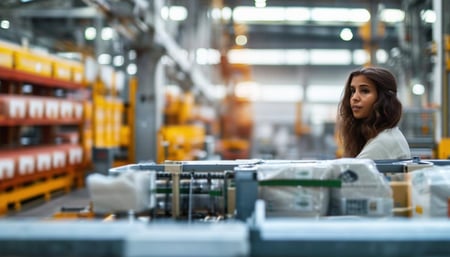
Operational Excellence: The Cornerstone of Profitability
While sustainability is a high priority, it cannot come at the expense of operational efficiency. Operational excellence involves streamlining processes, optimizing resources, and ensuring the consistent delivery of quality products on time and within budget. For a Purchasing Manager in a packaging manufacturing facility, the ability to ensure the right materials are available at the right time is critical to maintaining operational flow and avoiding costly delays.
Fortunately, the rise of advanced planning and scheduling (APS) software such as PlanetTogether has provided packaging manufacturers with the ability to balance complex operational requirements. When integrated with robust enterprise resource planning (ERP) systems like SAP, Oracle, or Microsoft Dynamics, these tools can deliver significant gains in productivity, reduce waste, and enhance sustainability efforts.

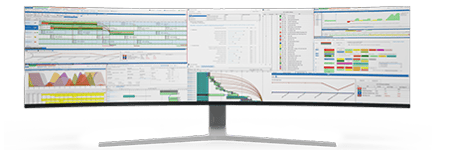
The Role of Advanced Planning and Scheduling (APS) in Sustainability
Advanced Planning and Scheduling (APS) systems like PlanetTogether enable companies to optimize production schedules by factoring in not just traditional metrics like lead time, costs, and capacity but also sustainability considerations. This includes energy consumption, carbon emissions, and waste reduction.
Integration of PlanetTogether with ERP Systems
Integrating PlanetTogether with an ERP system like SAP, Oracle, or Microsoft Dynamics provides a holistic view of the supply chain and manufacturing operations. This integration allows real-time data sharing, which is crucial for making informed decisions on procurement, scheduling, and inventory management.
For example, a facility using SAP for resource planning and financials can seamlessly integrate PlanetTogether to gain insight into production schedules and environmental impact simultaneously. The integration enables Purchasing Managers to prioritize sustainable suppliers, schedule production during off-peak energy times to reduce carbon footprints, and manage resources in a way that minimizes waste.
PlanetTogether’s real-time visibility into production and sustainability metrics is a game-changer for facilities looking to achieve operational excellence while meeting sustainability targets.
Benefits of APS-ERP Integration for Purchasing Managers
-
Sustainable Procurement: By integrating systems, Purchasing Managers can ensure they are sourcing materials that meet sustainability standards without sacrificing production schedules or budgets.
-
Energy Efficiency: Integrated systems allow the optimization of production schedules based on energy usage. For example, off-peak electricity usage or renewable energy sources can be factored into production timelines, reducing overall energy consumption.
-
Waste Reduction: Real-time data from APS and ERP integration helps identify bottlenecks and inefficiencies in production, leading to waste reduction in both materials and time.
-
Enhanced Supplier Collaboration: With integrated systems, Purchasing Managers can collaborate more effectively with suppliers, ensuring that both parties are aligned in terms of sustainability goals and operational needs.
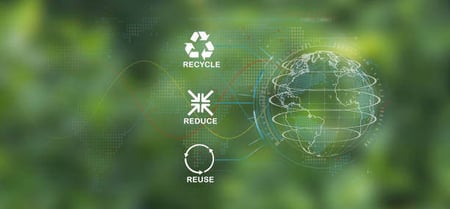
Key Strategies for Success in Sustainable Operations
Achieving sustainability while maintaining operational excellence requires a strategic approach that leverages technology, builds strong supplier relationships, and integrates sustainability into every phase of production. Here are some key strategies for success:
Supplier Selection with Sustainability in Mind
Selecting suppliers that align with your sustainability goals is crucial. By using tools like PlanetTogether integrated with your ERP, you can evaluate suppliers based on both cost and sustainability metrics. For instance, purchasing managers can prioritize suppliers with lower carbon footprints or those who offer recycled or biodegradable materials.
