Scheduling High-Tech Cleanroom Manufacturing
As a plant manager in a medical manufacturing facility, you understand the critical role that scheduling plays in ensuring the efficiency, productivity, and compliance of your operations. In the high-stakes world of medical manufacturing, where precision, quality, and cleanliness are paramount, effective scheduling becomes even more crucial. This is particularly true in cleanroom environments, where any disruption or delay can have serious consequences for product quality and patient safety.
In this blog post, we'll explore the unique challenges faced by plant managers in high-tech cleanroom manufacturing facilities and discuss how advanced scheduling solutions, such as PlanetTogether, integrated with ERP, SCM, and MES systems like SAP, Oracle, Microsoft, Kinaxis, and Aveva, can help overcome these challenges and optimize production processes.
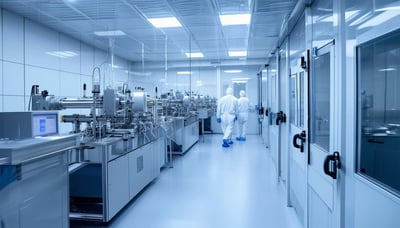
High-Tech Cleanroom Manufacturing
High-tech cleanroom manufacturing in the medical industry presents a myriad of challenges that demand meticulous planning and execution. These challenges include:
Stringent Regulatory Requirements: Medical manufacturing facilities must adhere to strict regulatory standards, such as those set forth by the FDA, ISO, and other regulatory bodies. Compliance with these standards is non-negotiable and requires careful scheduling to ensure that all processes meet regulatory requirements.
Complex Workflows: Cleanroom manufacturing involves intricate workflows that often require precise sequencing and coordination of tasks. From material preparation and sterilization to assembly and packaging, each step in the production process must be carefully orchestrated to minimize contamination and ensure product integrity.
Limited Resources: Cleanroom environments are resource-intensive and require specialized equipment, facilities, and personnel. Maximizing the utilization of these resources while minimizing downtime is essential for optimizing efficiency and reducing production costs.
Tight Production Schedules: In the fast-paced world of medical manufacturing, time is of the essence. Production schedules are often tight, with little room for error or delay. Any disruptions to the schedule can have ripple effects throughout the production process, leading to delays, missed deadlines, and increased costs.
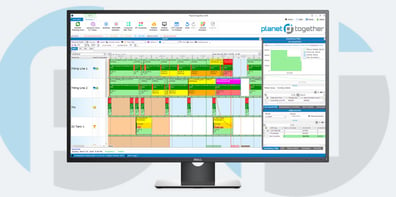
The Role of Advanced Scheduling Solutions
To address these challenges and optimize production processes in high-tech cleanroom manufacturing facilities, plant managers can leverage advanced scheduling solutions like PlanetTogether. These software solutions offer a range of features and capabilities designed to streamline scheduling, improve efficiency, and ensure compliance.
When integrated with ERP, SCM, and MES systems such as SAP, Oracle, Microsoft, Kinaxis, and Aveva, these scheduling solutions become even more powerful, providing seamless data exchange and real-time visibility into production operations.
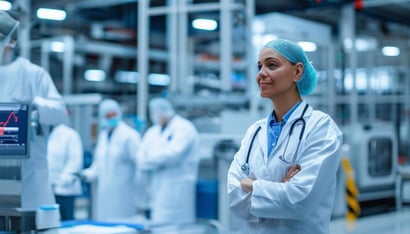
Key Benefits of Advanced Scheduling Solutions
Optimized Production Planning: Advanced scheduling solutions use sophisticated algorithms to generate optimized production schedules based on factors such as resource availability, production capacity, and customer demand. By automatically generating schedules that maximize efficiency and minimize downtime, these solutions help plant managers make better-informed decisions and improve overall productivity.
Real-Time Monitoring and Tracking: Integrated scheduling solutions provide real-time visibility into production operations, allowing plant managers to monitor progress, track Key Performance Indicators (KPIs), and identify potential bottlenecks or issues before they escalate. This level of visibility enables proactive decision-making and helps ensure that production stays on track.
Enhanced Collaboration and Communication: By centralizing scheduling data and facilitating communication across departments, advanced scheduling solutions foster collaboration and alignment among stakeholders. Plant managers can easily share schedules, allocate resources, and communicate changes in real-time, ensuring that everyone is on the same page and working towards common goals.
Improved Compliance and Quality Assurance: With built-in compliance features and audit trails, advanced scheduling solutions help ensure that production processes adhere to regulatory standards and quality requirements. By automating documentation and record-keeping tasks, these solutions simplify compliance efforts and reduce the risk of non-compliance penalties.
Dynamic What-If Analysis: Advanced scheduling solutions enable plant managers to perform dynamic what-if analysis to evaluate the impact of different scenarios on production schedules. Whether simulating changes in demand, resource availability, or production constraints, these solutions empower plant managers to make informed decisions and optimize scheduling strategies accordingly.
-Apr-01-2024-01-39-55-8668-PM.png?width=300&height=48&name=logo%20(2)-Apr-01-2024-01-39-55-8668-PM.png)
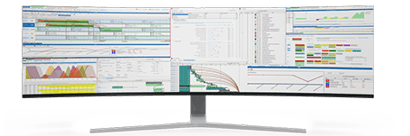
Optimizing Cleanroom Manufacturing with PlanetTogether Integration
By implementing PlanetTogether's advanced scheduling solution and integrating it with their existing ERP, SCM, and MES systems, the plant manager is able to achieve significant improvements in efficiency and productivity.
Streamlined Production Planning: PlanetTogether analyzes production data from the ERP system, such as customer orders, inventory levels, and production capacities, to generate optimized production schedules that minimize downtime and maximize throughput.
Real-Time Visibility and Monitoring: Integrated with MES systems, PlanetTogether provides real-time visibility into cleanroom operations, allowing the plant manager to monitor equipment status, track production progress, and identify potential issues in real-time.
Enhanced Collaboration and Communication: By integrating with collaboration tools like Microsoft Teams or Slack, PlanetTogether facilitates seamless communication and collaboration among production teams, enabling them to quickly respond to changes and coordinate tasks more effectively.
Improved Compliance and Quality Assurance: PlanetTogether's built-in compliance features ensure that production schedules adhere to regulatory standards and quality requirements. Automated documentation and record-keeping help streamline compliance efforts and minimize the risk of non-compliance penalties.
Dynamic What-If Analysis: PlanetTogether's what-if analysis capabilities enable the plant manager to simulate different scenarios and evaluate their impact on production schedules. By exploring various options and contingencies, the plant manager can make more informed decisions and optimize scheduling strategies to maximize efficiency and minimize risk.
In the world of high-tech cleanroom manufacturing in the medical industry, effective scheduling is essential for optimizing efficiency, ensuring compliance, and maintaining product quality. By leveraging advanced scheduling solutions like PlanetTogether and integrating them with ERP, SCM, and MES systems, plant managers can overcome the unique challenges of cleanroom manufacturing and achieve significant improvements in productivity, efficiency, and compliance.
By streamlining production planning, providing real-time visibility into operations, fostering collaboration and communication, ensuring compliance and quality assurance, and enabling dynamic what-if analysis, integrated scheduling solutions empower plant managers to make better-informed decisions and drive continuous improvement in their manufacturing operations.
Are you ready to take your manufacturing operations to the next level? Contact us today to learn more about how PlanetTogether can help you achieve your goals and drive success in your industry.