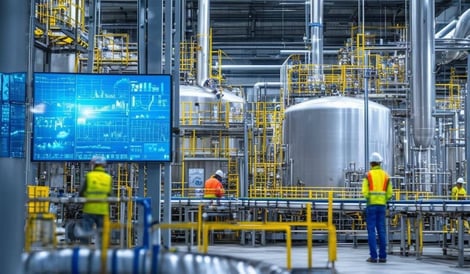
Reducing Cycle Times in Chemical Manufacturing
In chemical manufacturing, reducing cycle times is a priority for staying competitive. With the global demand for chemical products on the rise and supply chain complexities increasing, production schedulers play a pivotal role in optimizing manufacturing processes to ensure timely delivery without compromising quality.
In this blog, we’ll explore strategies for reducing cycle times and how integrating advanced planning and scheduling (APS) tools like PlanetTogether with enterprise systems such as SAP, Oracle, Microsoft, Kinaxis, or Aveva can unlock significant operational efficiencies.
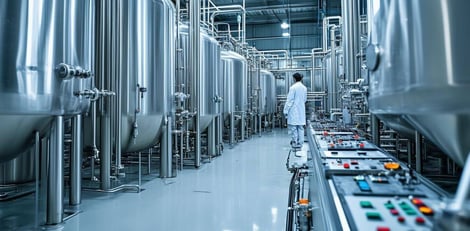
Cycle Time in Chemical Manufacturing
Cycle time refers to the total time it takes for a product to move from the beginning to the end of the production process. This includes raw material preparation, processing, quality checks, and packaging. In chemical manufacturing, where processes are often continuous or batch-based, even minor inefficiencies can significantly impact cycle time.
Key drivers that contribute to extended cycle times in chemical manufacturing include:
Manual Scheduling and Data Management: Relying on spreadsheets or siloed systems makes it challenging to adjust schedules dynamically.
Resource Constraints: Limited availability of equipment or skilled personnel can lead to delays.
Unplanned Downtime: Equipment failures or maintenance issues often interrupt production.
Complex Product Mix: Balancing different production orders with varying requirements can create bottlenecks.
Inefficient Changeovers: Prolonged equipment setup and cleaning times between batches slow production.
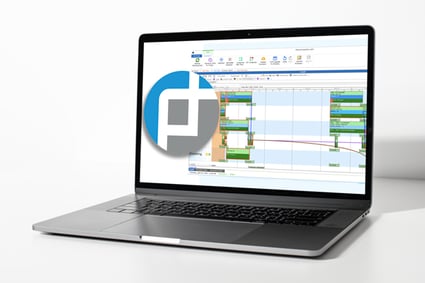
Strategies for Reducing Cycle Times
Streamlining Scheduling Processes
Automated scheduling systems like PlanetTogether help eliminate the inefficiencies of manual scheduling. By integrating with ERP systems such as SAP or Oracle, production schedulers can synchronize demand forecasts, inventory levels, and resource availability in real time. This enables the creation of optimal schedules that reduce idle time and improve throughput.
Example: A chemical plant producing adhesives integrated PlanetTogether with SAP. By automating schedule adjustments based on real-time data, the plant reduced idle time by 20% and improved order fulfillment rates.
Optimizing Resource Utilization
Production schedulers must ensure that equipment and personnel are utilized to their fullest potential. APS tools like PlanetTogether provide visibility into resource availability, enabling better allocation and minimizing underutilization or overbooking.
Integration Insight: By connecting PlanetTogether with Microsoft Dynamics 365, schedulers can access live data on equipment status and personnel availability. This integration ensures that every resource is used effectively, preventing bottlenecks and reducing cycle times.
Reducing Changeover Times
In chemical manufacturing, frequent changeovers between batches can significantly impact cycle time. APS tools provide insights into production sequences and suggest batch groupings to minimize changeovers. For example, grouping products with similar formulations can reduce cleaning and setup times.
Integration Highlight: Using PlanetTogether with Aveva’s production management software, a specialty chemicals manufacturer identified opportunities to group similar orders, cutting changeover times by 30%.
Improving Maintenance Scheduling
Unplanned downtime is a major contributor to extended cycle times. Integrating maintenance data from ERP systems into scheduling platforms allows production schedulers to incorporate planned maintenance into their schedules proactively.
Real-World Scenario: A plant integrated PlanetTogether with Oracle E-Business Suite to combine production and maintenance schedules. This holistic view reduced unplanned downtime by 15%, leading to faster cycle times.
Implementing Real-Time Monitoring and Adjustments
Chemical manufacturing often requires rapid responses to changing conditions, such as equipment issues or raw material shortages. Integrating APS tools with systems like Kinaxis provides real-time updates, allowing schedulers to make on-the-fly adjustments.
Case Study: A petrochemical company integrated PlanetTogether with Kinaxis RapidResponse to monitor supply chain disruptions and adapt production schedules in real time. This agility reduced cycle times by 12%.
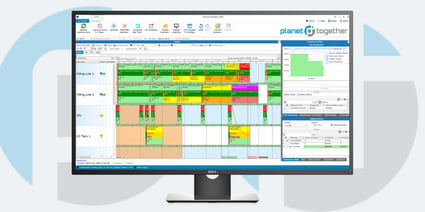
The Role of Advanced Integration in Reducing Cycle Times
Visibility Across Systems
Integrating PlanetTogether with ERP systems provides a single source of truth for production data. This eliminates the need for manual data consolidation and ensures that schedulers work with the most accurate and up-to-date information.
Enhanced Decision-Making
With advanced analytics and predictive capabilities, integrated systems can highlight potential bottlenecks before they occur. For example, if an unexpected delay in raw material delivery is detected, the system can suggest alternative schedules to minimize disruptions.
Improved Collaboration
Integration fosters better communication between departments. For instance, connecting PlanetTogether with Aveva’s solutions can align production schedules with engineering and quality control, ensuring smoother workflows.
For production schedulers in chemical manufacturing, reducing cycle times is not just a goal—it’s a requirement to stay competitive in today’s fast-paced market. By adopting strategies like automated scheduling, resource optimization, and proactive maintenance, and leveraging the power of integrations between tools like PlanetTogether and ERP systems such as SAP, Oracle, Microsoft, Kinaxis, or Aveva, schedulers can drive significant improvements in efficiency and productivity.
The path to shorter cycle times begins with leveraging the right technology and fostering collaboration across the production ecosystem. With integrated tools at your disposal, the possibilities for streamlining operations and achieving manufacturing excellence are endless.
Are you ready to take your manufacturing operations to the next level? Contact us today to learn more about how PlanetTogether can help you achieve your goals and drive success in your industry.