Risk Management and Quality Assurance
Production Planners in chemical manufacturing are often the first line of defense in ensuring that operations align with stringent quality and risk management standards. As the demand for chemical products grows, so does the complexity of maintaining quality while minimizing risk. To tackle these challenges, Production Planners must adopt advanced planning strategies and integrate powerful digital tools such as PlanetTogether with enterprise systems like SAP, Oracle, Microsoft, Kinaxis, or Aveva.
This integration can drive unprecedented control and visibility across operations, supporting a balanced approach to quality assurance and risk mitigation.
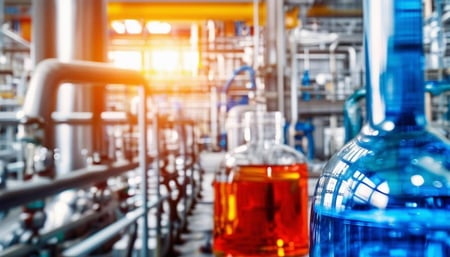
Risk Management in Chemical Manufacturing
Chemical manufacturing is uniquely prone to risks due to the hazardous nature of raw materials, the need for precise processes, and the strict regulatory environment. Any lapses in quality or safety can have serious repercussions, from environmental hazards to regulatory penalties and potential loss of market credibility. In this context, risk management isn’t just about avoiding disasters; it’s about proactively identifying and mitigating potential issues before they escalate.
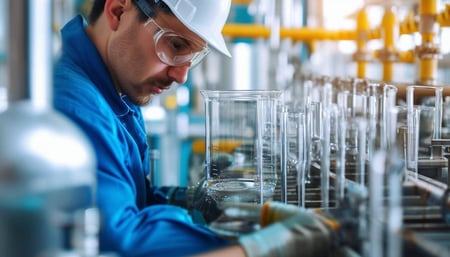
Key Risk Areas in Production Planning
For Production Planners, effective risk management begins with understanding the areas most prone to risks within the production process. These areas include:
Material Variability: The quality and stability of raw materials can vary, impacting the final product’s quality.
Process Consistency: Ensuring uniformity in production processes is crucial for quality assurance, especially in multi-step chemical processes.
Compliance: Adherence to stringent safety and environmental standards is mandatory. Non-compliance risks costly fines and legal repercussions.
Supply Chain Reliability: A disruption in the supply of critical raw materials can halt production, impacting both revenue and reputation.
Identifying and monitoring these risks is essential to proactively prevent quality issues. By utilizing tools like PlanetTogether and integrating it with other enterprise systems, Production Planners can develop a systematic, data-driven approach to managing these risks effectively.
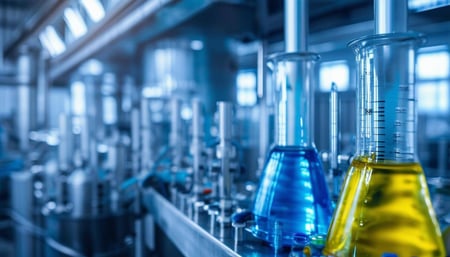
Quality Assurance as a Core Element of Risk Management
In chemical manufacturing, quality assurance (QA) isn’t just about final product checks; it permeates every stage of the production process. QA is central to risk management, as it establishes the benchmarks needed to ensure each product meets quality and regulatory standards.
Key components of an effective QA program include:
Real-time Quality Monitoring: Continuously tracking quality metrics during production can help identify deviations early.
Standard Operating Procedures (SOPs): Strict adherence to SOPs for each process step minimizes variability and maintains quality.
Data Analytics: Leveraging data from integrated systems like SAP, Oracle, and Microsoft can help analyze trends and detect patterns in quality metrics, allowing for predictive quality adjustments.
Feedback Loops: A continuous improvement loop that uses data from past production cycles enables proactive adjustments and long-term quality improvements.

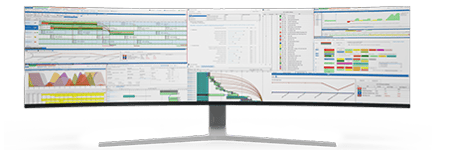
Leveraging PlanetTogether for Risk Management and Quality Assurance
As quality and risk management become increasingly data-driven, the integration of advanced planning systems like PlanetTogether with ERP platforms (SAP, Oracle, Microsoft, Kinaxis, Aveva) has become critical. Here’s how such integrations help Production Planners manage risk and assure quality:
Enhanced Visibility Across Production Phases
When PlanetTogether is integrated with ERP systems, planners gain comprehensive visibility over the production pipeline. This visibility allows them to:
Track real-time inventory levels and prevent material shortages that could lead to rushed or compromised production cycles.
Monitor work-in-progress (WIP) stages to detect quality deviations or potential bottlenecks.
Maintain transparency with the supply chain to mitigate potential risks tied to material sourcing and lead times.
With greater control over each phase of production, planners can proactively manage both quality and risk, ensuring that production flows smoothly without interruptions.
