Product and Process Standardization
Achieving operational efficiency is a constant pursuit in pharmaceutical manufacturing. One of the critical aspects influencing efficiency is scheduling. Efficient scheduling not only ensures timely delivery of pharmaceutical products but also plays a vital role in maintaining product and process standardization.
In this blog, we will look into the significance of scheduling for product and process standardization in pharmaceutical manufacturing, and how integration between advanced scheduling software like PlanetTogether and leading ERP, SCM, and MES systems can revolutionize operations.
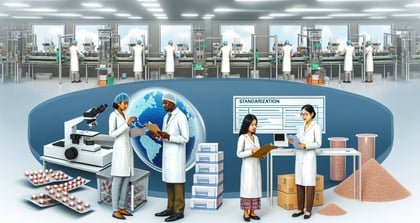
The Importance of Standardization
Product and process standardization is the cornerstone of quality assurance in pharmaceutical manufacturing. It involves establishing consistent procedures, specifications, and protocols to ensure uniformity and reliability across all stages of production. Standardization not only enhances product quality but also streamlines operations, reduces errors, and facilitates compliance with regulatory requirements such as Good Manufacturing Practices (GMP).
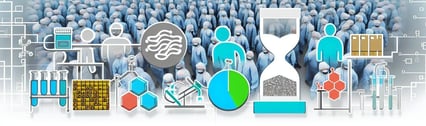
Challenges in Achieving Standardization
Despite its benefits, achieving standardization in pharmaceutical manufacturing comes with its set of challenges. These challenges include:
Complexity of Operations: Pharmaceutical manufacturing involves intricate processes with numerous variables, including raw material availability, equipment utilization, and regulatory compliance. Coordinating these variables to maintain standardization can be daunting without proper scheduling.
Regulatory Compliance: The pharmaceutical industry is subject to stringent regulatory standards enforced by agencies like the FDA. Compliance with these standards requires meticulous documentation, traceability, and adherence to predefined processes, all of which rely heavily on standardized scheduling practices.
Resource Optimization: Efficient utilization of resources, including manpower, equipment, and raw materials, is essential for maintaining consistency in product quality and process efficiency. Inadequate scheduling can lead to underutilization or overutilization of resources, resulting in inefficiencies and deviations from standard processes.
-Apr-01-2024-01-39-55-8668-PM.png?width=300&height=48&name=logo%20(2)-Apr-01-2024-01-39-55-8668-PM.png)
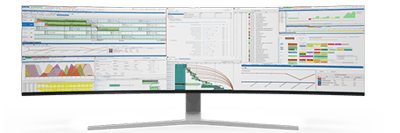
Scheduling for Standardization
Effective scheduling is the linchpin for achieving product and process standardization in pharmaceutical manufacturing. By leveraging advanced scheduling software like PlanetTogether, production schedulers can optimize schedules based on various parameters such as:
Production Capacity: PlanetTogether enables schedulers to optimize production schedules based on available capacity, ensuring that production levels align with demand while maintaining standardization.
Material Availability: Integration with ERP systems like SAP, Oracle, or Microsoft allows PlanetTogether to synchronize production schedules with real-time inventory data, ensuring that raw materials are available when needed, thus minimizing disruptions and deviations from standard processes.
Equipment Utilization: PlanetTogether facilitates optimal utilization of manufacturing equipment by scheduling production runs based on equipment availability and efficiency, thereby minimizing downtime and ensuring consistent product quality.
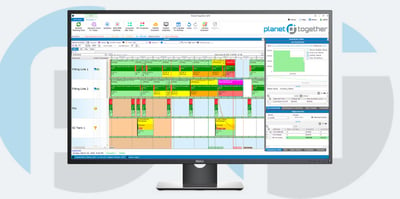
Integration with ERP, SCM, and MES Systems
The seamless integration between advanced scheduling software like PlanetTogether and leading ERP, SCM, and MES systems enhances the effectiveness of scheduling for product and process standardization in pharmaceutical manufacturing. Here's how integration with these systems adds value:
ERP Integration: Integration with ERP systems provides real-time visibility into inventory levels, production orders, and resource availability, allowing schedulers to make informed decisions and adjust schedules accordingly to maintain standardization.
SCM Integration: Integration with SCM systems enables efficient management of the supply chain, ensuring timely delivery of raw materials and components, thus minimizing disruptions and deviations from standard processes.
MES Integration: Integration with MES systems facilitates data exchange between production scheduling and shop floor operations, ensuring seamless execution of production plans and adherence to standard processes.
In the highly regulated and competitive landscape of pharmaceutical manufacturing, achieving product and process standardization is imperative for ensuring product quality, operational efficiency, and regulatory compliance. Effective scheduling plays a pivotal role in achieving this standardization by optimizing production schedules based on various parameters such as capacity, material availability, and equipment utilization.
Integration between advanced scheduling software like PlanetTogether and leading ERP, SCM, and MES systems further enhances the effectiveness of scheduling by providing real-time visibility, seamless data exchange, and improved decision-making capabilities.
By embracing scheduling for product and process standardization, pharmaceutical manufacturers can unlock new levels of efficiency, reliability, and compliance in their operations, ultimately driving growth and success in the industry. Are you ready to take your manufacturing operations to the next level? Contact us today to learn more about how PlanetTogether can help you achieve your goals and drive success in your industry.
LEAVE A COMMENT