Supply Chain Reassessment with Integrated Planning Solutions
In the global marketplace, supply chain managers in the food and beverage manufacturing industry face a myriad of challenges. From fluctuating consumer demands to supply chain disruptions, the need for agility and efficiency has never been greater.
In this blog, we will explore the concept of supply chain reassessment and how integrating advanced planning solutions like PlanetTogether with leading ERP systems such as SAP, Oracle, Microsoft, Kinaxis, and Aveva can revolutionize operations in food and beverage manufacturing facilities.
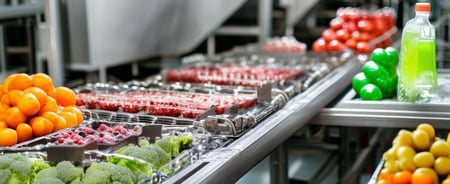
The Need for Supply Chain Reassessment
The traditional approach to supply chain management often involves siloed processes and fragmented systems, leading to inefficiencies and missed opportunities. However, in today's hyper-connected world, supply chain reassessment is essential for staying competitive. By reevaluating existing processes and adopting integrated planning solutions, food and beverage manufacturers can optimize their supply chains for greater resilience, agility, and profitability.

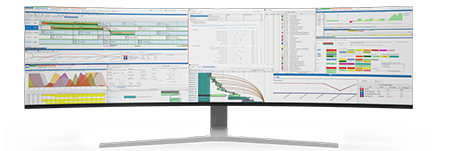
The Role of Integrated Planning Solutions
Integrated planning solutions like PlanetTogether offer supply chain managers powerful tools for streamlining operations, optimizing production schedules, and improving resource utilization. By integrating these solutions with ERP systems such as SAP, Oracle, Microsoft, Kinaxis, and Aveva, manufacturers can achieve end-to-end visibility and control over their entire supply chain ecosystem.
Benefits of Integration
Enhanced Visibility: Integration between PlanetTogether and leading ERP systems provides real-time insights into inventory levels, production schedules, and demand forecasts. This visibility enables supply chain managers to make informed decisions and respond swiftly to changing market dynamics.
Streamlined Operations: By automating planning and scheduling processes, integrated solutions reduce manual effort and minimize the risk of human error. This leads to more accurate production schedules, reduced lead times, and improved on-time delivery performance.
Optimal Resource Utilization: Integrated planning solutions optimize resource utilization by synchronizing production schedules with available capacity and inventory levels. This ensures that resources such as raw materials, equipment, and labor are utilized efficiently, minimizing waste and reducing costs.
Improved Collaboration: Integration fosters collaboration between different departments and stakeholders within the organization, as well as with external partners and suppliers. By sharing real-time data and insights, teams can work together more effectively to address supply chain challenges and drive continuous improvement.
Supply chain reassessment is essential for food and beverage manufacturers seeking to thrive in today's competitive landscape. By integrating advanced planning solutions like PlanetTogether with leading ERP systems, companies can optimize their supply chains for greater agility, efficiency, and resilience. Integration enables real-time visibility, streamlined operations, and improved collaboration, ultimately driving sustainable growth and success.
Are you ready to take your manufacturing operations to the next level? Contact us today to learn more about how PlanetTogether and integrated scheduling solutions can help you achieve your sustainability goals and drive success in the food and beverage industry.