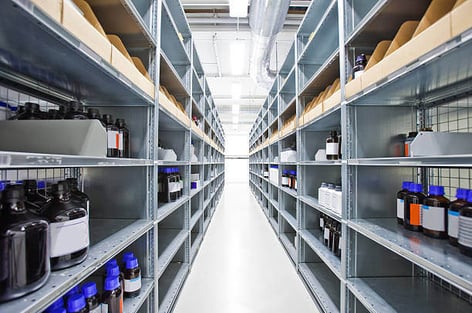
Smart Inventory Moves: Cutting Costs Without Cutting Corners in Chemical Manufacturing
In chemical manufacturing, inventory is more than just raw materials, intermediates, and finished products—it’s tied up capital, shelf-life considerations, regulatory compliance, and fluctuating demand cycles. For Production Planners, managing inventory efficiently isn't just a logistics challenge—it’s a critical lever for cost control and operational agility.
As market pressures intensify, from rising raw material costs to tightening regulatory frameworks and global supply chain disruptions, the need for intelligent inventory strategies has never been greater. In this context, integrating advanced planning and scheduling (APS) tools like PlanetTogether with enterprise systems such as SAP, Oracle, Microsoft Dynamics, Kinaxis, or Aveva can dramatically elevate your inventory management game—unlocking cost efficiencies without compromising service levels or safety.
Let’s look into how Production Planners in chemical manufacturing can achieve smarter, cost-efficient inventory management through technology integration and strategic planning.
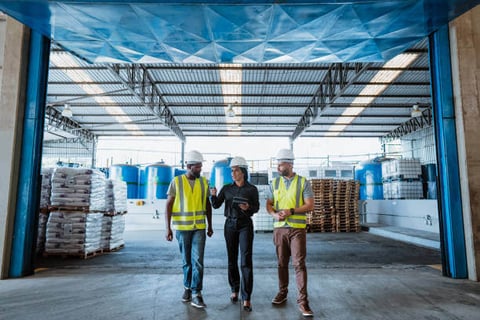
Understanding the Inventory Cost Landscape in Chemical Manufacturing
Before optimizing inventory, it’s essential to understand the cost components involved:
Carrying Costs: This includes warehousing, insurance, depreciation, and obsolescence. In chemical manufacturing, materials may degrade over time, making shelf-life a critical consideration.
Ordering Costs: The administrative and logistical costs associated with placing and receiving orders.
Stockout Costs: Lost sales, production delays, or even penalties resulting from unfulfilled demand due to insufficient inventory.
Production Inefficiencies: Overstocking may lead to batch mixing complexities, while understocking can cause unnecessary equipment idle time.
With narrow margins and complex formulations, chemical manufacturers must carefully balance supply and demand—optimizing inventory to ensure readiness while avoiding excess.
Challenges Production Planners Face in Chemical Inventory Management
Material Shelf Life and Hazard Classification
Many raw materials and finished goods have expiration dates or require special handling (e.g., temperature, containment). Poor planning leads to write-offs or costly rush orders.
Batch Production Complexity
Multi-step, batch-based processes require synchronized raw material availability. Variability in lead times or supplier reliability can disrupt entire production runs.
Regulatory Compliance
Over- or under-stocking certain chemicals can violate storage limits or environmental regulations, leading to fines or operational shutdowns.
Demand Volatility
Customer demand can be unpredictable—especially with contract manufacturing or toll production arrangements. Planners need to stay nimble.
Data Silos and Visibility Gaps
When planning systems aren’t integrated with ERP platforms like SAP or Microsoft Dynamics, it’s difficult to get real-time visibility into inventory levels across the supply chain.
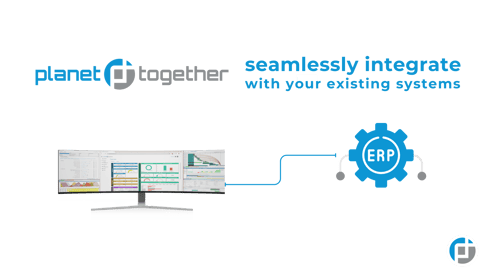
PlanetTogether + ERP Integration: A Game-Changer for Inventory Optimization
To achieve cost-efficient inventory management, real-time visibility and synchronized planning are crucial. This is where integrating PlanetTogether APS with ERP systems makes a transformative impact.
