Scheduling for Pharmaceutical Manufacturing
In the rigorously controlled world of pharmaceutical manufacturing, efficient scheduling is not just a requirement but a necessity. As an Operations Director, you're already familiar with the complexities of managing a pharmaceutical production line: from regulatory compliance and quality control to demand forecasting and inventory management.
However, one of the most challenging aspects of your role involves the integration of advanced scheduling systems like PlanetTogether with various Enterprise Resource Planning (ERP), Supply Chain Management (SCM), and Manufacturing Execution Systems (MES). This integration is crucial for enhancing production efficiency and ensuring that your facility can meet its production targets and maintain compliance with health regulations.
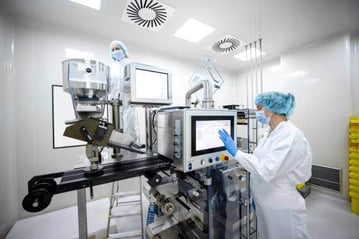
Understanding the Importance of Integrated Scheduling Systems
Integrated scheduling systems are at the heart of efficient pharmaceutical manufacturing operations. They provide a holistic view of the manufacturing process, enabling you to optimize production schedules, reduce downtime, and respond quickly to market demands or changes in production capacity.
PlanetTogether is a prime example of an advanced planning and scheduling (APS) system that is designed to work in harmony with various ERP, SCM, and MES platforms. By integrating PlanetTogether with systems like SAP, Oracle, Microsoft Dynamics, Kinaxis, Aveva, and others, pharmaceutical manufacturers can achieve a seamless flow of information across all operational levels. This integration allows for real-time data analysis, improved decision-making, and enhanced operational efficiency.
-Apr-01-2024-01-39-55-8668-PM.png?width=300&height=48&name=logo%20(2)-Apr-01-2024-01-39-55-8668-PM.png)
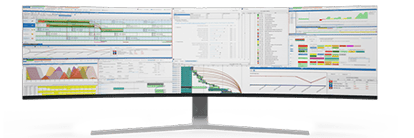
Key Benefits of Integrating PlanetTogether with ERP, SCM, and MES
Enhanced Data Visibility and Accuracy
Integrating PlanetTogether with ERP systems like SAP or Oracle ensures that scheduling decisions are based on accurate and up-to-date information. This integration allows for real-time updates from various departments, such as procurement, logistics, and production, which is essential for maintaining a streamlined operation and minimizing the risk of delays or errors due to outdated data.
Improved Production Efficiency
By leveraging the sophisticated scheduling algorithms of PlanetTogether, operations directors can optimize production lines for maximum efficiency. This means scheduling machinery and resources in a way that minimizes idle time and reduces bottlenecks. For instance, integration with MES systems like Aveva can provide detailed insights into machine performance and maintenance schedules, allowing for predictive maintenance and less unexpected downtime.
Better Compliance and Quality Control
The pharmaceutical industry is governed by stringent regulations that demand high standards of quality and traceability. Integrating PlanetTogether with systems like Kinaxis or Microsoft Dynamics can help ensure that all aspects of production are compliant with regulatory standards. This integration facilitates better quality control by synchronizing batch production records and quality checks, which are critical for maintaining product integrity and safety.
Enhanced Responsiveness to Market Changes
The ability to quickly adapt to changes in market demand is crucial for maintaining competitiveness in the pharmaceutical industry. Integrated scheduling systems enable faster response times by allowing operations directors to adjust production schedules promptly based on insights gained from SCM systems like SAP or Oracle SCM Cloud. This agility ensures that pharmaceutical manufacturers can meet demand spikes without compromising on quality.
Streamlined Inventory Management
Effective inventory management is crucial to prevent overstocking or stockouts of crucial materials. By integrating PlanetTogether with ERP systems, manufacturers can have a more accurate forecast of required materials, manage procurement schedules more efficiently, and reduce costs associated with excess inventory or emergency procurement.
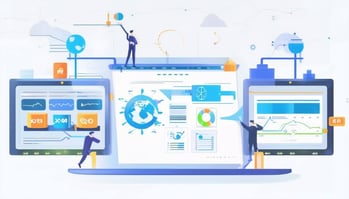
Implementing Integration: Best Practices
To reap the full benefits of integrating PlanetTogether with ERP, SCM, and MES systems, follow these best practices:
Ensure Data Compatibility
Before integration, ensure that data formats and protocols are compatible between PlanetTogether and the existing systems like SAP, Oracle, or Microsoft. This may involve some initial setup and customization to facilitate smooth data exchange.
Regular Training and Updates
As systems and processes evolve, regular training for staff on the latest functionalities of the integrated systems is essential. Keeping your team updated ensures that they are capable of leveraging the tools effectively to improve production schedules and operational efficiency.
Continuous Monitoring and Optimization
After integration, continuously monitor the performance of the scheduling systems. Regularly assess the impact of the integration on production efficiency, compliance, and responsiveness to changes. Use these insights to further optimize the scheduling and overall operational processes.
Integrating advanced scheduling systems like PlanetTogether with ERP, SCM, and MES platforms is a game-changer for pharmaceutical manufacturing. It not only enhances operational efficiency and compliance but also provides the agility to respond swiftly to market demands.
As an Operations Director, steering your facility through this integration will position your operations at the forefront of technological advancements, ensuring sustained growth and success in the competitive pharmaceutical industry.
By embracing these integrated solutions, you are not just optimizing your production processes but also setting up your facility to thrive in the dynamic landscape of pharmaceutical manufacturing. Are you ready to take your manufacturing operations to the next level? Contact us today to learn more about how PlanetTogether can help you achieve your goals and drive success in your industry.