Streamlining Capacity Planning and Management
Efficient capacity planning and management are important for success in Food and Beverage (F&B) manufacturing. As the industry faces evolving consumer demands, stringent regulations, and market volatility, manufacturers must adapt to optimize their operations.
In this blog, we look into the significance of capacity planning and management within F&B manufacturing and explore how integration between PlanetTogether and leading ERP, SCM, and MES systems revolutionizes this critical process.
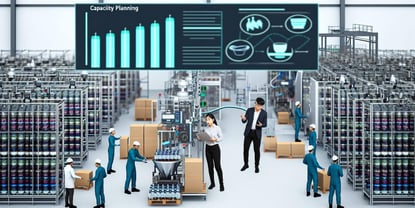
Capacity Planning and Management
Capacity planning involves determining the production capacity needed to meet current and future demand effectively. It encompasses forecasting demand, assessing available resources, and aligning production capabilities to fulfill requirements efficiently. Effective capacity management ensures optimal utilization of resources while maintaining high levels of productivity, quality, and customer satisfaction.
Challenges in F&B Manufacturing
F&B manufacturers encounter unique challenges in capacity planning and management due to the industry's complexities. These challenges include:
Seasonal Demand Fluctuations: F&B products often experience fluctuating demand influenced by factors like seasonal trends, holidays, and promotional activities.
Shelf Life Considerations: Products with limited shelf life require precise planning to minimize waste and ensure freshness.
Regulatory Compliance: Strict regulatory requirements regarding food safety, labeling, and traceability necessitate meticulous planning and adherence to standards.
Supply Chain Disruptions: Vulnerabilities in the supply chain, such as ingredient shortages or transportation delays, can impact production schedules and capacity utilization.
SKU Proliferation: F&B manufacturers deal with a wide range of SKUs, each with varying production requirements, further complicating capacity planning.

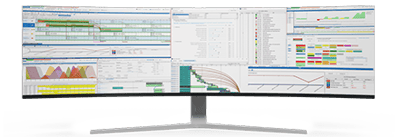
Integration for Enhanced Capacity Planning
Integration between advanced planning and scheduling (APS) tools like PlanetTogether and leading ERP, SCM, and MES systems offers a comprehensive solution to address these challenges. Let's explore how integration with prominent platforms enhances capacity planning and management:
SAP Integration: Integration with SAP enables seamless data exchange between production planning in PlanetTogether and core business processes in SAP ERP, facilitating real-time visibility, accurate forecasting, and synchronized production scheduling.
Oracle Integration: By integrating with Oracle ERP and SCM systems, F&B manufacturers can optimize inventory management, streamline order fulfillment, and achieve better synchronization between planning and execution processes.
Microsoft Dynamics Integration: Integration with Microsoft Dynamics enhances collaboration and decision-making by providing a unified platform for production planning, resource allocation, and performance tracking.
Kinaxis Integration: Integration with Kinaxis RapidResponse enables F&B manufacturers to leverage advanced analytics and scenario planning capabilities for agile decision-making and proactive risk management.
Aveva Integration: Integration with Aveva MES enhances shop floor control, quality management, and production tracking, ensuring seamless execution of capacity plans and adherence to operational standards.
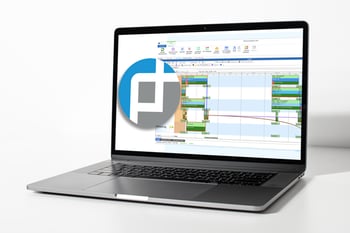
Benefits of Integrated Capacity Planning
The integration of PlanetTogether with leading ERP, SCM, and MES systems offers several benefits for F&B manufacturers:
Improved Efficiency: Real-time data exchange and synchronization optimize production schedules, minimize downtime, and enhance overall operational efficiency.
Enhanced Visibility: Integrated systems provide stakeholders with comprehensive visibility into production processes, resource utilization, and demand fluctuations, enabling informed decision-making and proactive intervention.
Agile Response to Change: Advanced analytics and scenario planning capabilities empower manufacturers to anticipate and respond swiftly to market dynamics, supply chain disruptions, and changing customer demands.
Cost Reduction: Optimized capacity planning reduces inventory carrying costs, minimizes waste, and enhances resource utilization, contributing to cost savings and improved profitability.
Compliance and Quality Assurance: Integrated systems ensure compliance with regulatory requirements and quality standards by facilitating traceability, documentation, and audit trails throughout the production process.
In the competitive landscape of F&B manufacturing, efficient capacity planning and management are critical for sustaining growth and profitability. Integration between PlanetTogether and leading ERP, SCM, and MES systems offers a comprehensive solution to address the industry's unique challenges and optimize production operations. By leveraging advanced planning and scheduling capabilities alongside robust integration capabilities, F&B manufacturers can enhance efficiency, agility, and compliance while meeting the demands of an ever-evolving market.
Incorporating integrated solutions into capacity planning and management processes empowers F&B manufacturers to navigate complexities, drive innovation, and achieve sustainable success in an increasingly competitive environment. As technology continues to evolve, embracing integration and collaboration across systems will remain essential for unlocking the full potential of capacity planning and propelling F&B manufacturing towards a future of excellence.
Are you ready to take your manufacturing operations to the next level? Contact us today to learn more about how PlanetTogether can help you achieve your goals and drive success in your industry.
LEAVE A COMMENT