Reinforcement Learning for Adaptive Scheduling
The packaging industry is a dynamic and ever-evolving sector where efficiency, speed, and adaptability are critical factors for success. As manufacturing IT professionals in a packaging manufacturing facility, you're well aware of the challenges that come with managing complex production schedules, ensuring optimal resource utilization, and meeting customer demands.
In this blog, we will explore the potential of reinforcement learning for adaptive scheduling and its integration with Enterprise Resource Planning (ERP), Supply Chain Management (SCM), and Manufacturing Execution Systems (MES) in the context of the packaging industry.
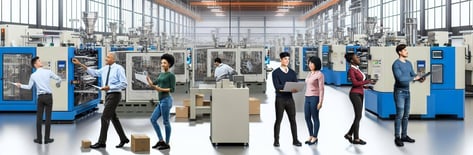
The Need for Adaptive Scheduling
Traditional scheduling approaches in manufacturing, including packaging, often rely on fixed, predetermined schedules that are based on historical data and forecasts. While these methods can work well under stable conditions, they struggle to adapt to unexpected disruptions, machine breakdowns, or changes in customer orders. This is where adaptive scheduling comes into play.
Adaptive scheduling leverages real-time data and advanced algorithms to adjust production schedules on the fly. It allows manufacturers to respond quickly to changing circumstances, minimize downtime, reduce production costs, and improve overall efficiency. In recent years, reinforcement learning has emerged as a powerful tool for implementing adaptive scheduling solutions.
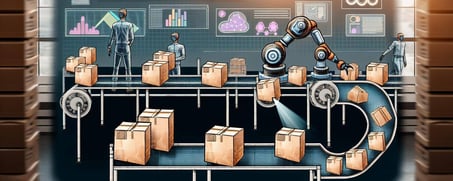
Reinforcement Learning: An Overview
Reinforcement learning (RL) is a subset of machine learning that focuses on training agents to make sequential decisions in an environment to maximize a cumulative reward. Unlike supervised learning, where the model learns from labeled data, RL involves learning through interaction with an environment and receiving feedback in the form of rewards or penalties.
In the context of adaptive scheduling, RL can be used to develop intelligent scheduling agents that continuously learn and adapt to dynamic manufacturing conditions. These agents can optimize production schedules by considering factors such as machine availability, order priorities, resource constraints, and delivery deadlines.

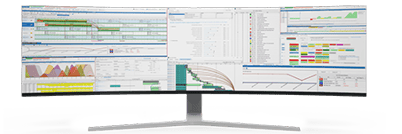
PlanetTogether Integration
One of the leading software solutions for advanced production planning and scheduling is PlanetTogether. Integrating PlanetTogether with your existing ERP, SCM, and MES systems can yield significant benefits in terms of adaptive scheduling.
PlanetTogether's advanced scheduling algorithms can be enhanced with reinforcement learning agents. Here's how it can work:
Data Integration
PlanetTogether seamlessly integrates with your ERP system to access data on customer orders, inventory levels, and material availability.
It also connects with MES to monitor real-time machine statuses and production progress.
RL-Based Scheduling Agent
A reinforcement learning-based scheduling agent is embedded within the PlanetTogether platform.
This agent continuously learns from historical data and real-time inputs, optimizing production schedules accordingly.
Adaptive Decision-Making
The RL agent considers various factors, such as machine downtime, resource constraints, and order priorities, to make adaptive scheduling decisions.
It adapts to changes in demand and production conditions in real time, ensuring efficient resource utilization.
Monitoring and Reporting
PlanetTogether provides a user-friendly interface for monitoring and reporting on the adaptive scheduling process.
Managers can gain insights into scheduling decisions, resource utilization, and production performance.
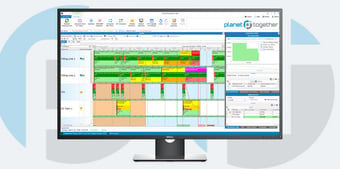
Benefits of Integration with PlanetTogether
The integration of PlanetTogether with reinforcement learning-based adaptive scheduling offers several advantages for packaging manufacturers:
Increased Efficiency
Adaptive scheduling ensures that production resources are utilized efficiently, minimizing downtime and reducing operational costs.
Improved Customer Satisfaction
Meeting delivery deadlines and responding to changing customer demands results in higher customer satisfaction and loyalty.
Enhanced Resource Management
Real-time visibility into machine and resource statuses enables proactive maintenance and resource allocation.
Reduced Lead Times
Adaptive scheduling can significantly reduce lead times, allowing you to respond quickly to market fluctuations and emerging opportunities.
Better Decision Support
Data-driven insights from integrated systems help manufacturing IT professionals make informed decisions and optimize processes further.
Challenges and Considerations
While the integration of reinforcement learning-based adaptive scheduling with ERP, SCM, and MES systems holds great promise, it's important to be aware of certain challenges:
Data Quality
Reliable data is essential for effective RL training and decision-making. Ensure data accuracy and consistency across integrated systems.
Training Time
RL models may require significant training time to become proficient. Initial implementation may involve a learning curve.
Change Management
Adaptation to new scheduling methods and processes may require organizational adjustments and employee training.
Scalability
Ensure that the integrated solution can scale with the growing needs of your packaging manufacturing facility.
The packaging industry is evolving rapidly, and manufacturers need to stay agile and adaptive to remain competitive. Reinforcement learning-based adaptive scheduling, when integrated with ERP, SCM, and MES systems, can provide the flexibility and efficiency needed to thrive in this dynamic environment.
By harnessing the power of intelligent scheduling agents, such as those integrated with PlanetTogether, packaging manufacturers can optimize resource utilization, improve customer satisfaction, reduce lead times, and make data-driven decisions. As manufacturing IT professionals, embracing these innovations and exploring integration possibilities can lead to a more resilient and profitable packaging manufacturing facility. Stay ahead of the curve and revolutionize your scheduling processes with reinforcement learning.
Are you ready to take your manufacturing operations to the next level? Contact us today to learn more about how PlanetTogether can help you achieve your goals and drive success in your industry.