Strategies for Growth Outperformance
The quest for growth and outperformance is perpetual in chemical manufacturing. With the demand for innovative products, stringent regulations, and evolving customer preferences, the industry demands agile and efficient strategies to stay ahead. Central to achieving growth outperformance is the optimization of manufacturing operations, and a key tool in this endeavor is integrated planning systems.
For planners in chemical manufacturing facilities, the integration of advanced planning tools like PlanetTogether with enterprise resource planning (ERP), supply chain management (SCM), and manufacturing execution systems (MES) such as SAP, Oracle, Microsoft, Kinaxis, Aveva, and others is vital. This integration unlocks a realm of possibilities, empowering planners to streamline processes, enhance decision-making, and drive sustainable growth.
-May-08-2024-04-36-12-8483-PM.png?width=263&height=42&name=logo%20(2)-May-08-2024-04-36-12-8483-PM.png)
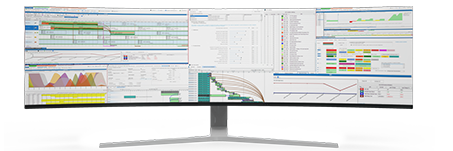
The Imperative of Integrated Planning Systems
Chemical manufacturing is a complex ecosystem with intricate processes, diverse product portfolios, and global supply chains. In such an environment, effective planning is pivotal to success. Integrated planning systems such as PlanetTogether offer a holistic approach that synchronizes various facets of operations, from demand forecasting and production scheduling to inventory management and resource allocation.
Seamless Data Integration: Integration between planning and enterprise systems eliminates silos and facilitates seamless data flow across departments. This ensures that planners have access to real-time, accurate information, enabling them to make informed decisions promptly.
Optimized Production Planning: By leveraging advanced algorithms and predictive analytics, integrated planning systems enable optimized production planning. Planners can analyze demand patterns, factor in constraints, and fine-tune schedules to maximize throughput while minimizing costs and lead times.
Enhanced Collaboration: Integration fosters collaboration among different functional areas, allowing for better coordination between production, procurement, logistics, and sales teams. This collaboration facilitates cross-functional alignment and enables agile responses to changing market dynamics.
Adaptive Capacity Planning: With integrated planning systems, capacity planning becomes more agile and adaptive. Planners can dynamically adjust production capacities based on demand fluctuations, market trends, and operational constraints, ensuring optimal utilization of resources while avoiding bottlenecks or overcapacity.
Continuous Improvement: Integrated systems provide a foundation for continuous improvement initiatives such as Lean, Six Sigma, and Total Quality Management (TQM). By analyzing performance metrics and identifying areas for optimization, planners can drive continuous improvements in efficiency, quality, and sustainability.

Leveraging Integration: Strategies for Growth Outperformance
Now that we understand the importance of integrated planning systems, let's explore some strategies for leveraging this integration to achieve growth outperformance in chemical manufacturing:
Demand-Driven Planning
Traditional planning approaches often rely on static forecasts, leading to inefficiencies and excess inventory. By integrating planning systems with advanced demand sensing technologies and customer relationship management (CRM) platforms, chemical manufacturers can adopt a demand-driven planning approach. Real-time demand signals, combined with predictive analytics, enable more accurate demand forecasting and proactive inventory management, reducing stockouts, minimizing carrying costs, and enhancing customer satisfaction.
Agile Production Scheduling
In today's fast-paced market, agility is a key differentiator. Integrated planning systems empower planners to embrace agile production scheduling methodologies such as Just-in-Time (JIT), Kanban, and Drum-Buffer-Rope (DBR). By synchronizing production schedules with demand fluctuations, market dynamics, and resource availability, manufacturers can minimize lead times, reduce work-in-progress (WIP) inventory, and respond swiftly to changing customer requirements.
Supply Chain Optimization
The resilience and efficiency of the supply chain are critical to sustained growth. Integration between planning systems and SCM platforms enables end-to-end visibility and optimization of the supply chain network. By analyzing factors such as supplier performance, lead times, transportation costs, and inventory levels, planners can identify bottlenecks, mitigate risks, and optimize sourcing strategies to ensure a reliable and cost-effective supply chain.
Collaborative Decision-Making
Growth outperformance requires alignment and collaboration across the organization. Integrated planning systems facilitate collaborative decision-making by providing stakeholders with a unified platform for data-driven insights and scenario analysis. Cross-functional teams can collaborate in real-time, evaluate alternative scenarios, and align on strategic objectives, fostering a culture of innovation and continuous improvement.
Performance Monitoring and KPI Management
To sustain growth outperformance, it is essential to monitor performance metrics and key performance indicators (KPIs) rigorously. Integrated planning systems offer robust analytics and reporting capabilities that enable planners to track KPIs such as production efficiency, on-time delivery, inventory turns, and cost per unit. By monitoring performance in real-time and conducting root cause analysis, manufacturers can identify areas for improvement, implement corrective actions, and drive operational excellence.
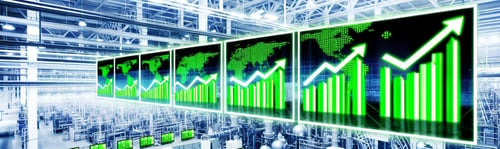
Achieving Growth Outperformance with Integrated Planning Systems
To illustrate the transformative impact of integrated planning systems, let's consider a case study of a leading chemical manufacturer:
Challenge: The company faced challenges in balancing production capacities with fluctuating demand, resulting in high inventory levels, increased lead times, and suboptimal resource utilization.
Solution: By integrating PlanetTogether with their existing SAP ERP system, the company implemented a demand-driven planning approach, leveraging real-time demand signals and predictive analytics to optimize production scheduling and inventory management.
Results: The integration enabled the company to achieve significant improvements in key performance metrics, including:
20% reduction in inventory carrying costs
30% decrease in lead times
15% increase in production efficiency
95% on-time delivery performance
As a result, the company not only achieved growth outperformance but also enhanced customer satisfaction and profitability.
The pursuit of growth outperformance requires a strategic approach to planning and operations in chemical manufacturing. Integrated planning systems serve as a catalyst for transformation, enabling manufacturers to optimize processes, enhance collaboration, and drive sustainable growth.
By leveraging integration between planning tools such as PlanetTogether and ERP, SCM, and MES systems, planners can unlock new opportunities for efficiency, agility, and innovation. With the right strategies and technologies in place, chemical manufacturers can navigate complexities, capitalize on market opportunities, and emerge as industry leaders in the pursuit of growth outperformance.
Through the integration of advanced planning tools with ERP, SCM, and MES systems, chemical manufacturers can streamline operations, enhance decision-making, and drive sustainable growth. As a planner in a chemical manufacturing facility, embracing integrated planning systems is not just a strategic choice; it's a pathway to achieving growth outperformance in a rapidly evolving industry.
Are you ready to take your manufacturing operations to the next level? Contact us today to learn more about how PlanetTogether can help you achieve your goals and drive success in your industry.