Supplier Quality Management in Packaging Production
The role of a Production Planner is pivotal in packaging manufacturing, where precision, efficiency, and quality are essential. Ensuring seamless operations and meeting the demands of clients requires a keen eye for detail and a robust strategy. One critical aspect that often separates the best from the rest is Supplier Quality Management (SQM).
In this blog, we'll look into the significance of SQM, its challenges, and how integrating advanced planning tools like PlanetTogether with leading ERP, SCM, and MES systems can revolutionize the way packaging facilities manage supplier quality.

Supplier Quality Management (SQM)
Supplier Quality Management encompasses the processes and systems used to ensure that the materials and components sourced from suppliers meet the required quality standards. For packaging manufacturers, where raw materials directly impact the final product's quality, SQM plays a vital role in maintaining consistency and reliability.
Challenges in SQM
Despite its importance, SQM poses several challenges for Production Planners:
Variability in Supplier Performance: Suppliers may deliver materials that vary in quality, consistency, or timeliness, leading to disruptions in production schedules.
Compliance and Regulatory Requirements: Packaging materials often need to comply with specific regulations and standards, adding complexity to SQM processes.
Communication and Collaboration: Coordinating with multiple suppliers and internal stakeholders while ensuring transparency and accountability can be daunting.
Data Management: Gathering, analyzing, and managing vast amounts of data related to supplier performance and quality can be time-consuming and error-prone.

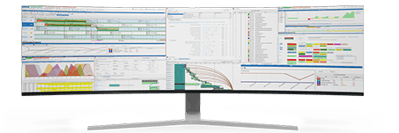
The Role of Advanced Planning Tools
Integrated planning tools like PlanetTogether, coupled with leading ERP, SCM, and MES systems, offer a comprehensive solution to overcome SQM challenges. Let's explore how:
Real-time Data Integration: By integrating with ERP systems like SAP, Oracle, or Microsoft Dynamics, PlanetTogether can access real-time data on inventory levels, production schedules, and supplier performance. This enables Production Planners to make informed decisions based on up-to-date information.
Forecasting and Demand Planning: Advanced planning tools leverage historical data and predictive analytics to forecast demand accurately. By integrating with SCM systems like Kinaxis or Aveva, Production Planners can optimize inventory levels and proactively address supply chain disruptions, reducing the risk of stockouts or overstock situations.
Supplier Collaboration and Transparency: MES systems facilitate seamless communication and collaboration with suppliers by providing a centralized platform for sharing specifications, quality requirements, and performance metrics. This transparency fosters trust and accountability among all stakeholders, leading to improved SQM.
Quality Control and Compliance: Integrated systems enable automated quality control processes, ensuring that materials meet the required standards and regulatory requirements. MES systems play a crucial role in tracking and documenting quality inspections, audits, and certifications, streamlining SQM processes and reducing compliance risks.
Benefits of Integrated SQM
The integration between PlanetTogether and ERP, SCM, and MES systems offers numerous benefits for Packaging Production Planners:
Enhanced Visibility and Control: Real-time access to data from across the supply chain enables Production Planners to anticipate issues, identify bottlenecks, and make proactive decisions to optimize production schedules and resource utilization.
Improved Quality and Consistency: By standardizing processes and enforcing quality standards across suppliers, integrated SQM systems help ensure consistent product quality, reducing the risk of defects or recalls.
Cost Savings and Efficiency: Streamlined SQM processes lead to reduced lead times, lower inventory carrying costs, and fewer production delays, resulting in cost savings and improved operational efficiency.
Strategic Insights and Continuous Improvement: Advanced analytics and reporting capabilities provide valuable insights into supplier performance trends, enabling Production Planners to identify areas for improvement and drive continuous process optimization.
Supplier Quality Management is a critical aspect of packaging manufacturing that directly impacts product quality, customer satisfaction, and operational efficiency. By integrating advanced planning tools like PlanetTogether with leading ERP, SCM, and MES systems, Production Planners can overcome SQM challenges, enhance visibility and control, and drive continuous improvement across the supply chain.
Embracing integrated SQM not only ensures consistent quality and reliability but also positions packaging manufacturers for long-term success in an increasingly competitive market landscape.
Are you ready to take your manufacturing operations to the next level? Contact us today to learn more about how PlanetTogether can help you achieve your goals and drive success in your industry.
LEAVE A COMMENT