Restructuring the Supply Base
As a Supply Chain Manager, you understand the intricacies involved in orchestrating the movement of goods from farm to fork efficiently. One key strategy that can significantly enhance your supply chain's agility and competitiveness is restructuring the supply base.
In this blog, we'll look into the importance of supply base restructuring and how integrating Planettogether with leading ERP solutions like SAP, Oracle, Microsoft, Kinaxis, or Aveva can revolutionize your operations.
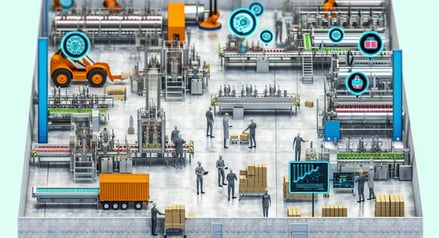
Why Restructure the Supply Base?
The traditional approach to supply chain management often involves dealing with multiple suppliers for various components or ingredients. While this approach may have worked in the past, the complexities of today's global marketplace demand a more streamlined and integrated supply base.
Restructuring the supply base involves consolidating suppliers, forging strategic partnerships, and leveraging technology to optimize procurement processes. By doing so, food and beverage manufacturers can:
Enhance supply chain visibility: Consolidating suppliers allows for better visibility into the entire supply chain network, from source to shelf. This visibility enables proactive risk management and better decision-making.
Improve quality and consistency: Working closely with a select group of suppliers fosters stronger relationships and enables manufacturers to enforce rigorous quality standards. This, in turn, ensures consistency in product quality, which is crucial in the food and beverage industry.
Increase agility and responsiveness: A streamlined supply base enhances agility by reducing lead times and simplifying the procurement process. This agility is vital for quickly responding to changing consumer demands and market trends.

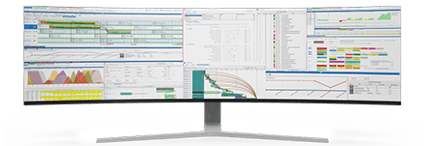
Integration with Leading ERP Solutions
To effectively restructure the supply base, seamless integration between supply chain planning software like Planettogether and ERP systems is essential. Let's explore how integration with leading ERP solutions can amplify the benefits of restructuring:
SAP Integration: SAP's ERP solutions offer robust capabilities for managing various aspects of the supply chain, from procurement to production planning. By integrating Planettogether with SAP, Supply Chain Managers can achieve real-time visibility into inventory levels, demand forecasts, and production schedules. This integration enables more accurate planning and execution, ultimately leading to cost savings and improved customer satisfaction.
Oracle Integration: Oracle's suite of ERP applications provides comprehensive tools for supply chain management, including procurement, inventory management, and logistics. By integrating Planettogether with Oracle ERP, manufacturers can optimize inventory levels, reduce stockouts, and minimize carrying costs. The seamless flow of data between the two systems facilitates collaborative planning and ensures alignment between supply and demand.
Microsoft Integration: Microsoft's ERP solutions, such as Dynamics 365 Supply Chain Management, offer flexible and scalable options for managing complex supply chains. Integrating Planettogether with Microsoft ERP empowers Supply Chain Managers with end-to-end visibility and control over their operations. From demand forecasting to production scheduling, this integration enables efficient resource allocation and better decision-making.
Kinaxis Integration: Kinaxis RapidResponse is a leading supply chain planning platform known for its agility and responsiveness. By integrating Planettogether with Kinaxis, manufacturers can achieve a holistic view of their supply chain dynamics and simulate various scenarios to optimize resource utilization. This integration facilitates collaborative planning across departments and ensures alignment with business objectives.
Aveva Integration: Aveva's comprehensive suite of manufacturing solutions offers advanced capabilities for optimizing production processes and improving operational efficiency. Integrating Planettogether with Aveva enables seamless data exchange between production planning and execution systems, ensuring synchronized operations and timely delivery of products to market.
Restructuring the supply base is a strategic imperative for food and beverage manufacturers looking to enhance their competitive advantage in the market. By consolidating suppliers and integrating supply chain planning software like Planettogether with leading ERP solutions, Supply Chain Managers can achieve greater visibility, agility, and responsiveness across their operations.
Embracing this transformative approach to supply chain management will not only drive cost savings but also foster innovation and customer satisfaction in an increasingly dynamic industry landscape.
Are you ready to take your manufacturing operations to the next level? Contact us today to learn more about how PlanetTogether and integrated scheduling solutions can help you achieve your sustainability goals and drive success in the food and beverage industry.
LEAVE A COMMENT