Predictive Quality Assurance with Data Analytics
Integrated systems enable Production Planners to apply predictive analytics to detect potential quality issues before they arise. PlanetTogether, combined with data from ERP systems, allows planners to:
Analyze historical data to pinpoint patterns or trends that signal potential quality deviations.
Set quality checkpoints based on real-time data, allowing for mid-process adjustments that help maintain product integrity.
Utilize predictive maintenance insights to ensure machinery is in optimal condition, reducing the risk of defects due to equipment malfunction.
For instance, by integrating PlanetTogether with SAP’s analytics capabilities, Production Planners can assess the quality impact of specific raw material suppliers, helping make informed purchasing decisions that prioritize consistent quality.
Optimized Scheduling for Quality Assurance
Maintaining quality in chemical manufacturing often requires careful scheduling to balance production speed with QA measures. PlanetTogether’s scheduling capabilities, when integrated with ERP systems, help Production Planners:
Prioritize production runs based on quality needs and resource availability, ensuring that QA checks are not compromised for the sake of speed.
Schedule preventive maintenance and QA checks into production timelines, reducing the likelihood of defects caused by worn-out equipment or rushed processes.
Account for QA bottlenecks in the planning phase, allowing for smoother transitions and fewer delays during production.
For example, integration between PlanetTogether and Oracle’s ERP system can automatically adjust schedules if a QA checkpoint detects a deviation, preventing the issue from cascading into subsequent production stages.
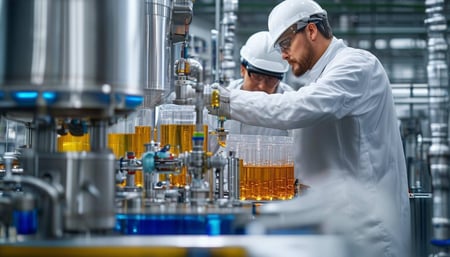
Building a Robust Quality Culture: Integrating People, Process, and Technology
While integrated systems play a significant role, technology alone isn’t enough. A robust quality culture is essential, especially in a highly regulated industry like chemical manufacturing. Production Planners can cultivate this culture by:
Training Teams: Educating staff on the importance of QA and risk management fosters a proactive approach, with team members better able to spot and address issues.
Continuous Improvement: Encouraging feedback from operators and QA teams helps identify improvement opportunities, leading to refined processes.
Alignment Across Departments: Integrating ERP and planning systems enables alignment between production, quality assurance, procurement, and supply chain teams. This alignment creates a unified approach to quality, minimizing communication gaps and delays in addressing issues.
By combining integrated technology with a strong quality culture, Production Planners can create an environment where risk management and QA processes operate seamlessly and support one another.

Practical Steps for Implementing Risk and Quality Strategies with PlanetTogether and ERP Integration
To effectively manage risk and ensure quality in chemical manufacturing, consider these steps to integrate PlanetTogether with ERP systems for optimal results:
Step 1: Define Risk and Quality KPIs
Establish clear KPIs around quality and risk. This might include metrics such as the frequency of quality deviations, downtime due to quality issues, and compliance incident rates. These KPIs should be easily accessible and measurable within both PlanetTogether and the integrated ERP system.
Step 2: Automate Data Capture and Reporting
Automated data capture from ERP systems enables real-time reporting and analytics, making it easier to track and respond to risks. Integrating ERP with PlanetTogether helps streamline data flow, ensuring planners have the latest information on production variables that affect quality and risk.
Step 3: Use Scenario Planning to Simulate Risk Outcomes
With PlanetTogether’s scenario planning capabilities, Production Planners can model different production scenarios and assess their impact on quality and risk. For instance, planners can simulate the effects of using alternative materials or adjusting production speeds, providing a low-risk environment to explore potential changes.
Step 4: Implement Continuous Quality Feedback Loops
By creating a feedback loop between production and QA data, planners can use historical quality data to refine future production runs. This continuous improvement process helps pinpoint the root causes of quality issues, reduce rework, and strengthen quality control over time.
The ongoing digital transformation in manufacturing is making it easier for Production Planners to adopt comprehensive risk management and QA strategies. With the right combination of technology, data, and processes, planners can move beyond traditional quality checks and embrace a proactive approach that anticipates and prevents issues.
By integrating PlanetTogether with ERP systems such as SAP, Oracle, Microsoft, Kinaxis, or Aveva, Production Planners in chemical manufacturing can build a solid foundation for risk management and quality assurance, paving the way for consistent, high-quality production that meets both regulatory requirements and market demands.
Production Planners are the stewards of both risk management and quality assurance in chemical manufacturing. With the aid of integrated planning and ERP systems, they can harness real-time data, predictive insights, and seamless scheduling to protect their organization from quality lapses and operational risks, creating a safer, more efficient, and quality-focused production environment.
Are you ready to take your manufacturing operations to the next level? Contact us today to learn more about how PlanetTogether can help you achieve your goals and drive success in your industry.