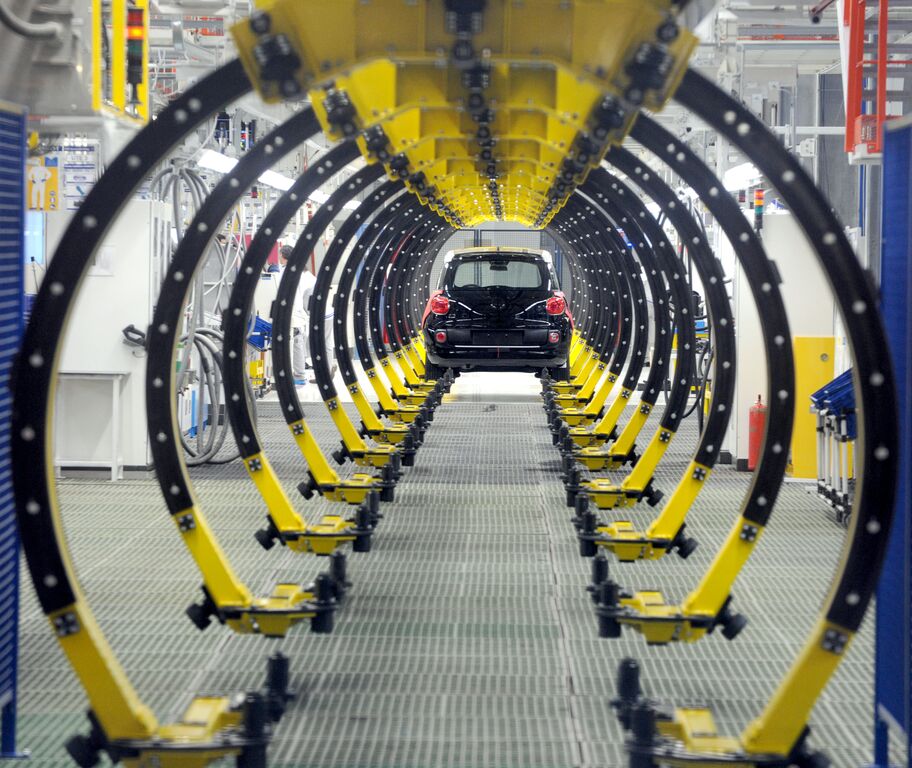
Strategic management is the planning. monitoring, analysis, and assessment of all aspects of an organization on a continuing basis. Attention to these elements ensures that a quality control strategy is developed and then implemented in the manufacturing facility. The benefits of strategic management will help manufacturing organizations make better decisions regarding production planning and scheduling, keep customers happy, and allow the facility to meet its overall goals.
Attention to these elements helps in formulating an operating strategy which specifies company-wide objectives and standards. Strategic management also requires that measures are put into place to determine if the strategies implemented are working as expected.
Customer-focused manufacturing companies need to adapt quickly to their customers' needs. One way to increase customer satisfaction toward your organization is to ensure that you have high-quality products.
Quality control is vital to organizations looking to meet these predetermined objectives. Ultimately, quality control is the key to meeting customers' expectations and needs as the customers themselves determine the level of quality of the items based on their satisfaction with the products.
Total Quality Control and Strategic Management
Total quality control is an approach aimed at achieving zero product defects, resulting in the production of a product which conforms to the desired standards. This method of addressing quality emphasizes the management and improvement of processes within the organization.
Like strategic management, this method views the company as a whole that contains interdependent functional areas that require a degree of flexibility to respond to changing market needs. Total quality control emphasizes the importance of involving all departments in the production process. These include accounting, design, finances, marketing, and purchasing.
Total quality control goes beyond ensuring that manufacturing processes are well defined and continuously improved. It also emphasizes that workers have the adequate knowledge and skill sets to perform the required processes and that there is a sense of integrity and organizational culture to foster quality.
Ensuring Quality and Efficiency
Viewing quality control as an end-to-end process involving multiple factors with continual examination of standards and results ensures the highest level of quality and efficiency. Total production efficiency can only be reached if the following factors are considered:
Production design must be simple.
It is easier to mistake-proof a simple process that has been designed for manufacturability. This requires a full understanding of the resources at hand, including labor's skill sets, equipment run information, market demand, and recognition of possible bottlenecks. Only then can a process be expected to be free of mistakes.
Continuous improvement of processes and product design will also result in decreases in costs incurred due to item re-work and will allow the overall production output to increase.
Recording and measuring resource performance in terms of expected quantities and hours worked against actual quantities and hours worked can help identify areas in need of improvement.
Quality control begins with quality vendors.
Reliable raw materials that arrive on time brings stability to the production process and allows a manufacturing organization to work using lean manufacturing strategies. The cost savings inherent in being able to hold to a limited inventory of materials helps keep profitability high down the line.
Choosing vendors that have quality control processes in place and have the right capabilities and qualification will help ensure that they consistently deliver high-quality products. Spot checking inbound material against requirements also builds good quality control within your facility.
Continuous attention to standards and guidelines are important.
Adhering to the quality measures set during the production design process will provide reliable data for analysis. It is important to develop product criteria and specifications that identify how a product should turn out.
If results are communicated in real-time, this will allow adjustments to be made quickly, before errors turn into waste, low quality products, missed deadlines, and customer dissatisfaction. This can be implemented by having real-time quality metrics displayed on the shop floor so that each team of workers is aware of how they compare to the quality goals.
Spot checks during manufacturing aid quality control.
Running smaller batches helps to catch problems early and will avoid waste that could result from longer runs of product. This is especially important when utilizing JIT production methods as there is often not enough time to re-work large batches.
Performing quality control checks throughout the production cycle increases the chance of detecting defective or low-quality items before they become scraps.
Our quality has improved as a result of implementing PlanetTogether's Advanced Planning and Scheduling. The software assigns the best person to the job.
DICK MARX, MATERIALS MANAGER, KNAPHEIDE TRUCK EQUIPMENT
The production of low-quality or faulty goods must be avoided if companies want to maintain a good reputation and a competitive advantage in the market. Strategic management concepts are key for organizations wanting to focus on excellent quality control.
From the design of production processes to setting goals and standards, to monitoring quality at every point in the manufacturing line, the holistic view that these ideas bring ensures that production decisions are made without harming the quality of products. Manufacturing companies in all industries will thrive if they focus their efforts on improving and maintaining products of high quality.
Advanced Planning and Scheduling (APS) Software
Advanced Planning and Scheduling Softwares have become a must for modern-day manufacturing operations as customer demand for increased product assortment, fast delivery, and downward cost pressures become prevalent. These systems help planners save time while providing greater agility in updating ever-changing priorities, production schedules, and inventory plans. APS Systems can be quickly integrated with an ERP/MRP software to fill the gaps where these systems lack planning and scheduling flexibility, accuracy, and efficiency.
With PlanetTogether APS you can:
- Create optimized schedules that balance production efficiency and delivery performance
- Maximize throughput on bottleneck resources to increase revenue
- Synchronize supply with demand to reduce inventories
- Provide company-wide visibility to resource capacity
- Enable scenario data-driven decision making
The implementation of an Advanced Planning and Scheduling (APS) Software will take your manufacturing operations to the next level of production efficiency by taking advantage of the operational data you already possess in your ERP system. APS is a step in the right direction of efficiency and lean manufacturing production enhancement. Try out a free trial or demo!
Related New Features Video
APS Resources