Material Flow: Implementing Multi-Modal Systems
Efficiency is the cornerstone of success in pharmaceutical manufacturing. As the industry evolves, so do the challenges faced by manufacturers. One critical aspect is optimizing material flow within facilities. With the advent of advanced technology, implementing multi-modal systems has become a game-changer, allowing for smoother operations and enhanced productivity.
In this blog, we look into the significance of multi-modal systems and explore the integration of PlanetTogether with leading ERP, SCM, and MES systems to achieve seamless material flow in pharmaceutical manufacturing facilities.
Multi-Modal Systems
Multi-modal systems refer to the integration of various modes of transportation and handling within manufacturing facilities. This approach incorporates a combination of conveyors, automated guided vehicles (AGVs), robotics, and other technologies to facilitate the movement of materials from one point to another efficiently.
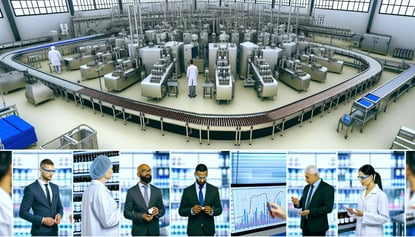
Advantages of Multi-Modal Systems
Enhanced Efficiency: By utilizing multiple modes of transportation, multi-modal systems optimize material flow, reducing bottlenecks and minimizing idle time. This results in streamlined processes and improved overall efficiency.
Flexibility: Multi-modal systems offer flexibility in adapting to changing production demands and facility layouts. They can be customized to accommodate different types of materials and production setups, ensuring agility in operations.
Reduced Errors: Automation inherent in multi-modal systems minimizes the risk of human errors, leading to higher accuracy and consistency in material handling and processing.
Cost Savings: Efficient material flow translates to cost savings by reducing labor requirements, minimizing downtime, and optimizing resource utilization. This contributes to a more competitive edge in the market.

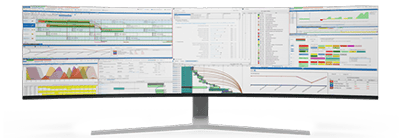
Integration with ERP, SCM, and MES Systems
To maximize the benefits of multi-modal systems, seamless integration with Enterprise Resource Planning (ERP), Supply Chain Management (SCM), and Manufacturing Execution Systems (MES) is crucial. Among the leading software solutions in this space are SAP, Oracle, Microsoft, Kinaxis, and Aveva.
PlanetTogether, a comprehensive production planning and scheduling software, plays a pivotal role in orchestrating the integration between multi-modal systems and these enterprise solutions. Let's explore how PlanetTogether facilitates this integration:
SAP Integration
PlanetTogether seamlessly integrates with SAP, enabling real-time data exchange between production planning and execution processes. This integration ensures that material flow aligns with production schedules and resource availability, optimizing operational efficiency.
Oracle Integration
By integrating with Oracle ERP and SCM systems, PlanetTogether synchronizes production plans with inventory levels and demand forecasts. This synchronization ensures timely procurement of materials and optimal utilization of resources, driving cost savings and enhancing customer satisfaction.
Microsoft Integration
PlanetTogether's integration with Microsoft Dynamics ERP and SCM solutions enables comprehensive visibility into production processes and material flow. This integration empowers manufacturers to make data-driven decisions, optimize production schedules, and respond effectively to changing market dynamics.
Kinaxis Integration
Integration between PlanetTogether and Kinaxis RapidResponse enhances supply chain visibility and responsiveness. This integration enables real-time collaboration across the supply chain, from production planning to material procurement, ensuring agile and efficient material flow within facilities.
Aveva Integration
PlanetTogether's integration with Aveva MES solutions enables seamless coordination between production scheduling and shop floor operations. This integration ensures that material flow aligns with production priorities, minimizing lead times and maximizing throughput.
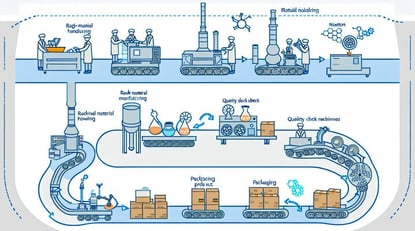
Implementation Best Practices
Implementing multi-modal systems for efficient material flow requires careful planning and execution. Here are some best practices to consider:
Assess Current Processes: Conduct a thorough assessment of existing material handling processes and identify areas for improvement.
Define Objectives: Clearly define the objectives of implementing multi-modal systems, such as reducing lead times, improving throughput, or minimizing costs.
Collaborate with IT and Operations Teams: Collaboration between IT and operations teams is essential to ensure smooth integration between multi-modal systems and existing enterprise solutions.
Pilot Testing: Conduct pilot tests to validate the effectiveness of multi-modal systems and fine-tune processes before full-scale implementation.
Training and Change Management: Provide comprehensive training to employees on operating and managing multi-modal systems. Implement change management strategies to ensure smooth transition and adoption.
In the competitive landscape of pharmaceutical manufacturing, optimizing material flow within facilities is imperative for success. Multi-modal systems offer a holistic approach to streamlining material handling processes, leveraging a combination of technologies to enhance efficiency, flexibility, and cost-effectiveness. By integrating with leading ERP, SCM, and MES systems such as SAP, Oracle, Microsoft, Kinaxis, and Aveva, PlanetTogether plays a crucial role in orchestrating seamless material flow within pharmaceutical manufacturing facilities.
Embracing multi-modal systems and leveraging advanced integration capabilities will empower manufacturers to stay ahead of the curve, drive operational excellence, and deliver value to customers in the ever-evolving pharmaceutical industry. Are you ready to take your manufacturing operations to the next level? Contact us today to learn more about how PlanetTogether can help you achieve your goals and drive success in your industry.
LEAVE A COMMENT