Simulation-based Optimization for Batch Production Scheduling
The intricate dance of batch production scheduling demands precision to meet regulatory requirements, ensure product quality, and optimize resource utilization. Traditional methods of scheduling, relying solely on historical data and manual intervention, often fall short in addressing the complexities of modern manufacturing environments.
However, with advancements in technology, particularly in the realm of Manufacturing Execution Systems (MES) and Enterprise Resource Planning (ERP) solutions, a new paradigm emerges – one driven by simulation-based optimization.
In this blog, we'll look into the significance of simulation-based optimization for batch production scheduling in pharmaceutical manufacturing. We'll explore the challenges inherent in traditional scheduling approaches, the benefits of integrating simulation tools like PlanetTogether with leading ERP, SCM, and MES systems such as SAP, Oracle, Microsoft, Kinaxis, and Aveva, and how this integration empowers manufacturers to achieve enhanced efficiency, compliance, and competitiveness.
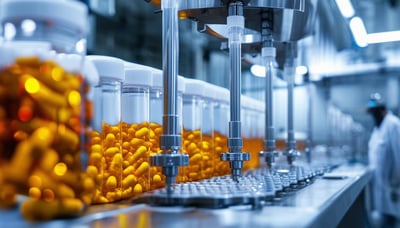
Challenges in Batch Production Scheduling
Pharmaceutical manufacturing presents a unique set of challenges compared to other industries. Batch production scheduling in this sector must adhere to stringent regulatory standards, accommodate varying production volumes, manage complex recipes and formulations, and ensure minimal downtime for equipment maintenance and cleaning. Traditional scheduling methods often rely heavily on heuristic rules, manual input, and static models, which can lead to suboptimal outcomes and inefficiencies.
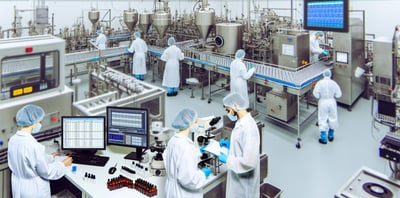
The Need for Simulation-based Optimization
Simulation-based optimization offers a dynamic approach to batch production scheduling by leveraging advanced algorithms and modeling techniques to simulate various production scenarios. By incorporating factors such as equipment constraints, material availability, production priorities, and regulatory requirements, simulation-based optimization enables manufacturers to identify optimal schedules that minimize production costs, reduce lead times, and maximize resource utilization.
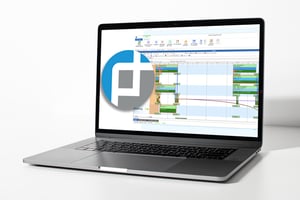
Integration with ERP, SCM, and MES Systems
The seamless integration of simulation tools like PlanetTogether with leading ERP, SCM, and MES systems enhances the efficacy of batch production scheduling in pharmaceutical manufacturing. These systems serve as repositories of real-time data pertaining to inventory levels, production orders, resource availability, and regulatory compliance. By integrating simulation capabilities directly into these systems, manufacturers can leverage the power of predictive analytics and optimization algorithms to generate agile and responsive production schedules.
Benefits of Integration
Enhanced Decision-making: Integration enables manufacturing IT professionals to make informed decisions by providing real-time visibility into production processes, resource utilization, and potential bottlenecks. By simulating different scenarios, stakeholders can assess the impact of various scheduling decisions on key performance metrics such as throughput, cycle time, and equipment utilization.
Improved Compliance: Pharmaceutical manufacturers operate in a highly regulated environment where compliance with Good Manufacturing Practices (GMP) and other regulatory standards is non-negotiable. Integration with ERP and MES systems ensures that scheduling decisions take into account regulatory constraints and compliance requirements, thereby mitigating the risk of non-compliance and associated penalties.
Optimized Resource Utilization: By synchronizing production schedules with resource availability and capacity constraints, integration enables manufacturers to optimize the utilization of equipment, materials, and personnel. This results in reduced idle time, improved throughput, and lower operating costs.
Agility and Flexibility: In today's fast-paced business environment, agility and flexibility are key drivers of competitive advantage. Integration with simulation-based optimization tools allows manufacturers to quickly adapt to changing market demands, production priorities, and supply chain disruptions. By simulating "what-if" scenarios, stakeholders can proactively identify potential issues and devise contingency plans to mitigate risks.
-May-08-2024-04-36-12-8483-PM.png?width=307&height=49&name=logo%20(2)-May-08-2024-04-36-12-8483-PM.png)
Integration of PlanetTogether with SAP ERP
Let's consider a hypothetical scenario where a pharmaceutical manufacturer integrates PlanetTogether, a leading simulation-based optimization tool, with SAP ERP, a widely used enterprise resource planning system. By leveraging this integration, the manufacturer gains the following benefits:
- Real-time synchronization of production schedules with SAP's master data, including material requirements, work orders, and resource capacities.
- Generation of optimized production schedules that minimize changeover times, reduce inventory holding costs, and maximize production efficiency.
- Seamless communication between production planners, operators, and other stakeholders through SAP's collaborative features and reporting capabilities.
- Enhanced visibility into production KPIs, such as OEE (Overall Equipment Effectiveness), yield rates, and adherence to production schedules, through integrated dashboards and analytics tools.
Simulation-based optimization represents a paradigm shift in batch production scheduling for pharmaceutical manufacturing. By integrating advanced simulation tools like PlanetTogether with leading ERP, SCM, and MES systems, manufacturers can achieve unparalleled levels of efficiency, compliance, and agility. By simulating various production scenarios and leveraging real-time data, stakeholders can make informed decisions that drive operational excellence and foster innovation in the pharmaceutical industry.
As we look to the future, the convergence of simulation, optimization, and digital transformation will continue to revolutionize the way pharmaceuticals are manufactured, ensuring safe, reliable, and cost-effective healthcare solutions for patients worldwide.
Are you ready to take your manufacturing operations to the next level? Contact us today to learn more about how PlanetTogether and integrated scheduling solutions can help you achieve your sustainability goals and drive success in the pharmaceutical industry.