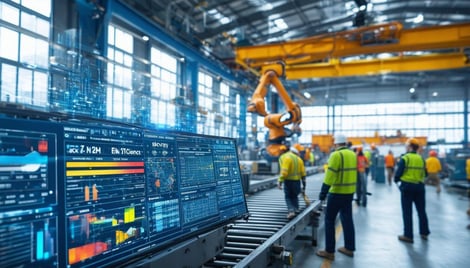
Root Cause Analysis for Scheduling Failures in Industrial Manufacturing
Effective production scheduling is at the heart of industrial manufacturing. It ensures that resources are allocated efficiently, deadlines are met, and costs are controlled. Yet, even with advanced tools and meticulous planning, scheduling failures can still disrupt operations, leading to missed deadlines, increased costs, and customer dissatisfaction.
Root Cause Analysis (RCA) is a critical approach to identify the underlying reasons behind these failures. When integrated with advanced scheduling platforms like PlanetTogether and enterprise systems such as SAP, Oracle, Microsoft, Kinaxis, or Aveva, RCA becomes even more powerful
This blog explores how production planners in industrial manufacturing facilities can leverage RCA to address scheduling failures and improve operational outcomes.
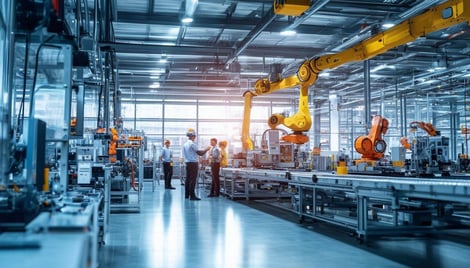
The Importance of Root Cause Analysis in Scheduling
Scheduling failures are often symptoms of deeper systemic issues. Without addressing these root causes, planners risk facing recurring disruptions. RCA offers a structured methodology to drill down into the factors contributing to a problem, ensuring sustainable solutions.
Common Scheduling Challenges in Industrial Manufacturing:
Resource Constraints: Limited availability of equipment, materials, or labor.
Data Silos: Disconnected systems leading to misaligned planning.
Unforeseen Changes: Sudden demand spikes or supply chain disruptions.
Inaccurate Forecasting: Over- or underestimating production requirements.
System Inefficiencies: Software or integration issues between scheduling and ERP systems.
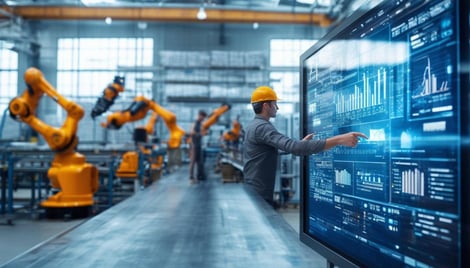
Steps for Effective Root Cause Analysis
Define the Problem: Begin by clearly articulating the scheduling failure. For instance, "Production of Item A delayed by 24 hours due to resource unavailability."
Gather Data: Collect relevant data from scheduling platforms like PlanetTogether and ERP systems such as SAP or Oracle. Integration between these systems enables seamless data flow, offering a holistic view of operations.
Identify Possible Causes: Use brainstorming techniques, historical data, and advanced analytics. Tools like PlanetTogether, integrated with Kinaxis or Aveva, provide predictive insights, helping planners identify potential bottlenecks.
Analyze Causes: Employ techniques like the "5 Whys" or Fishbone Diagrams to look deeper into the issue. For instance:
Why was Item A delayed? Lack of materials.
Why were materials unavailable? Supplier delay.
Why was the supplier delayed? Forecast error in replenishment schedule.
Implement Solutions: Address the root cause by enhancing system processes or resource planning. Integrated systems like PlanetTogether and Microsoft Dynamics can automate adjustments, ensuring real-time updates across the supply chain.
Monitor Outcomes: Evaluate the effectiveness of the implemented solutions. Continuous feedback loops between PlanetTogether and your ERP system enable real-time performance monitoring and adjustments.

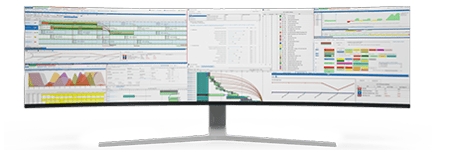
Leveraging System Integrations for RCA
Advanced scheduling platforms like PlanetTogether are designed to integrate seamlessly with leading enterprise systems. These integrations offer unparalleled advantages for RCA, including:
Data Centralization: Integration ensures data from production schedules, inventory, and sales forecasts are consolidated, reducing silos and improving visibility.
Enhanced Analytics: Combined with SAP or Oracle, PlanetTogether provides detailed analytics, helping planners predict and prevent potential failures.
Real-Time Updates: With integrations to platforms like Microsoft Dynamics, planners receive instant notifications of schedule changes, enabling proactive adjustments.
Scenario Planning: Tools like Kinaxis allow planners to simulate various scenarios, identifying potential issues and their root causes before they occur.
Best Practices for Production Planners
To effectively use RCA for scheduling failures, production planners should:
Invest in Integrated Systems: Ensure your scheduling platform is integrated with ERP and SCM systems like Oracle or Kinaxis for seamless data flow.
Adopt Predictive Analytics: Leverage tools like PlanetTogether for real-time and predictive insights into potential scheduling disruptions.
Promote Cross-Department Collaboration: Engage stakeholders from procurement, maintenance, and supply chain to ensure comprehensive data collection and analysis.
Embrace Continuous Improvement: Use RCA findings to refine processes, workflows, and system integrations continually.
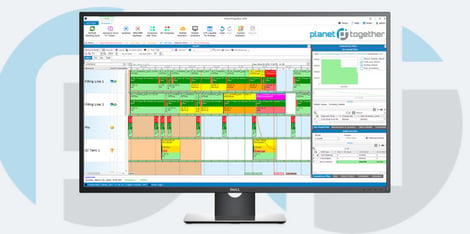
The Role of PlanetTogether and System Integrations
PlanetTogether’s advanced scheduling capabilities, combined with ERP systems such as SAP or Microsoft Dynamics, provide a robust framework for RCA. These integrations enable:
Visibility: Real-time dashboards offering insights into production schedules, inventory levels, and capacity constraints.
Automation: Automated adjustments to schedules based on changing priorities or resource availability.
Collaboration: Shared data across systems fosters better communication between departments, ensuring aligned decision-making.
Scheduling failures in industrial manufacturing facilities can be costly, but with a systematic approach like Root Cause Analysis, production planners can identify and address the underlying issues effectively. Integrating advanced scheduling tools like PlanetTogether with enterprise systems such as SAP, Oracle, Microsoft, Kinaxis, or Aveva further enhances the RCA process, providing the data and insights needed for proactive decision-making.
By embracing these practices, production planners can ensure smoother operations, improved resource utilization, and enhanced customer satisfaction. Are you ready to take your manufacturing operations to the next level? Contact us today to learn more about how PlanetTogether can help you achieve your goals and drive success in your industry.