Real-Time Data Exchange
When PlanetTogether is integrated with systems like SAP or Oracle, inventory data—such as on-hand stock, procurement lead times, and safety stock thresholds—are updated continuously. This gives Production Planners access to real-time inventory positions, enabling dynamic adjustments based on actual conditions.
Smarter Scheduling for Reduced Inventory Buffers
Through PlanetTogether’s optimization algorithms, planners can align production schedules with actual demand forecasts and inventory availability. By minimizing gaps between batch processes and streamlining changeovers, safety stock requirements are reduced, freeing up working capital.
Enhanced Forecast Accuracy via Kinaxis or Microsoft Integration
When connected to platforms like Kinaxis RapidResponse or Microsoft Power BI, PlanetTogether can incorporate broader demand signals, such as customer order patterns, market trends, and supplier risks. This improves forecast reliability and reduces the need for conservative overstocking.
Regulatory Traceability with Aveva and Quality Integration
Integration with systems like Aveva (formerly Wonderware) helps maintain batch genealogy, quality specs, and compliance logs. This ensures that inventory management is aligned not just with operational efficiency but also with regulatory traceability and material compatibility.
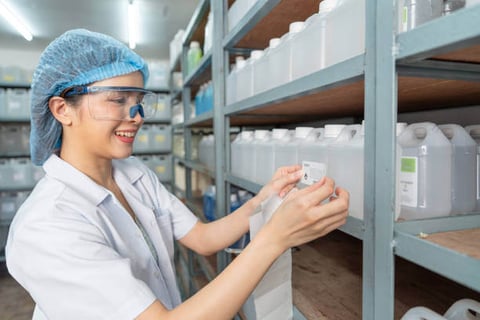
5 Strategies for Cost-Efficient Inventory Management with PlanetTogether
Let’s explore practical strategies Production Planners can implement with the help of PlanetTogether and ERP integration.
1. Move from Static to Dynamic Safety Stocks
Instead of fixed safety stock levels, use PlanetTogether to calculate dynamic safety stock based on forecast variability, lead times, and historical usage. The system can automatically adjust thresholds as demand patterns evolve—reducing both excess inventory and stockout risks.
2. Optimize Production Batches to Minimize Inventory Peaks
Use PlanetTogether’s finite capacity scheduling to align production batch sizes with demand intervals and tank availability. Avoid producing excess inventory just to fill production slots—produce just in time, not just in case.
3. Synchronize Procurement with Production Plans
Through ERP integration, PlanetTogether can generate material requirements planning (MRP) signals that are directly tied to the production schedule. This ensures raw materials are ordered only when needed, reducing inventory holding costs while ensuring availability.
4. Leverage “What-If” Scenarios to Preempt Disruptions
Chemical supply chains are vulnerable to raw material price fluctuations, transportation delays, and regulatory disruptions. PlanetTogether allows planners to simulate “what-if” scenarios—e.g., what happens if a key solvent shipment is delayed? This enables proactive reallocation or rescheduling to prevent costly inventory shortages or excesses.
5. Collaborate Cross-Functionally with Shared Visibility
With ERP-APS integration, teams across procurement, production, quality, and warehousing have a single version of truth. This reduces miscommunication and allows planners to align inventory decisions with broader operational goals, such as capex reduction or service-level improvement.
As a Production Planner in chemical manufacturing, you’re at the intersection of efficiency, safety, and profitability. Managing inventory for cost efficiency isn’t a one-time initiative—it’s a continuous discipline fueled by data and collaboration.
With tools like PlanetTogether APS integrated into your ERP ecosystem, you can finally shift from reactive planning to proactive control—minimizing costs while ensuring that the right materials are available at the right time, in the right quantities.
It’s time to transform inventory from a cost center into a strategic advantage.
LEAVE A COMMENT