Reshaping Traditional Manufacturing Models
Traditional models are undergoing a significant transformation driven by the relentless march of technology. As Industry 4.0 continues to revolutionize manufacturing processes, the integration of advanced software solutions becomes essential for chemical companies to stay competitive and agile in the market.
In this blog, we look into the crucial role of integrated systems, focusing on the convergence between PlanetTogether—a leading production planning and scheduling software—and prominent ERP, SCM, and MES systems like SAP, Oracle, Microsoft, Kinaxis, and Aveva. By exploring the benefits, challenges, and best practices of such integrations, we aim to provide insights into reshaping traditional manufacturing models in the chemical industry.

The Evolution of Manufacturing Models
Traditional manufacturing models in the chemical industry have long relied on siloed systems and manual processes, leading to inefficiencies, production bottlenecks, and limited agility in responding to market demands. However, the advent of digital technologies has paved the way for a paradigm shift towards interconnected and data-driven manufacturing ecosystems.
Industry 4.0 technologies offer a myriad of opportunities, from predictive analytics and IoT sensors to cloud computing and artificial intelligence, empowering manufacturers to optimize operations, enhance productivity, and drive innovation. At the heart of this transformation lies the integration of disparate systems, enabling seamless communication and data exchange across the entire value chain.
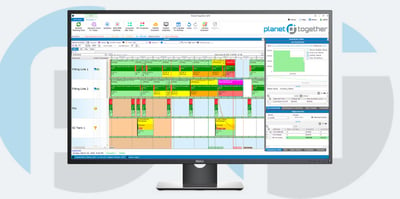
Integration between PlanetTogether and ERP, SCM, and MES Systems
PlanetTogether stands out as a comprehensive production planning and scheduling software designed to optimize manufacturing processes, minimize lead times, and maximize resource utilization. However, its true potential is realized when integrated with enterprise resource planning (ERP), supply chain management (SCM), and manufacturing execution systems (MES), thereby creating a unified ecosystem that synchronizes planning, execution, and monitoring activities.
Let's look into the integration capabilities and benefits of PlanetTogether with some of the leading systems in the industry:
SAP Integration: SAP, a stalwart in the ERP domain, offers robust functionalities for finance, procurement, and inventory management. By integrating PlanetTogether with SAP, chemical manufacturers can achieve real-time visibility into production schedules, material requirements, and capacity constraints. This integration facilitates seamless data exchange, enabling agile decision-making and optimized resource allocation.
Oracle Integration: Oracle's comprehensive suite of SCM solutions complements PlanetTogether's planning capabilities by providing end-to-end visibility across the supply chain. Integration between PlanetTogether and Oracle enables manufacturers to synchronize production plans with procurement, warehousing, and logistics operations, ensuring on-time delivery and cost-effective inventory management.
Microsoft Integration: Microsoft Dynamics offers a versatile platform for ERP and CRM functionalities, empowering businesses with scalability and flexibility. By integrating PlanetTogether with Microsoft Dynamics, chemical manufacturers can streamline order management, improve forecast accuracy, and enhance customer satisfaction. This integration fosters collaboration across departments, enabling a cohesive approach towards meeting customer demands.
Kinaxis Integration: Kinaxis RapidResponse is renowned for its advanced analytics and scenario planning capabilities in the SCM domain. Integration between PlanetTogether and Kinaxis enables manufacturers to perform holistic simulations, assess the impact of demand fluctuations, and proactively adjust production schedules. This integration fosters agility and resilience in the face of market uncertainties, ensuring continuity in operations.
Aveva Integration: Aveva's MES solutions offer comprehensive functionalities for production monitoring, quality management, and compliance. By integrating PlanetTogether with Aveva, chemical manufacturers can achieve real-time visibility into shop floor activities, track production performance metrics, and enforce regulatory compliance. This integration enhances operational efficiency, reduces downtime, and improves overall equipment effectiveness (OEE).
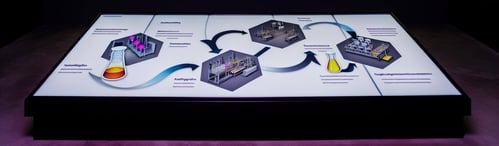
Challenges and Best Practices
While the integration of PlanetTogether with ERP, SCM, and MES systems offers compelling benefits, it is not without its challenges. Data compatibility issues, disparate architectures, and varying implementation timelines can pose hurdles during the integration process. Therefore, it is essential for manufacturers to adopt best practices to ensure successful integration:
Define Clear Objectives: Clearly define the objectives and expected outcomes of the integration project, aligning them with the overarching business goals and KPIs.
Collaborative Approach: Foster collaboration between IT, operations, and business stakeholders to ensure a holistic understanding of requirements and priorities.
Data Standardization: Establish data standardization protocols to harmonize data formats, terminology, and structures across integrated systems.
Continuous Monitoring: Implement robust monitoring mechanisms to track the performance of integrated systems, identify bottlenecks, and implement corrective actions proactively.
Scalability and Flexibility: Design integration solutions with scalability and flexibility in mind, anticipating future growth and evolving business needs.
The integration of PlanetTogether with ERP, SCM, and MES systems represents a pivotal step towards reshaping traditional manufacturing models in the chemical industry. By leveraging the synergies between advanced software solutions, manufacturers can unlock new efficiencies, enhance agility, and drive sustainable growth in an increasingly competitive landscape.
Embracing integration is not merely a technological imperative but a strategic imperative for companies seeking to thrive in the digital age of manufacturing. As we navigate the complexities of the modern manufacturing ecosystem, integration emerges as the cornerstone of transformation, enabling us to build resilient, adaptive, and future-ready operations.
Are you ready to take your manufacturing operations to the next level? Contact us today to learn more about how PlanetTogether can help you achieve your goals and drive success in your industry.
LEAVE A COMMENT