Hazardous Materials Handling Procedures
Ensuring the safety and efficiency of hazardous materials handling procedures is essential in medical manufacturing. As a Production Scheduler, you play a pivotal role in orchestrating the intricate dance of production processes while adhering to strict regulations and safety protocols.
In this blog, we'll look into the importance of efficient hazardous materials handling procedures and explore how integrating advanced scheduling software like PlanetTogether with leading ERP, SCM, and MES systems can enhance safety, compliance, and productivity.
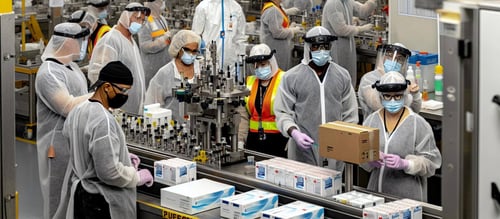
Understanding Hazardous Materials Handling
Before we look into the intricacies of scheduling and integration, let's first establish a solid understanding of hazardous materials handling in medical manufacturing facilities. Hazardous materials can range from flammable substances to toxic chemicals, and their mishandling can pose serious risks to both personnel and the environment. Proper handling involves meticulous planning, storage, transportation, and disposal procedures to mitigate these risks and ensure regulatory compliance.
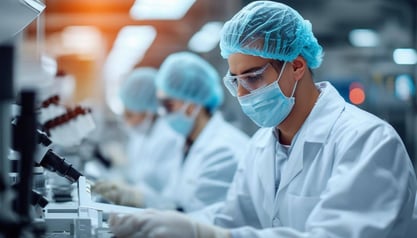
Challenges Faced by Production Schedulers
Production Schedulers encounter numerous challenges when it comes to managing hazardous materials within the manufacturing process. Some of these challenges include:
Compliance with Regulations: Regulatory bodies impose strict guidelines on the handling, storage, and transportation of hazardous materials. Navigating these regulations while maintaining production schedules can be a daunting task.
Inventory Management: Tracking and managing inventory levels of hazardous materials is crucial to prevent stockouts or overages, which can disrupt production schedules and compromise safety.
Scheduling Coordination: Coordinating the movement of hazardous materials within the production schedule while optimizing resource utilization requires precision and foresight.
Safety Protocols: Implementing and enforcing safety protocols to protect personnel and the environment from potential hazards is non-negotiable.

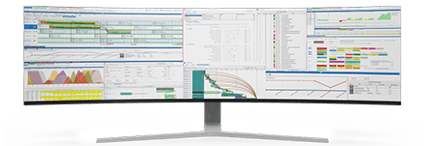
Integrating Advanced Scheduling Solutions
To address these challenges effectively, medical manufacturing facilities can benefit significantly from integrating advanced scheduling solutions like PlanetTogether with ERP, SCM, and MES systems. Let's explore how such integration can streamline hazardous materials handling procedures:
Real-Time Visibility: Integration between scheduling software and ERP systems provides real-time visibility into inventory levels, production schedules, and resource availability. This enables Production Schedulers to make informed decisions regarding the handling and movement of hazardous materials.
Automated Alerts and Notifications: By integrating scheduling software with MES systems, Production Schedulers can set up automated alerts and notifications for critical events such as inventory shortages, equipment failures, or deviations from safety protocols. This proactive approach enhances responsiveness and minimizes the risk of disruptions.
Resource Optimization: Advanced scheduling algorithms offered by solutions like PlanetTogether optimize resource allocation and production sequencing to minimize the handling of hazardous materials. By consolidating production tasks and reducing changeovers, these algorithms enhance efficiency while reducing the inherent risks associated with handling hazardous materials.
Compliance Management: Integration with ERP systems allows for seamless compliance management by incorporating regulatory requirements directly into the scheduling process. This ensures that production schedules adhere to applicable regulations regarding the handling, storage, and transportation of hazardous materials.
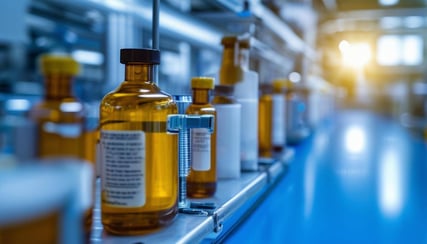
Best Practices for Effective Hazardous Materials Handling
In addition to leveraging advanced scheduling solutions and integration capabilities, adopting best practices can further enhance the safety and efficiency of hazardous materials handling procedures:
Employee Training: Provide comprehensive training to personnel involved in the handling, storage, and transportation of hazardous materials to ensure they understand safety protocols and regulatory requirements.
Risk Assessment: Conduct regular risk assessments to identify potential hazards and implement appropriate control measures to mitigate risks effectively.
Emergency Preparedness: Develop and regularly update emergency response plans to address potential incidents involving hazardous materials promptly and effectively.
Continuous Improvement: Foster a culture of continuous improvement by soliciting feedback from employees and stakeholders and implementing corrective actions to enhance safety and efficiency continually.
Efficient hazardous materials handling procedures are essential for ensuring the safety, compliance, and productivity of medical manufacturing facilities. By integrating advanced scheduling solutions like PlanetTogether with ERP, SCM, and MES systems, Production Schedulers can streamline processes, optimize resource utilization, and minimize risks associated with handling hazardous materials.
By adopting best practices and leveraging cutting-edge technology, medical manufacturing facilities can achieve operational excellence while prioritizing safety and regulatory compliance.
Are you ready to take your manufacturing operations to the next level? Contact us today to learn more about how PlanetTogether can help you achieve your goals and drive success in your industry.