Technology can also provide insight into the long-term environmental impact of different materials, helping Purchasing Managers make decisions that balance cost, quality, and sustainability. When integrated with systems like SAP or Oracle, these tools allow for better tracking and reporting on sustainable procurement efforts, making it easier to measure and demonstrate progress.
Material Sourcing and Inventory Optimization
Effective material sourcing is a key area where technology and sustainability intersect. Sourcing materials closer to your manufacturing facility not only reduces transportation costs but also lowers your carbon footprint. Additionally, real-time inventory tracking and demand forecasting can help minimize excess materials that might otherwise go to waste.
PlanetTogether, when integrated with systems like Microsoft Dynamics or Kinaxis, can provide valuable insights into demand planning and inventory management. This allows Purchasing Managers to optimize order quantities, reduce overproduction, and ensure materials are used efficiently. By reducing excess inventory, you not only save on storage costs but also avoid the disposal of unused materials, aligning with sustainability objectives.
Optimizing Energy Consumption in Production
Energy is one of the largest cost drivers in packaging manufacturing. Purchasing Managers can leverage integrated APS and ERP systems to identify energy-intensive processes and work with operations teams to reduce energy consumption. For example, scheduling production during periods of lower energy demand can significantly reduce costs and carbon emissions.
Software solutions like PlanetTogether allow for more detailed energy usage tracking by integrating with your facility’s systems and feeding data into your ERP platform. The ability to optimize production schedules based on energy efficiency can lead to significant savings and align with broader sustainability initiatives.
Circular Economy and Closed-Loop Manufacturing
The concept of a circular economy is gaining traction in packaging manufacturing, where the focus is on reducing waste by keeping materials in use for as long as possible. Purchasing Managers can play a key role in this by sourcing recycled materials or selecting suppliers that offer products designed for reuse.
Integrating systems like Aveva’s industrial software with PlanetTogether can facilitate closed-loop manufacturing processes by providing real-time data on material use, waste generation, and recycling efforts. This helps ensure that materials are used efficiently, waste is minimized, and sustainability goals are met.
Leveraging Data for Continuous Improvement
Data is a powerful tool for driving continuous improvement in both sustainability and operational excellence. By integrating advanced planning and scheduling software with ERP systems, Purchasing Managers gain access to comprehensive data on everything from material usage to energy consumption and waste.
This data can be used to set benchmarks, track progress, and make informed decisions that align with both financial and environmental objectives. Furthermore, the integration allows for more accurate reporting and auditing of sustainability efforts, which is increasingly important as consumers and regulators demand transparency.
For example, an integration between PlanetTogether and Kinaxis enables Purchasing Managers to use predictive analytics to forecast demand, optimize inventory, and reduce waste. These insights can lead to more efficient operations and a stronger commitment to sustainability.
The role of Purchasing Managers will become even more critical in balancing operational efficiency with sustainability. By leveraging advanced tools like PlanetTogether and integrating them with ERP systems such as SAP, Oracle, Microsoft Dynamics, Kinaxis, and Aveva, Purchasing Managers can ensure they are not only meeting today’s demands but also preparing for a more sustainable future.
Operational excellence and sustainability are no longer separate goals—they are two sides of the same coin. By embracing technology, building strong supplier partnerships, and continuously striving for improvement, Purchasing Managers can lead their facilities toward a future where sustainability and profitability go hand in hand.
As we move forward, the companies that can successfully integrate sustainability into their operations will be the ones that thrive in an increasingly complex and environmentally conscious world. For Purchasing Managers in packaging manufacturing, the time to act is now.
Sustainability and operational excellence are no longer mutually exclusive goals. Through the integration of APS systems like PlanetTogether with ERP platforms like SAP, Oracle, Microsoft Dynamics, and others, Purchasing Managers in packaging manufacturing can drive meaningful change. By implementing these strategies—focusing on sustainable procurement, optimizing energy consumption, embracing circular economy principles, and leveraging data—companies can enhance both their environmental and financial performance.
Are you ready to take your manufacturing operations to the next level? Contact us today to learn more about how PlanetTogether can help you achieve your goals and drive success in your industry.