Supplier Performance Management Systems
In food and beverage manufacturing, ensuring seamless operations requires meticulous planning, precise execution, and effective supplier management. As a production scheduler, your role is pivotal in orchestrating the intricate dance between demand and supply.
In this blog, we'll look into the realm of Supplier Performance Management Systems (SPMS) and how they integrate with production scheduling tools like PlanetTogether and leading enterprise resource planning (ERP) systems such as SAP, Oracle, Microsoft, Kinaxis, and Aveva.
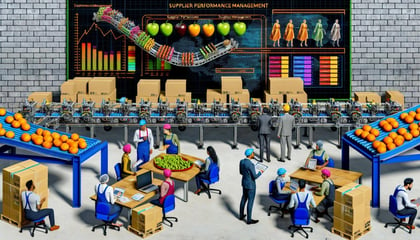
Supplier Performance Management Systems
Supplier performance management encompasses the processes and systems designed to evaluate, measure, and improve the performance of suppliers throughout the supply chain. SPMS plays a crucial role in mitigating risks, ensuring quality, and optimizing costs associated with procuring raw materials and ingredients.
Challenges in Supplier Management
In the food and beverage industry, where quality and safety are paramount, managing suppliers poses unique challenges. These challenges include:
Quality Control: Ensuring consistent quality of raw materials to maintain product standards and comply with regulations.
Lead Time Variability: Dealing with fluctuations in lead times, which can disrupt production schedules and impact customer satisfaction.
Supplier Reliability: Dependability of suppliers in meeting delivery schedules and adhering to agreed-upon terms.
Cost Optimization: Balancing cost considerations with quality requirements to maximize profitability.
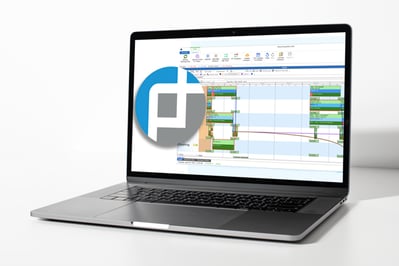
Integration with Production Scheduling Tools
Effective integration between SPMS and production scheduling tools is essential for streamlining operations and optimizing resource utilization. PlanetTogether, a leading production scheduling software, offers robust features that align with SPMS objectives:
Real-Time Data Exchange: Seamless integration allows for the exchange of real-time data between SPMS and PlanetTogether, enabling accurate demand forecasting and efficient scheduling.
Automated Alerts: Integration enables automated alerts triggered by deviations in supplier performance metrics, allowing proactive resolution of issues to prevent disruptions.
Dynamic Scheduling: Utilizing data from SPMS, PlanetTogether dynamically adjusts production schedules in response to changes in supplier performance, ensuring continuity in operations.
Scenario Analysis: By leveraging historical supplier data within SPMS, production schedulers can conduct scenario analysis in PlanetTogether to evaluate the impact of supplier performance on production timelines and resource allocation.
SPMS Integration with ERP Systems
In addition to production scheduling tools, SPMS integration with ERP systems such as SAP, Oracle, Microsoft Dynamics, Kinaxis, and Aveva enhances visibility and control across the entire supply chain:
End-to-End Visibility: Seamless data flow between SPMS and ERP systems provides production schedulers with comprehensive visibility into supplier performance metrics, inventory levels, and production schedules.
Data Standardization: Integration ensures consistency and accuracy of data across systems, eliminating discrepancies and enhancing decision-making capabilities.
Supplier Collaboration: ERP-integrated SPMS facilitates collaboration between internal stakeholders and suppliers, enabling effective communication and alignment of objectives.
Performance Analytics: ERP systems leverage advanced analytics capabilities to analyze supplier performance trends, identify areas for improvement, and drive continuous optimization.
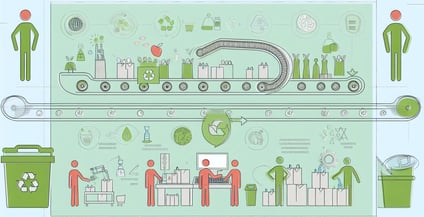
Best Practices for Implementing SPMS
To maximize the benefits of SPMS integration, production schedulers should adopt the following best practices:
Define Key Performance Indicators (KPIs): Identify and define relevant KPIs to measure supplier performance, such as on-time delivery, lead time variability, and quality compliance.
Establish Clear Communication Channels: Foster open communication channels with suppliers to provide feedback, address issues, and collaborate on improvement initiatives.
Implement Continuous Improvement Processes: Encourage a culture of continuous improvement by regularly evaluating supplier performance, implementing corrective actions, and sharing best practices.
Invest in Training and Development: Equip production scheduling teams with the necessary training and tools to effectively utilize SPMS and leverage integration capabilities with ERP and production scheduling software.
In food and beverage manufacturing, optimizing supplier performance is essential to maintaining competitive advantage and meeting customer expectations. By leveraging Supplier Performance Management Systems and integrating them with production scheduling tools like PlanetTogether and leading ERP systems, production schedulers can enhance visibility, control, and agility across the supply chain.
Embracing best practices and fostering collaboration with suppliers will empower organizations to navigate challenges, drive efficiency, and achieve sustainable growth in the dynamic landscape of food and beverage manufacturing.
As a production scheduler, embracing the integration of SPMS with your existing systems is not just a choice but a necessity in today's competitive environment. By doing so, you're not just optimizing processes; you're ensuring the foundation for long-term success in the industry.
Are you ready to take your manufacturing operations to the next level? Contact us today to learn more about how PlanetTogether can help you achieve your goals and drive success in your industry.
LEAVE A COMMENT