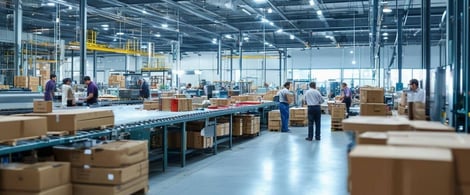
Scheduling for Customizable Products in Consumer Goods Manufacturing
In consumer goods manufacturing, packaging is no longer just about functionality. Today’s consumers expect personalized, aesthetically pleasing, and sustainable packaging. For plant managers in packaging manufacturing facilities, meeting these demands while maintaining efficiency and profitability is a significant challenge. The ability to schedule production effectively, especially for customizable products, is critical.
This is where advanced scheduling tools like PlanetTogether, integrated with ERP systems such as SAP, Oracle, Microsoft, Kinaxis, or Aveva, can transform operations.
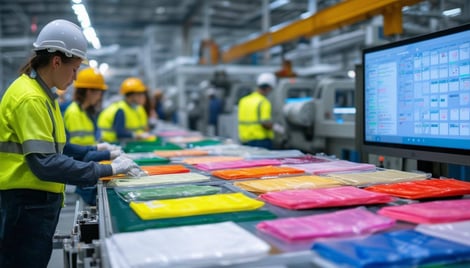
The Challenge of Customizable Products
Consumer goods manufacturers are increasingly offering customizable products to meet the demands of diverse markets and individual preferences. Whether it’s personalized branding, unique package sizes, or environmentally friendly materials, these requirements add complexity to production processes. Traditional scheduling methods often fall short when managing these intricacies, leading to:
Extended Lead Times: Frequent adjustments and smaller production runs can disrupt workflows, delaying order fulfillment.
Increased Waste: Inefficient changeovers and poor material planning result in wasted resources.
Higher Costs: Last-minute changes or errors often necessitate overtime or expedited shipping, driving up expenses.
Lower Flexibility: Without a responsive scheduling system, adapting to changes becomes a cumbersome task.
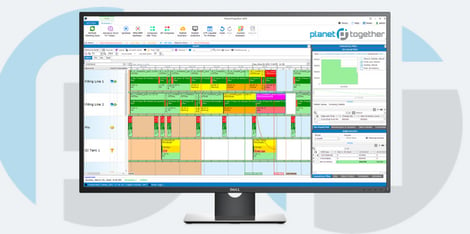
Integrating PlanetTogether with ERP Systems
Integrating advanced scheduling software like PlanetTogether with ERP systems addresses these challenges head-on. By leveraging real-time data and sophisticated algorithms, these solutions provide plant managers with the tools to optimize production schedules, reduce waste, and meet customer demands efficiently.
Key Benefits of Advanced Scheduling for Customizable Products
Enhanced Visibility
Integration between PlanetTogether and ERP systems like SAP or Oracle ensures seamless data flow across the organization. This real-time visibility allows plant managers to track order statuses, inventory levels, and machine availability, enabling proactive decision-making.
Improved Flexibility
Advanced scheduling tools can quickly adapt to changing demands or unforeseen disruptions. For example, if a customer requests a last-minute change to packaging design, the system can adjust the schedule and reallocate resources with minimal disruption.
Reduced Changeover Times
Optimized sequencing minimizes downtime between production runs. PlanetTogether’s integration with manufacturing execution systems (MES) ensures that machine settings and materials are prepped ahead of time, further reducing delays.
Sustainability
By optimizing material usage and reducing waste, advanced scheduling aligns with sustainability goals—a critical factor in today’s consumer goods market. Integration with Aveva’s sustainability solutions can further enhance environmental performance.
Cost Efficiency
Efficient scheduling reduces overtime, minimizes inventory holding costs, and avoids penalties for delayed deliveries. With Kinaxis’ supply chain planning integration, demand forecasting becomes more accurate, leading to better resource allocation.
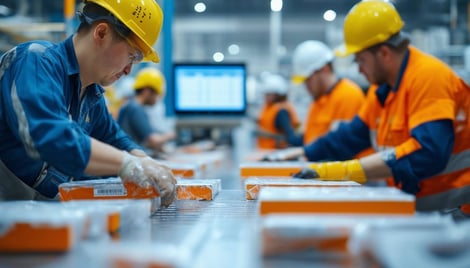
Steps to Implement Advanced Scheduling in Your Facility
If your packaging facility is struggling to meet the demands of customizable products, implementing an advanced scheduling system can drive significant improvements. Here’s how to get started:
Assess Current Processes
Identify bottlenecks, inefficiencies, and areas where flexibility is lacking. Analyze the impact of these issues on lead times, costs, and customer satisfaction.
Select the Right Tools
Choose scheduling software that integrates seamlessly with your existing ERP system. For example, PlanetTogether’s compatibility with SAP, Oracle, Microsoft, and Kinaxis ensures a smooth transition.
Train Your Team
Provide comprehensive training for your staff to ensure they can fully utilize the system’s capabilities. Focus on real-time monitoring, schedule adjustments, and data analysis.
Pilot and Scale
Start with a pilot project to test the system’s effectiveness. Use the insights gained to refine processes before scaling up across the facility.
Monitor and Optimize
Continuously monitor performance metrics, such as on-time delivery rates, changeover times, and waste levels. Use these insights to fine-tune the system and address emerging challenges.
Scheduling for customizable products in consumer goods manufacturing is a complex yet rewarding endeavor. With the right tools and strategies, plant managers in packaging manufacturing facilities can turn challenges into opportunities. The integration of advanced scheduling software like PlanetTogether with ERP systems such as SAP, Oracle, Microsoft, Kinaxis, or Aveva is not just a technical upgrade—it’s a strategic investment in your facility’s future.
By adopting these solutions, you’re not only improving operational efficiency but also setting the stage for long-term success in a competitive market. Whether you’re managing last-minute design changes or optimizing resource allocation, advanced scheduling can be the key to unlocking your facility’s full potential.
Are you ready to take your manufacturing operations to the next level? Contact us today to learn more about how PlanetTogether can help you achieve your goals and drive success in your industry.