Real-Time Demand Orchestration
Production schedulers in food and beverage manufacturing are tasked with the crucial responsibility of orchestrating demand in real-time, ensuring that production processes are optimized to meet customer needs while minimizing waste and maximizing profitability.
In this blog, we'll explore the concept of real-time demand orchestration and how integrating solutions like PlanetTogether with leading ERP, SCM, and MES systems can revolutionize your production scheduling processes.
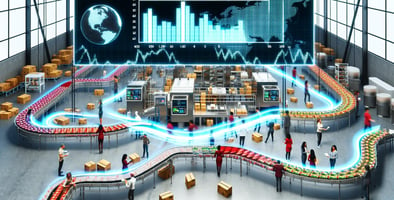
Understanding Real-Time Demand Orchestration
Real-time demand orchestration involves synchronizing production activities with fluctuating customer demand to ensure timely delivery of products while minimizing costs and maximizing resource utilization. It requires a holistic approach that integrates data from various sources, including customer orders, inventory levels, production capacity, and supply chain dynamics.
Traditional production scheduling methods often rely on static plans that are updated periodically, leading to inefficiencies and missed opportunities. Real-time demand orchestration, on the other hand, leverages advanced technologies and predictive analytics to continuously monitor and adjust production schedules in response to changing demand signals.
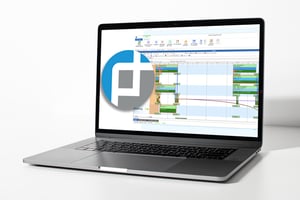
The Role of Integrated Solutions
One of the key enablers of real-time demand orchestration is the integration of production scheduling software like PlanetTogether with enterprise resource planning (ERP), supply chain management (SCM), and manufacturing execution systems (MES). By connecting these systems, production schedulers gain access to a wealth of real-time data and actionable insights that enable them to make informed decisions quickly.
Integration with ERP Systems
ERP systems serve as the backbone of many food and beverage manufacturing facilities, managing core business processes such as order management, inventory control, and financials. By integrating with ERP systems like SAP, Oracle, or Microsoft Dynamics, production schedulers can ensure that production schedules are aligned with customer orders and inventory levels in real-time.
For example, when a new customer order is received in the ERP system, the integrated solution automatically updates the production schedule in PlanetTogether, taking into account factors such as available inventory, production capacity, and lead times. This seamless integration streamlines the order-to-delivery process and helps avoid stockouts or overproduction.
Integration with SCM Systems
Supply chain management (SCM) systems play a crucial role in coordinating the flow of materials and information across the entire supply chain, from raw material suppliers to end customers. By integrating with SCM systems like Kinaxis or Aveva, production schedulers can gain visibility into upstream and downstream supply chain activities, allowing them to proactively adjust production schedules in response to supply chain disruptions or changes in demand forecasts.
For example, if a key raw material supplier experiences a delay in delivery, the integrated solution can automatically adjust the production schedule to prioritize the use of alternative materials or reschedule production to minimize the impact on customer orders. This agility is essential in today's volatile and unpredictable business environment.
Integration with MES Systems
Manufacturing execution systems (MES) play a critical role in managing shop floor operations, including work orders, production tracking, and quality control. By integrating with MES systems, production schedulers can ensure that production schedules are synchronized with actual shop floor activities in real-time, allowing for greater accuracy and efficiency.
For example, as production orders are completed on the shop floor, the MES system provides real-time updates on production progress, including actual cycle times, downtime events, and quality issues. This information is fed back into the production scheduling system, enabling production schedulers to dynamically adjust schedules based on actual performance data and minimize idle time or bottlenecks.
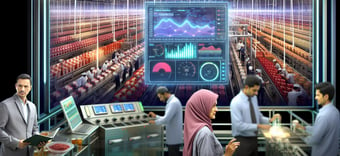
Benefits of Real-Time Demand Orchestration
The integration of production scheduling software with ERP, SCM, and MES systems offers a host of benefits for food and beverage manufacturers:
Improved Customer Service: By aligning production schedules with customer demand in real-time, manufacturers can ensure on-time delivery and meet customer expectations more consistently.
Reduced Costs: Real-time demand orchestration helps minimize inventory carrying costs, production downtime, and waste by optimizing production schedules based on actual demand and resource availability.
Enhanced Agility: Integrated solutions enable manufacturers to respond quickly to changing market conditions, supply chain disruptions, or customer requirements, ensuring greater agility and competitiveness.
Better Decision-Making: By providing production schedulers with real-time visibility into key performance metrics and actionable insights, integrated solutions empower them to make informed decisions quickly and effectively.
Increased Efficiency: Automation and optimization capabilities inherent in integrated solutions help streamline production processes, eliminate manual errors, and improve overall operational efficiency.
Real-time demand orchestration is no longer a luxury but a necessity for food and beverage manufacturers looking to thrive in today's competitive marketplace. By integrating production scheduling software like PlanetTogether with leading ERP, SCM, and MES systems, production schedulers can achieve unprecedented levels of efficiency, agility, and customer satisfaction.
The ability to synchronize production activities with fluctuating demand in real-time enables manufacturers to stay ahead of the curve and drive sustainable growth in an ever-changing industry landscape. Are you ready to take your manufacturing operations to the next level? Contact us today to learn more about how PlanetTogether can help you achieve your goals and drive success in your industry.