Scheduling in Unpredictable Environments with Dynamic Demand and Seasonal Variations
As a Plant Manager in the Food and Beverage manufacturing industry, you're conscious of the challenges that come with ensuring efficient production while dealing with unpredictable demand patterns and seasonal variations. In today's fast-paced business environment, the ability to adapt quickly to changing circumstances can make or break your success. This is where effective scheduling becomes a crucial element in optimizing your operations.
In this blog, we'll explore how you can tackle scheduling in unpredictable environments with dynamic demand and seasonal variations, with a focus on integrating scheduling solutions like PlanetTogether with popular ERP, SCM, and MES systems such as SAP, Oracle, Microsoft, Kinaxis, Aveva, and others.
Unpredictable Environments
Manufacturing in the Food and Beverage industry can be a daunting task when you have to deal with unpredictable fluctuations in demand. Seasonal variations, market trends, unforeseen disruptions, and changes in consumer preferences all contribute to the complexity of your production schedules. To stay competitive and meet customer expectations, you need to be agile and responsive to these dynamic challenges.
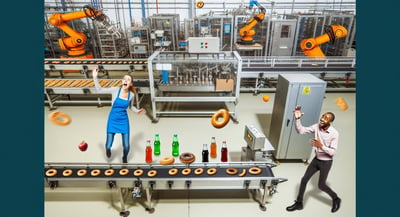
The Role of Scheduling
Effective scheduling is the linchpin of managing unpredictable environments. It's the process of allocating resources, including equipment, labor, and materials, to specific tasks and production orders to ensure that everything runs smoothly and efficiently. In an industry as dynamic as Food and Beverage manufacturing, scheduling plays a critical role in achieving:
Improved Efficiency: Efficient scheduling minimizes downtime, reduces idle resources, and maximizes equipment utilization, leading to cost savings and increased productivity.
Meeting Customer Demands: Timely delivery and product availability are crucial in satisfying customer demands, which is essential in this highly competitive industry.
Adaptability: A robust scheduling system allows you to respond quickly to changes in demand, whether due to seasonality or unforeseen events.
Reduced Inventory Costs: Efficient scheduling minimizes the need for excess inventory, helping you save on storage and holding costs.
Enhanced Resource Allocation: Optimized scheduling ensures that your resources are allocated efficiently, reducing overtime and labor costs.
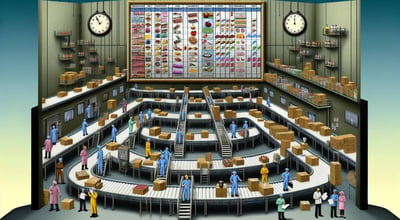
Challenges in Scheduling for Food and Beverage Manufacturing
Scheduling in the Food and Beverage industry presents its own set of unique challenges:
Seasonal Variations: Many products in this industry have seasonal demand spikes, making it essential to plan for variations in production capacity.
Short Shelf Life: Perishable goods require precise scheduling to minimize waste and ensure that products reach consumers in their freshest state.
Recipe Changes: Frequent recipe changes to accommodate new product lines or variations add complexity to scheduling.
Compliance and Quality Control: Stringent regulations and quality control measures necessitate scheduling that ensures compliance and traceability.
Supply Chain Complexity: Managing the complex supply chain for ingredients and packaging materials requires efficient scheduling to avoid disruptions.
Equipment Maintenance: Regular equipment maintenance and downtime need to be factored into the schedule without impacting production targets.

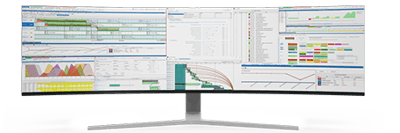
PlanetTogether: A Powerful Scheduling Solution
To address these challenges effectively, many Food and Beverage manufacturers are turning to advanced scheduling solutions like PlanetTogether. PlanetTogether is a robust production planning and scheduling software that offers a wide range of features to help optimize your operations. One of its key strengths is its ability to integrate seamlessly with various ERP, SCM, and MES systems commonly used in the industry, such as SAP, Oracle, Microsoft, Kinaxis, Aveva, and more.
Integration Benefits
Integrating PlanetTogether with your existing systems offers several significant advantages:
Real-time Data Exchange: Integrating your scheduling software with ERP, SCM, and MES systems allows for real-time data exchange. This means that your production schedule can be constantly updated with the latest information on orders, inventory levels, and resource availability.
Enhanced Visibility: Integration provides a comprehensive view of your operations, allowing you to monitor and manage all aspects of production, from order processing and inventory management to equipment maintenance.
Improved Accuracy: Automated data transfer reduces the risk of manual errors and ensures that scheduling decisions are based on accurate, up-to-date information.
Streamlined Communication: Integration facilitates seamless communication between different departments, reducing miscommunication and improving collaboration.
Faster Decision-Making: With real-time data, you can make quick decisions to adjust production schedules in response to changing demand or unforeseen disruptions.
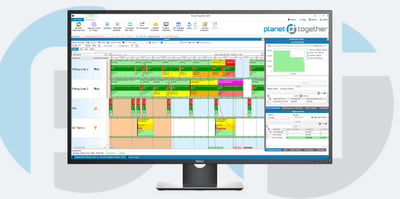
How PlanetTogether Enhances Scheduling
Now, let's look into how PlanetTogether's features can help you tackle scheduling challenges in unpredictable environments:
Forecasting and Demand Planning: PlanetTogether's advanced forecasting tools allow you to predict demand more accurately, even in volatile markets. By analyzing historical data and market trends, you can make informed decisions about production levels and resource allocation.
Seasonal Variation Management: The software can accommodate seasonal variations in demand by automatically adjusting production schedules, staffing levels, and inventory levels to meet fluctuating requirements.
Production Optimization: PlanetTogether uses sophisticated algorithms to optimize production schedules, taking into account constraints like equipment availability, labor shifts, and inventory levels. This ensures that resources are utilized efficiently while meeting production targets.
Recipe Management: Managing multiple recipes and formulations is made easier with PlanetTogether. You can create and schedule production orders for different product variations with ease.
Compliance and Traceability: The software helps you maintain compliance with industry regulations by tracking the origin of ingredients and ensuring that quality control measures are implemented at every stage of production.
Resource Allocation: PlanetTogether's resource allocation capabilities allow you to assign the right equipment and labor to each task, minimizing idle time and overtime costs.
Equipment Maintenance Scheduling: Preventive maintenance schedules can be incorporated into production plans to minimize unplanned downtime and equipment failures.
What-If Scenarios: The software enables you to simulate different production scenarios, helping you make informed decisions when facing unexpected challenges.
In the Food and Beverage manufacturing industry, scheduling in unpredictable environments with dynamic demand and seasonal variations is a challenging but essential task. Effective scheduling not only improves efficiency and resource utilization but also helps you meet customer demands and maintain a competitive edge. Integrating advanced scheduling solutions like PlanetTogether with your ERP, SCM, and MES systems can significantly enhance your ability to manage these challenges.
By leveraging PlanetTogether's features, including forecasting, production optimization, recipe management, and real-time data exchange, you can overcome the unique challenges of your industry.
As a Plant Manager, your ability to adapt to unpredictable circumstances and make data-driven decisions is essential. Integration between scheduling solutions and existing systems is the path to achieving operational excellence, reducing costs, and ensuring customer satisfaction in the ever-changing Food and Beverage manufacturing landscape.
Are you ready to take your manufacturing operations to the next level? Contact us today to learn more about how PlanetTogether can help you achieve your goals and drive success in your industry.
LEAVE A COMMENT