AI-Driven Predictive Maintenance for Material Handling Systems
As a production scheduler, you understand the intricate dance of coordinating resources, optimizing processes, and meeting tight deadlines. One critical aspect of this puzzle is ensuring the smooth operation of material handling systems. Any downtime in these systems can lead to costly delays and disruptions in production.
Traditionally, maintenance of material handling systems has been a reactive endeavor, relying on manual inspections and repairs after breakdowns occur. However, with the advent of artificial intelligence (AI) and predictive analytics, a paradigm shift is underway. By harnessing the power of data and machine learning algorithms, production schedulers can now predict and prevent equipment failures before they happen, thus minimizing downtime and maximizing efficiency.
In this blog, we'll explore the potential of AI-driven predictive maintenance for material handling systems in food and beverage manufacturing facilities. Specifically, we'll delve into how integration between advanced planning and scheduling (APS) software like PlanetTogether and enterprise resource planning (ERP), supply chain management (SCM), and manufacturing execution systems (MES) such as SAP, Oracle, Microsoft, Kinaxis, and Aveva can unlock new levels of operational excellence.
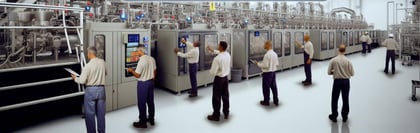
Predictive Maintenance
Predictive maintenance is a proactive maintenance strategy that leverages data analysis, machine learning, and AI to predict when equipment is likely to fail. By continuously monitoring the condition of machinery and analyzing historical performance data, predictive maintenance algorithms can identify patterns and anomalies indicative of impending failures. This allows maintenance teams to intervene preemptively, scheduling repairs or replacements at the most opportune times to minimize downtime and maximize asset lifespan.
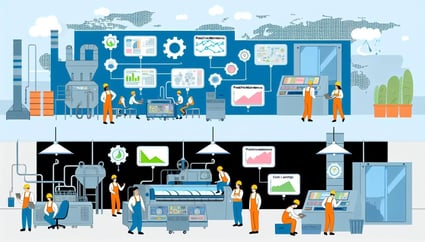
The Benefits of Predictive Maintenance
Reduced Downtime: Perhaps the most significant advantage of predictive maintenance is its ability to minimize unplanned downtime. By addressing potential issues before they escalate into failures, production interruptions can be minimized, ensuring a smooth flow of operations.
Cost Savings: Predictive maintenance helps companies avoid costly repairs and emergency maintenance expenses associated with unexpected breakdowns. By replacing components proactively and scheduling maintenance during planned downtimes, organizations can optimize maintenance budgets and reduce overall operational costs.
Extended Asset Lifespan: By identifying and addressing issues early, predictive maintenance can help extend the lifespan of material handling equipment. This not only reduces the frequency of costly replacements but also ensures that assets operate at peak performance levels for longer periods.
Improved Safety: Well-maintained equipment is inherently safer to operate. By proactively addressing potential safety hazards through predictive maintenance, companies can create a safer working environment for employees and minimize the risk of accidents or injuries.
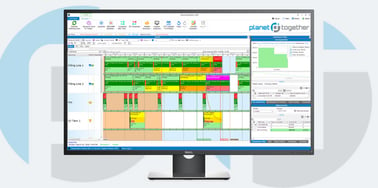
Integration with APS and ERP Systems
Now, let's explore how the integration of AI-driven predictive maintenance with advanced planning and scheduling (APS) software like PlanetTogether and ERP, SCM, and MES systems can further enhance the efficiency and effectiveness of maintenance operations in food and beverage manufacturing facilities.
Real-Time Data Exchange: Integration between predictive maintenance systems and APS/ERP platforms enables seamless exchange of real-time data. This ensures that maintenance schedules are aligned with production plans, allowing maintenance activities to be prioritized based on production priorities and resource availability.
Optimized Resource Allocation: By leveraging data from APS and ERP systems, predictive maintenance algorithms can factor in production schedules, resource constraints, and inventory levels when generating maintenance plans. This enables more intelligent resource allocation, ensuring that maintenance activities are performed with minimal disruption to ongoing production processes.
Improved Forecasting Accuracy: APS and ERP systems provide valuable insights into demand forecasts, production schedules, and inventory levels. By incorporating this data into predictive maintenance models, manufacturers can enhance the accuracy of failure predictions and optimize maintenance schedules accordingly.
Enhanced Decision-Making: Integration between predictive maintenance and APS/ERP systems empowers production schedulers with actionable insights. By providing visibility into the impact of maintenance activities on production schedules and resource utilization, manufacturers can make more informed decisions to balance maintenance requirements with production goals.
AI-driven predictive maintenance represents a game-changer for food and beverage manufacturing facilities looking to optimize material handling systems and maximize operational efficiency. By integrating advanced planning and scheduling (APS) software like PlanetTogether with ERP, SCM, and MES systems, manufacturers can unlock new levels of predictive insight and operational excellence.
As a production scheduler, embracing predictive maintenance technologies and leveraging the power of data-driven decision-making can help you streamline maintenance operations, reduce downtime, and ensure a smooth flow of production. By staying ahead of equipment failures and proactively addressing maintenance needs, you can contribute to the overall success and competitiveness of your organization in the dynamic landscape of food and beverage manufacturing.
Are you ready to take your manufacturing operations to the next level? Contact us today to learn more about how PlanetTogether can help you achieve your goals and drive success in your industry.