Streamlining Production Planning
As a Purchasing Manager in a Food and Beverage manufacturing facility, you understand the importance of smooth production planning processes. With the increasing complexity of supply chains and customer demands, integrating advanced planning software with ERP, SCM, and MES systems becomes crucial.
In this blog, we'll look into the significance of production planning in food manufacturing and explore how integration between PlanetTogether and leading ERP, SCM, and MES systems can revolutionize your operations.
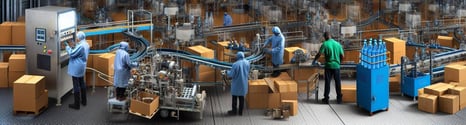
Identifying the Challenges
Let's identify the challenges faced by food manufacturers in production planning. These challenges include:
Fluctuating Demand: Food trends can change rapidly, leading to unpredictable demand patterns.
Ingredient Availability: Sourcing quality ingredients consistently can be a challenge due to seasonality, supplier issues, or market fluctuations.
Regulatory Compliance: Adhering to stringent food safety regulations adds complexity to production planning processes.
Waste Reduction: Minimizing waste while ensuring optimal inventory levels is essential for profitability and sustainability.
Addressing these challenges requires a holistic approach that optimizes resource utilization, minimizes waste, and ensures timely delivery to customers.
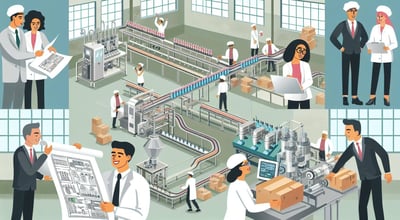
The Role of Production Planning
Production planning is the backbone of efficient food manufacturing operations. It involves forecasting demand, scheduling production runs, managing inventory levels, and optimizing resource allocation. A well-executed production plan enables you to:
- Meet customer demand while minimizing stockouts and overstock situations.
- Optimize production schedules to maximize equipment utilization and minimize downtime.
- Improve inventory management by synchronizing procurement with production schedules.
- Enhance agility to respond quickly to changing market conditions and customer preferences.

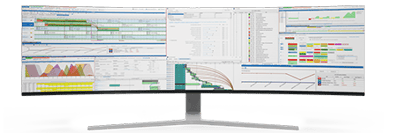
Integration between PlanetTogether and ERP, SCM, and MES Systems
Now, let's explore how integration between PlanetTogether, a leading production planning software, and popular ERP, SCM, and MES systems such as SAP, Oracle, Microsoft, Kinaxis, and Aveva can elevate your production planning capabilities.
Seamless Data Exchange: Integration enables seamless data exchange between production planning and other systems, ensuring real-time visibility into inventory levels, production schedules, and resource availability.
Enhanced Accuracy: By integrating with ERP systems, production plans can be based on accurate demand forecasts, inventory data, and procurement schedules, leading to more precise production scheduling and inventory management.
Improved Collaboration: Integration fosters collaboration across departments by providing a centralized platform where stakeholders can access up-to-date information and communicate effectively, leading to better decision-making and alignment of objectives.
Automated Workflows: Integration automates repetitive tasks such as data entry, order processing, and scheduling, freeing up valuable time for your team to focus on strategic initiatives and problem-solving.
Better Traceability and Compliance: Integration ensures traceability of ingredients and finished products throughout the supply chain, enabling you to meet regulatory requirements and maintain high standards of food safety and quality.
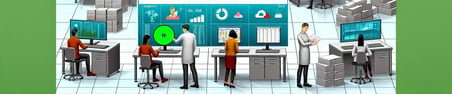
Best Practices for Successful Integration
To maximize the benefits of integration between PlanetTogether and ERP, SCM, and MES systems, consider the following best practices:
- Define clear objectives and key performance indicators (KPIs) to measure the success of the integration project.
- Ensure buy-in from all stakeholders and provide training to users to facilitate adoption.
- Collaborate closely with your IT department and software vendors to ensure smooth implementation and ongoing support.
- Regularly monitor and evaluate performance metrics to identify areas for improvement and optimization.
- Stay informed about new technologies and industry trends to continuously enhance your production planning capabilities.
Production planning plays a critical role in the success of food manufacturing operations. By integrating advanced planning software like PlanetTogether with ERP, SCM, and MES systems, you can streamline your production planning processes, improve efficiency, and stay ahead of the competition.
Embrace integration as a strategic initiative to drive innovation, enhance collaboration, and achieve operational excellence in your food manufacturing facility.
Are you ready to take your manufacturing operations to the next level? Contact us today to learn more about how PlanetTogether and integrated scheduling solutions can help you achieve your sustainability goals and drive success in the food and beverage industry.
LEAVE A COMMENT